4 wear resistant coatings for lightweight metal
24 January 2024Lightweight metals have become integral to automotive, aerospace, transportation and many other industries. Offering the possibility of weight reduction and cost-efficient performance, they can contribute to the increased efficiency, performance and sustainable manufacture in these industries.
Despite their favourable strength-to-weight ratios, lightweight metals tend to have low hardness and exhibit poor resistance to mechanical wear. Aluminium, for instance, is susceptible to friction-initiated wear, making surface engineering and advanced coatings essential for use in many applications.
The wide variety of applications and consequent demand for these lightweight metals has spawned a wide range of surface solutions. These solutions vary in strength, application technique, thickness and chemical composition. Reviewing the differences between these methods is a key step in your search for the optimum coating for your application.
Requirements for a wear resistant coating
Firstly it is important to recognize that “wear resistance” is an umbrella term and there are different types of wear such as impact, fretting, abrasion, friction sliding and others.
Traditionally, it was believed that high hardness (H) of a material surface will give good wear resistance. This is true in part but does not take into account the different types of wear mechanism. In fact, a level of compliance is also very useful to allow deformation of the substrate without fracturing. A more useful indicator as to whether a coating will be hard-wearing is the ratio of its hardness or tensile strength to its stiffness (Young’s Modulus, E). Coatings with a high H/E ratio exhibit fracture toughness and can better tolerate substrate deformations without yielding. These properties confer wear resistance to the substrate more reliably than hardness alone. Examples of H/E ratio are illustrated in the table below:
Material | Tensile Strength/MPa | Young Modulus/MPa | H/E |
Aluminium alloy 6082-T6 | 300 | 70,000 | ~4x10-3 |
Borosilicate glass | 70 | 50,000-90,000 | ~1x10-3 |
Butyl rubber | 13 | 7 | ~2 |
A second important property for a wear resistant coating is low friction between the coating and its wearing counterpart. Friction is a somewhat complex phenomenon microscopically, summarized by the well-known macroscopic formula F = µN. Reducing the friction coefficient, µ, reduces energy transfer between sliding surfaces and hence reduces the potential for damage. This can be achieved to some extent by polishing the surface to lower roughness. Alternatively, introducing a lubricating layer, less able to sustain a shear force, between the surfaces will reduce energy transfer and thus damage. Such layers could be gases, liquids or even some solids, such as graphite or MoS2, possessing lamellar structures with weakly-coupled layers that can easily decouple under shear forces. This approach of friction reduction works in cases where low friction is a requirement e.g bearing surfaces but is less useful for e.g braking surfaces where energy transfer between the surfaces is the primary requirement.
Finally, in cases involving high normal loads (N) between the two surfaces, the coating may need to have load-bearing capabilities, particularly if it has higher strength than the substrate. This is often the case with lightweight metal substrates, whose relatively low yield strength may not otherwise support the Hertzian stresses provided by the wear partner. In this case, two approaches are to apply a very thick coating that may be able to sustain the loading without yield or fracture, or to increase the strength of the base metal surface itself by diffusion of secondary elements into its lattice.
We’ve examined four of the most popular surface coatings for achieving wear resistance, to help kick-off your search:
1. Hard anodizing
Hard anodized surface coats are produced in a similar process to standard sulphuric anodising techniques. Higher temperatures and different processing time parameters are used to form harder and thicker protective oxide layers.
Hard anodizing provides a very good wear resistant coating for many applications. It has hardness two or three times higher than the aluminium itself but considerably lower than most common abradants such as sand, glass, textiles etc. Its main defence is a fine columnar microstructure which can result in a very smooth surface once polished and consequently low friction.
Hard anodized coatings are best suited to applications involving intensive heat, but not necessarily those involving heavy normal loads. Metals intended to carry heavy loads should not be hard anodized, as the coating typically has through-thickness vertical cracks that act as stress raisers and reduce the fatigue strength of the metal. The limited aesthetic effects also limit the applications for hard anodized metals, making them a less flexible option for product engineers. Hard anodizing is not available for magnesium and titanium alloys.
2. Nitriding
Nitriding is a popular hardening heat treatment. The protective layer is hard, slender in form and is grown by thermochemically introducing nitrogen to the outer surface.
Although titanium is naturally strong, the wear rate is high when compared to other lightweight metals. Protective layers can vastly increase the abrasive wear protection in strenuous environments and applications. There are three widely used methods to nitride a metal surface:
- Salt baths - less common, due to the toxic byproducts
- Gas nitriding - still popular, although ammonia is produced which poses difficulties when produced at high volumes
- Ion nitriding - a particular innovation focus, a cleaner nitriding method using plasma under vacuum conditions
Each of these methods has production face unique challenges. For example, gas nitriding methods are less suitable for materials with more complex geometry unless high-pressure application is used. However, one challenge of all nitriding methods is the high temperatures (typically above 540ºC) meaning that, in the context of light alloys, it is only really suitable for use on titanium. Even then, the possibility of thermal distortion must be considered.
The most suitable uses for nitriding techniques are for materials produced at low volumes. There are also issues with materials of complex geometry, as sufficient pressure is required to form the slender layers, so for more scalable coatings, simple materials are recommended.
