What is Plasma Electrolytic Oxidation?
16 February 2021Plasma electrolytic oxidation (PEO), also known as micro-arc oxidation (MAO), is a surface coating technology that produces multiple ceramic layers on the surface of light metals, valve metals and their alloys. Uniquely, the porous outer layer enables materials scientists and engineers to impregnate different reagents that customise the performance characteristics of the coating. Surface coatings formed through plasma electrolytic oxidation deliver two to four times the hardness of hard anodising or steel.
The basic PEO process uses an electrolyte bath of a proprietary dilute aqueous solution, with additional reagents according to the desired surface coating properties. A high voltage, typically 200V or higher, is passed through the electrolyte and the high potentials generate plasma discharges on the substrate’s surface, as shown in this video. The plasma in turn provides the ideal conditions of high temperature and pressure that forms a mainly crystalline oxide from the light metal substrate.
Electrolytic oxidation without the use of plasma - anodising – is a mature and well-established technique. It is the introduction of plasma that fundamentally alters the coating and performance characteristics in end-use applications. The use of plasma introduces multiple benefits that include:
- The development of harder ceramic phases, including crystallisation
- Chemical passivity - most PEO ceramics are chemically inert
- The impregnation of elements from the electrolyte into the porous outer layer that deliver many different properties
- Reduced stiffness gives high adhesion under mechanical strain or thermal cycling
- Crack-free edges
PEO surface coatings are distinctive because of their wear resistance, corrosion resistance and thermal and chemical stability. This unique coating technology is used for the light metals and their alloys, aluminium, magnesium and titanium. It is applied to other metals such as the valve metals zirconium, tantalum, niobium and hafnium, and also cobalt.
How does the plasma electrolytic oxidation (PEO) process work?
The processes involved in PEO are highly flexible, particularly when compared to alternatives such as hard anodising. This delivers a wide range of potential surface coating properties, which can be adapted and tailored to best suit the end use application of a component.
PEO requires less complex equipment than many coating technologies. It requires no high temperature furnace or plasma guns, does not need a vacuum and uses no hazardous substances in its basic form.
Figure 1 below shows the basic equipment required for a research and test installation, with a 25-litre bath, transparent walls for observation and 10kW output. As the process is scalable, Keronite’s industrial scale equipment uses 3500 litre tanks with 300kW capabilities to process larger components for coating.
Figure 1: 80KW machine with a 300L tank
Pre-treatment is simpler for PEO. In many cases, aluminium components may only require a light degrease prior to treatment. By comparison, most anodising and plating processes will need a cleaner surface, necessitating degreasing, etching and desmut steps to ensure a high-quality coating.
The reason behind how PEO can be used to finely tune material properties lies in its unique process. The process generally follows three stages:
Stage 1: Substrate oxidation
The light metal or alloy component is placed into an electrolyte bath. The bath’s composition differs according to the target characteristics of the PEO coating but is usually a proprietary dilute aqueous solution. This is free from chrome and other heavy metals. The solution is disposable and clean, in contrast to other coating technologies.
A high voltage current, typically 200V or greater, is passed through the solution. Depending on the desired coating characteristics, different electrical regimes are used. For example, alternating the polarity of an aluminium substrate delivers variations of growth formation.
Stage 2: Plasma Modification
The increased temperatures on the alloy’s surface caused by the high potentials created by the current within the electrolyte generates a plasma discharge on the substrate’s surface, as shown in figure 2. The plasma in turn provides the ideal conditions of high temperature and pressure that forms a mainly crystalline oxide - corundum, periclase or rutile/anatase in the case of aluminium, magnesium and titanium - from the light metal substrate.
Figure 2: A component immersed in the electrolyte - high potentials created by the current within the electrolyte generates a plasma discharge on the substrate’s surface
In conventional anodising, the coating growth mechanism causes through-thickness cracks or fissures in the protective layer on corners or uneven surfaces, as shown in the left-hand image in figure 3. Additional seals or treatments are necessary to increase the corrosion resistance capabilities of hard anodised components for this reason. These also reduce the fatigue strength of a component, acting as stress raisers.
