Hydrophobic coatings for corrosion resistance and osseointegration
3 November 2020Light alloys, such as titanium, magnesium and aluminium, are used increasingly in high performance applications due their exceptional performance characteristics. Titanium is high strength, low weight and exceptionally corrosion resistant. Aluminium and magnesium have similar mechanical properties and are less expensive and easier to work. Each brings a unique set of qualities that, when used correctly, can bring a number of benefits to any given application.
As a result of these and other features, light metal alloys are widely used in demanding applications such as aerospace and defence, automotive, medical protheses, orthopaedic and dental implants and industrial processes. These testing applications require a unique combination of qualities in order to enhance the performance of the materials used.
But light alloys are not a panacea to all materials challenges. Aluminium and magnesium alloys are chemically active so react with surface contaminants and corrode. Titanium and its alloys can become susceptible to corrosion in high temperature conditions. They need further protection – which is where high performance surface coatings make things interesting.
Surface coatings can protect these materials, enabling their use under these testing conditions. And hydrophobic, low or non-wettable surface coatings allow light metal alloys to be used in very specific applications, where repelling liquids is an essential feature of the metal’s application. But the benefits of a hydrophobic coating stretch further than you might at first believe.
Wettability and hydrophobic behaviour
The wettability of a surface, measured by its contact angle from zero to 180 degrees, is a measure of whether a liquid drop will spread out on that surface, or avoid the surface by ‘balling up’. This is determined by the balance of adhesive and cohesive forces of the liquid and solid surface. A hydrophobic surface will cause the liquid to ball up.
Higher adhesive forces, created where the contact angle is low, result in the liquid spreading out and sticking to the surface, which is called hydrophilic. Greater cohesive forces, the forces that cause molecules to tightly bind, with low adhesive forces to the surface, cause the liquid to form a drop on that solid surface, which is therefore hydrophobic with a high contact angle.
So, if a materials engineer does not want liquids to spread out or adhere to a solid surface, they want that surface to have a high contact angle, which means low or non-wettability, and thus hydrophobic properties. Any liquid, from rainwater to corrosive acids and oils, will sit on top of the surface as a droplet.
Surfaces where the contact angle is zero or close to zero degrees are called superhydrophilic. Similarly, surfaces where the contact angle from approximately 150 degrees to 180 degrees is known as superhydrophobic. A superhydrophobic surface is therefore highly water repellent. For many applications, water repellency is a critical, but often understated, feature.
The role of hydrophobic surface coatings
Why would a materials engineer need to choose a hydrophobic surface? A good example is the leading edge of an aircraft wing, which can ice up during flight or on the ground. These leading edges are typically made from light structural alloys (typically high in aluminium content). Titanium alloys can be used when, for example, the leading edge is likely to be subjected to high temperatures, such as supersonic aircraft.
If the leading edge can be coated with a low wettability hydrophobic coating that repels water, the ice is less likely to adhere to the wing and therefore cannot build layers of ice that impact on the wing aerodynamics and potentially cause disaster, such as USAir Flight 405.
Steam and gas turbine blades are another example where hydrophobic surfaces play an important role. They operate in harsh conditions where high strength, low weight, stiffness, corrosion resistance and temperature resistance are essential. Liquid droplets can adhere to the turbine blades and nozzles, incorporating contaminants that form deposits.
These deposits can distort the blades and nozzles or corrode the surfaces, particularly of components made from light alloys that are susceptible to corrosion. The distortion and corrosion can in turn cause component failure, particularly if the steam purity is poor.
However, liquid droplets and corrosive deposits cannot adhere to turbine components with hydrophobic coatings, enabling the turbine to run smoothly, even if the steam or gas includes contaminants. This reduces both failure risk and downtime for maintenance, both of which can drastically increase the value of certain designs.
Hydrophobic coatings in osseointegration and biomaterials
In medical and dental implant technology, osseointegration is the process of directly fusing, or direct attachment, of the bone tissue to the implant. It is most often used in the context of titanium and calcium phosphate coated titanium implants and medical protheses, like a hip replacement device.
