What are the best alternatives to YSZ coatings for light alloys?
4 December 2020Engineering challenges such as emission reduction, improving performance, more demanding operating conditions and enhancing efficiency can only be met with high performance materials. This is particularly true in the sectors such as aerospace, automotive and energy, where greater power is required using lower weight components.
Extreme heat is a common feature in these operating environments, as jet engines and power generation turbines are more efficient, and therefore produce lower emissions, when operating at higher temperatures. Nickel alloys tend to be the metal of choice in these environments. However, engineers are increasingly turning to light metals and their alloys, such as aluminium, magnesium and titanium, to help meet some of these challenges.
Components like turbine blades, vanes, nozzles and exhaust manifolds must withstand high temperatures during operation, but the heat resistant properties of light metal alloys are relatively low. As a result, a thermal barrier coating (TBC) is usually required, even for heat resistance nickel alloys.
There are many TBCs available, including multiple surface coatings. A common solution to provide a heat resistant barrier for light alloys is to apply an Yttria-stabilised zirconia (YSZ) coating, usually by using a plasma spray or electron beam physical vapour deposition (EBPVD) technique.
What are YSZ coatings?
Zirconia, or Zirconium dioxide (ZrO2), is a ceramic that is the base for many materials engineering solutions due to its high thermal resistance, and other useful properties. However, it undergoes a phase change from monoclinic structure at room temperature to tetragonal at 1173oC and cubic at 2370oC. As a result, when cooling it cracks, as the change in structure results in a change in volume. This reduces its utility as a thermal barrier or refractory.
However, when small amounts of Yttrium oxide Y2O3 are introduced, Zirconia’s structure is stabilised, so it does not change phases during heating or cooling. The resulting material is known as Yttria-stabilised zirconia (YSZ) that has low thermal conductivity, with a high coefficient of thermal expansion and is also shock resistant. As a result, it is commonly used as a surface coating for materials with low thermal resistance to protect them from heat. Such as turbine blades in a gas turbine engine.
YSZ surface coatings are typically applied to the substrate by using plasma spraying and electron beam physical vapour deposition (EBPVD). The latter technique heats the YSZ into a vapour using an electron beam. The YSZ vapour condenses as a thin film onto the substate, or an additional barrier layer depending on the TBC required. Plasma spraying uses a plasma flame, typically an argon-nitrogen-hydrogen-helium mix, to melt YSZ powder that is sprayed via a spray gun onto the substrate.
How YSZ coatings’ thermal conductivity compares with PEO
Effective TBCs have very low thermal conductivity, measured as watts per metre-Kelvin, W/mK. Or put another way, TBCs have high thermal resistance and thermal insulance. This is expressed as a heat transfer coefficient, measured by WK-1m-2.
To put thermal conductivity into context [this link lists the thermal conductivity of many common materials], at room temperature, air is a poor conductor of heat / a good insulator, with a thermal conductivity of 0.0262 W/mK. Graphite is a good conductor of heat / poor insulator, at 168 W/mK. Aluminium is an excellent heat conductor / not an insulator, with thermal conductivity between 237 W/mK at -73K to 220 W/mK ay 527K.
The thermal conductivity of YSZ surface coatings can vary widely according to the method of application and the exact ratio of Y2O3 to ZrO2. In one instance, Zhao et al found that using EBPVD and with 6-8 wt % Y2O3, thermal conductivity was between 2.2 and 2.9 W/mK.
Plasma electrolytic oxide (PEO) coatings are regularly used as TBCs on light and valve metals and their alloys in a wide range of high-performance applications, including automotive and aerospace. According to the Composites and Coatings Group, part of the University of Cambridge’s Department of Materials Science & Metallurgy, for PEO: “typical thermal conductivities are of the order of 1 W/mK, providing good thermal insulation to the substrate material.”
A study by Apelfeld et al shows that thermal conductivity of a PEO coating on a zirconium niobium alloy (1% Nb) falls to 0.2 W/mK at temperatures of 1600K. The authors highlight that “the thermal conductivity of PEO coatings is several times less than one of [the] reference sample of [YSZ].”
Doping PEO electrolytes to increase heat resistance properties
Unlike the plasma spraying and EBPVD techniques used to apply YSZ coatings, PEO uses an electrolyte bath and plasma to form a ceramic-like duplex coating on the substrate. The bottom layer is well adhered to the substrate with low porosity, but a feature of the plasma discharges during the PEO process is that they cause the porosity of the outer layer.
The electrolyte bath can be ‘salted’ with other substances to take advantage of the porosity, and tailor the top layer according to the application. Curran et al found that using a silicate-rich electrolyte for the PEO process resulted in a mullite-rich PEO coating on aluminium alloys. This reduces the thermal conductivity of the PEO coating to 0.5 W/mK, alongside other valuable properties such as faster growth rates, greater thickness and low stiffness.
YSZ is the default heat resistant coating for many engineers when applying TBCs to components and parts in high temperature applications. However, it is clear that PEO offers a viable alternative, particularly given the ability to customise other characteristics, such as corrosion protection, lubrication and dielectric properties, by further salting the electrolyte bath. This flexibility is not possible using conventional YSZ TBCs and application techniques.
To learn more about PEO, download our white paper ‘What is Plasma Electrolytic Oxidation?’ or get in touch with one of our materials scientists today.
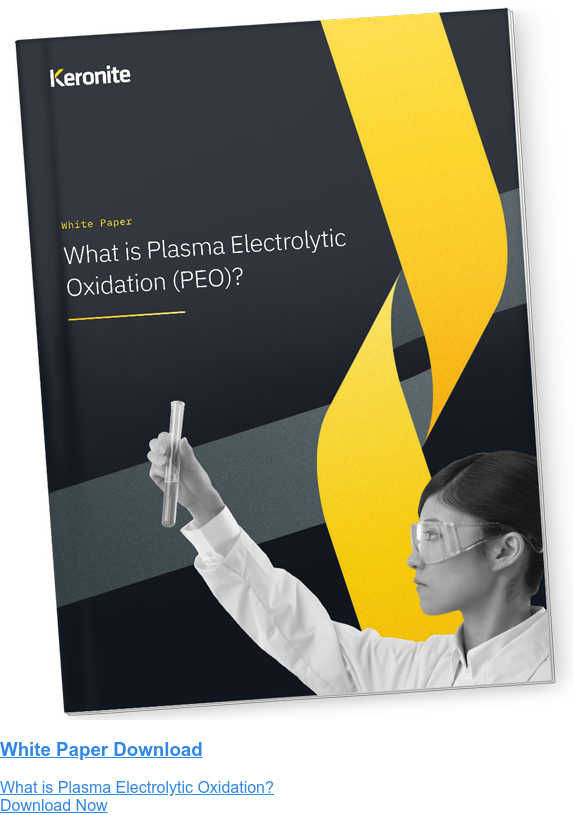