3. Plasma Electrolytic Oxidation (PEO)
Aluminium, titanium and magnesium can all be enhanced with a PEO (plasma electrolytic oxidation) coating. This is partly due to the flexibility in the 3-stage formation process, as follows:
- In a process not dissimilar to anodising, the metal substrate is submerged in an alkaline electrolyte bath composition and a voltage is applied which oxidises the surface
- Plasma discharges are formed across the coating, modifying it both physically and chemically
- Elements from the electrolyte solution can be combined into the coating alongside the oxides of the substrate
Due to the plasma discharges, crystallites of high hardness can be formed in the coating. Furthermore, the nano and micro-structured films so formed can be tailored to give an attractive combination of high hardness and low stiffness required for high fracture toughness, high adhesion and hence wear resistance. Typical values of Hardness ~15GPa and Young’s Modulus ~20-30GPa give a favourable H/E ratio of ~0.5, a similar order of magnitude to that of rubber and two orders of magnitude higher than aluminium 6082. To visualize the properties of such a coating, a useful analogy is a cobbled street which combines hard “particles” connected by a more compliant matrix of lime or other mortar. Such streets dating back to Roman times can still be found in service in Europe. Similarly, seashells are formed of nacre, the celebrated natural nano-composite that comprises small interleaved platelets of calcium carbonate. The platelets are typically of sub-critical dimensions for crack propagation and the resulting structure has a high toughness that gives seashells an afterlife long after the parent mollusc has died.
Notably, however, it is the green credentials of the comprehensive coating that are encouraging focus on this technique from regulatory bodies. Coatings produced by PEO are free from toxic byproducts and are free from chromium, which mean REACH and RoHS compliance can be attained through the techniques.
Comprehensive wear and corrosion resistance can be achieved through a PEO coating - without the need for an additional seal. However, the natural roughness of the coating means that a post treatment to reduce roughness or friction are often required. Nonetheless, the combination of excellent wear and corrosion resistance, combined with a clean application process, ranks PEO amongst the most promising of scalable surface treatments to emerge in the last 30 years. However, it is important to consult a surface engineer familiar with PEO to achieve the best results.
Learn more about Keronite's revolutionary plasma electrolytic oxidation technique in 'What is Plasma Electrolytic Oxidation?'.
4. Electroless Nickel
Electroless nickel (EN) plating is perhaps the most popular and effective type of chemical or autocatalytic plating on aluminium and titanium. It involves deposition of a Ni-P composite in a chemical bath, producing coatings of excellent uniformity and throwing power. These coatings possess high hardness, natural lubricity, ductility and good wear and abrasion resistance, making them a very good coating in sliding wear applications. Additional wear resistance can be conferred by inclusion of silicon carbide into the coating (so-called Nicasil coating).
Good quality EN can be problematic to apply since the cleanliness of the surface prior to application is critical, and any surface contaminants may fail to initiate plating in localized areas. The principal disadvantage of EN on light alloys is that it is a cathodic, or non-sacrificial, coating and will cause rapid corrosion of the substrate if the coating contains any pores or other breaches. This was a common cause of failure on cast alloys, causing it to be abandoned as a widespread coating for cylinder liners in internal combustion engines. This property means that EN is rarely applied to magnesium, expect with a passive interlayer such as a PEO coating.
More recently, EN plating has become a more highly regulated industry due to health and environmental concerns associated with nickel compounds. Also it is difficult to recycle EN plated components since the coating must be stripped beforehand.
Conclusion
In high temperatures and at tight tolerance environments, preventing wear in tribological applications - like engines - is absolutely essential. Even in less severe conditions, the choice of a surface coating is an important one, needing your care and attention in matching desired performance with an appropriate method.
Taking a holistic approach to this decision will best serve you in finding the optimum solution. This entails reviewing the composition of your lightweight metal substrate and that of the counterpart or agent causing the wear. Application-specific performance requirements, component geometry and an understanding of the nature of the wear mechanism itself will help to ensure the correct approach can be selected.
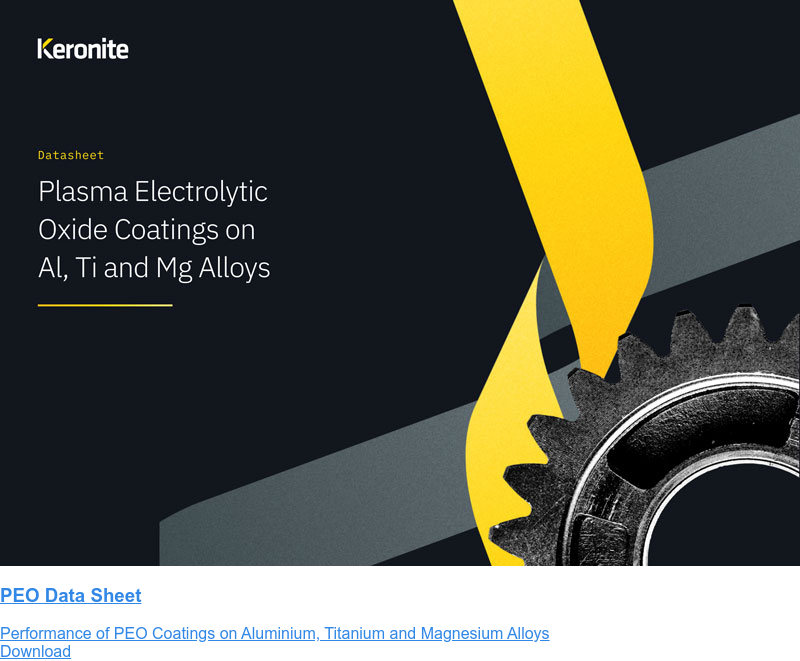