Under most circumstances, bone tissue, and specifically the osteoblast cells that promote bone growth, fuse more effectively to the light metal alloy implant if the metal surface is roughened. Hydrophilic surfaces facilitate the process, encouraging cell adhesion and greater integration of the osteoblast cells.
Implants with hydrophobic surfaces reduce or prevent integration of bone and implant, because of the way that cells adhere to surfaces. However, although a hydrophobic surface reduces osteoblast proliferation, it encourages osteoblasts to differentiate into osteocytes. These stellate cells are a fundamental, and the largest, component of bone tissue, so encouraging their growth is a positive step.
Although a developing area of research, studies suggest that implants with a roughened superhydrophilic surface that has an overlay of a superhydrophobic surface may be the optimal combination to promote osseointegration. Studies such as these are highlighting that the composition of surface coatings could further still become optimised for cell proliferation and adhesion.
Surface coatings that can be tailored to show hydrophobic features
As demonstrated above, there are multiple applications where hydrophobic or superhydrophobic behaviour of the light alloy surface is required. However, untreated metal surfaces and most conventional surface treatments do not produce the required contact angle, and therefore the required superhydrophobic performance for many modern applications.
However, materials engineers choosing the surface coating technology plasma electrolytic oxidation (PEO) can introduce the required superhydrophobic performance. PEO uses an electrolyte bath and plasma to form a ceramic-like coating on light alloys. There are two specific features of PEO enabling engineers to introduce superhydrophobic behaviour. Firstly, the coating is multi-layered, and the top layer is porous, meaning that additives that change the behaviour of the coating can be introduced.
Secondly, the composition of the electrolyte bath can be altered so that materials engineers can finely control the additives in the porous top layer. Research shows that adding potassium stearate to the PEO electrolyte increases the contact angle to 130 degrees. This results in the superhydrophobic behaviour required. Similar benefits can be generated when using fatty acids as the additive.
The combination of anti-corrosion and osteoblast cell differentiation that result from the superhydrophobic PEO coating is particularly relevant to biomedical applications, in addition to the wider aerospace and industrial uses.
To learn more about PEO, download our white paper ‘What is Plasma Electrolytic Oxidation?’ or get in touch with one of our materials scientists today.
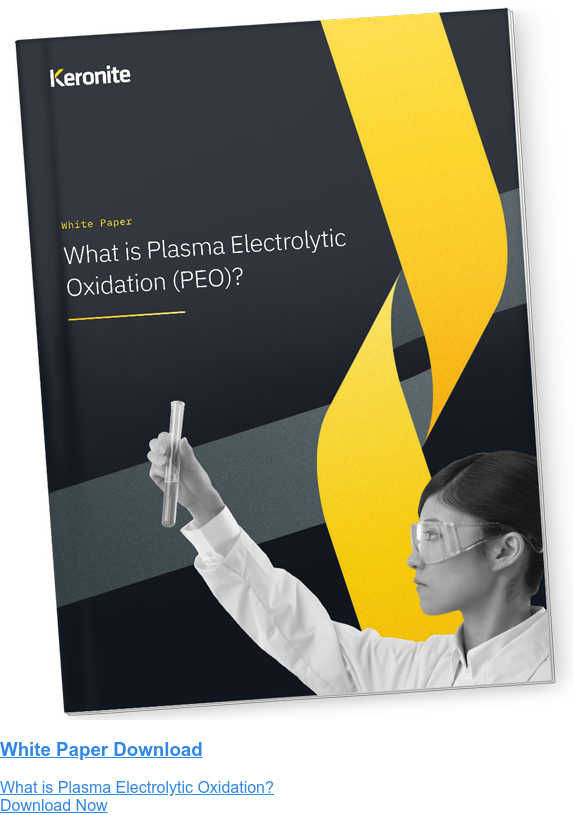