PEO coatings are characterised by good coverage of the component compared to line-of-sight processes such as painting, powder coating and plasma or flame spray techniques. Also, the insulating properties of the coating ensure good uniformity at corners and edges. Paints tend to thin at corners, whereas electroplating techniques tend to thicken at corners.
Figure 3: Crack free edges mean higher strength and corrosion resistance
With PEO, plasma is used to modify the coating during the growth process. This alters the microstructure, resulting in no through-thickness cracks as the right-hand image in figure 3 shows. This provides consequent benefits in corrosion resistance and fatigue strength. PEO layers are characterised by their complex microstructure. The presence of irregularly shaped microcrystals and other features provides more comprehensive protection on corners than the through-thickness cracks clearly visible in hard anodised coatings.
Plasma modification also creates other attractive features such as chemical passivity, low stiffness and thermal stability.
Stage 3: Incorporation of electrolyte elements into the coating
The plasma modification process enables elements of the electrolyte to be incorporated within the ceramic composition of the layer. This is because uniquely, resulting from the discharges caused by the plasma, the coating’s outer surface is porous.
The discharge pores on the surface structure allow impregnation of the outer layer with performance enhancing reagents. The electrolyte’s composition can be customised to fill, or impregnate, the discharge pores with performance changing materials during the coating process.
The surface caused by the plasma discharge also enables additional coating layers to be applied that adhere strongly to the porous oxide outer layer. This means engineers can select elements to tailor coating properties specifically for the component’s application.
For example, using a silicate-rich electrolyte for the PEO process results in a mullite-rich PEO coating on aluminium alloys. This reduces the thermal conductivity of the PEO coating to 0.5 W/mK. Polyester coatings enhance corrosion and scratch resistance. Figure 4 shows a polyester powder coat adhered to a PEO layer on a magnesium substrate.
Figure 4: Polyester powder coat adhered to a PEO layer on a magnesium substrate
The role of the electrolyte and resultant properties
PEO’s unique and flexible process produces highly protective layers that can be enhanced with performance characteristics designed for specific applications.
Wear resistance and hardness
Applying a high-sliding wear resistant PEO coating improves hardness. Typical aluminium coatings are harder than steel (1600HV vs 500HV – see figure 5), yet the component itself could be up to 66% lighter. The performance enhancing characteristics of PEO coatings have enabled light alloys - even magnesium - to feature in high performance aerospace and automotive applications.
Figure 5: Hardness of PEO layers in pin-on-disc tests
Using polymers, such as PEEK (poly-ether-ether-ketone), in the outer layer introduces a built-in lubricant coating that reduces friction and wear.
High Strain Tolerance
High hardness alone does not necessarily provide comprehensive wear resistance capabilities. Compliance is also a very valuable property, allowing for some deformation of the component under deflection or thermal expansion without placing undue stress into the coating-metal surface.
Hardness and appropriate levels of compliance combined increase the wear-resistance of a substrate. Again, PEO’s unique microstructure gives the material high fracture toughness, reducing the potential for cracking under force, which means ceramic surface coatings provide excellent performance in tribology applications.
Corrosion resistance
Corrosion resistance is improved by adding PEO coatings with chemically inert ceramic-like properties and thickening the oxide layers by adjusting the PEO process to provide the desired level of resistance. For optimal corrosion resistance performance, PEO works best as a pre-treatment for subsequent sealers, paints and other polymers. Figure 4 shows a polyester powder coat applied to a PEO layer on a magnesium alloy substrate.
The strong bond between the two layers enhances corrosion resistance capabilities, also forming scratch resistant qualities. The polyester coating effectively fills the pore architecture created during the formation of the PEO layer.
Generally, PEO is good for different types of bonding because its reticulated microstructure creates a physical ‘key’ and does not rely upon chemical compatibility between additional coats, unlike alternative coating mechanisms. An extensive study by Keronite demonstrates the performance of Duplex PEO coatings in slat-spray testing.
The same principle applies to adhesion of oil and other lubricants in sliding wear applications. Hydrophobic properties also increase corrosion resistance – see below.
Dielectric breakdown strength
Introducing insulating dielectric characteristics can be achieved by finely controlling the thickness of the PEO coating, which can be achieved by tailoring the deposition process. The light metal’s oxide layer can be thickened to achieve dielectric strengths of 59-79 kV/mm.
Thermal barrier coatings
A reduction in thermal conductivity can be achieved by adding silicates to the electrolyte bath, which generates a mullite-rich coating that acts as a Thermal barrier coating (TBC), protecting light metal components that are used in high temperature and high speed applications.
Photocatalytic surface coatings
Titanium dioxide is well known for its photocatalytic properties, with potential applications in water purification. Photocatalysis typically relies on UV lighting and experiments with PEO have found the incorporation of nanoparticles such as Ag into a PEO coating of a titanium substrate drastically expands the effective spectrum of light enabling photocatalysis.
Anti-microbial properties
‘Salting’ the PEO electrolyte with zinc and a sodium/tungsten oxide introduces anti-microbial properties, making light metal parts particularly suitable for medical, healthcare and dental applications.
Hydrophobic properties
Increasing the hydrophobic properties of the component’s surface can increase corrosion resistance by preventing liquid droplets and contaminants adhering to parts. Titanium alloy medical and dental implants benefit from improved osseointegration.
Environmental Friendliness
Coating and surface treatments using heavy metals such as nickel, cobalt and frequently chromium often involve high-hazard chemicals. Tough regulations control the use of these chemicals. Conventional anodising uses strong acids, raising safety issues in use, transportation and disposal.
PEO is an environmentally safe option. Electrolytic baths are typically low concentration, chemically benign, aqueous solutions. Process waste streams can typically be discharged directly to drain after pH adjustment, so operating licenses are easily obtained.
To learn more about the characteristics and performance of PEO, download our PEO datasheet for Al, Mg and Ti alloys, or get in touch with one of our materials scientists today.
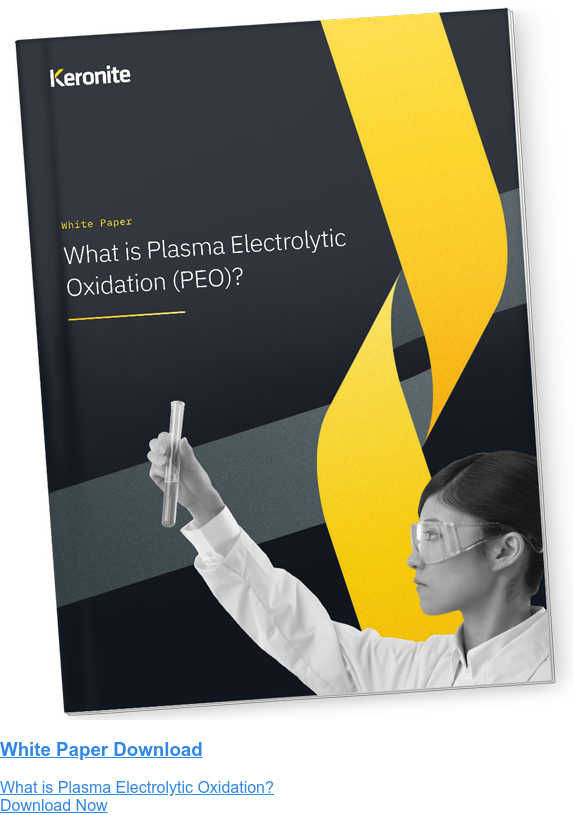
