Radical surfaces: new developments in material science
14 December 2017The cutting edge of scientific research can take a while to filter into university courses and change received wisdom. As a result, engineers and designers can be blissfully unaware of how the latest developments in surface technologies could radically improve the efficiency of their components. Here we’ll have a look at how Keronite overwrites the rules imposed by metals’ internal structures, offering exciting engineering possibilities in the process: stronger, more resilient, lighter, and greener alternatives.
Thinking outside what's inside
Experimentation, innovation, and disasters have taught us the properties of metals, making it seem like their internal structure defines what they are able to withstand, and what they are not – as if materials science is an open and closed book. Nobody wants to use a metal with a structure known as too weak to support a bridge, or prone to creep for aerospace: the metals available for the component at hand can seem like a fixed matter.
What this story overlooks is how the latest research into surface technologies has radically redefined the limits metals’ internal structures place on their properties. If engineers are aware of how surface technologies can radically change the properties of metals, all sorts of components could be rethought:
- with some awareness of how magnesium can be rendered strong and resistant by a surface coating, a car could be rethought to allow for a lightweight magnesium chassis.
- knowing that surface technologies can render otherwise hazardous metals inert means medical suppliers can manufacture cheaper, safer, and lighter instruments.
This kind of radical thinking can be applied to all sorts of products once the possibilities opened up by new surface technologies have been embraced.
Keronite rewrites the rules
To traditional material scientists, the properties of aluminium, magnesium, and titanium can seem set in stone:
- Magnesium is cheap and extremely light but chemically highly active.
- Aluminium is cheap and light but not particularly wear resistant.
- Titanium is light, strong, and extremely resistant, but relatively expensive.
With Keronite’s PEO coating technology, things change:
- Magnesium remains cheap, extremely light but gains further strength, and corrosion-resistant capabilities
- Aluminium remains light, but gains strength and wear resistance capabilities.
- Titanium develops a smooth, inert surface that stops it from galling nearby sliding parts and accelerating the corrosion of adjoining materials: ideal for harsh aquamarine environments and moving components.
With magnesium and aluminium suddenly viable and cheap alternatives to titanium, and titanium no longer a threat to surrounding parts, it becomes easy to see how designs and projects can be rethought: but how do these material changes take place?
PEO changes the surface of things
Keronite uses plasma electrolytic oxidation (PEO) to form a ceramic coating from the substrate of the metal. PEO is similar to anodisation, as the metal is submerged in an electrolytic bath and an electric current is passed through. Unlike anodisation, PEO uses absolutely no toxic agents, and the electrical current employed is much higher. The high current causes plasma discharges at the surface of the metal.
The resultant ceramic coating is highly adhesive, almost a part of the metal. It is super strong, lightweight, and able to withstand great degrees of strain without warping. As it is chemically inert, the resulting component can be used in flammable or organic environments, making it useful in everything from helicopter engines to ship hulls.
Plasma and precision
The introduction of plasma into the anodisation process fundamentally alters the microstructure of the metal’s surface. The oxide layer of the metal crystallises, preventing the kind of cracks that can result from anodisation. A range of elements can be incorporated into the coating from the electrolyte, providing a range of aesthetic and material properties: the porosity of the coating, its hardness, and its colour can all be controlled.
Different porosities of the coating allow for different surface finishes, such as lubricants, to graft on, depending on what is required of the component being coated. Every aspect of the process, from the electrolyte, to the intensity and duration of the current, is precisely controlled to ensure that the resultant Keronite coating is fit for the exact purpose in question. Keronite’s scientists perform extensive tests with various parameters and alloys, to ensure that the resultant coating’s properties are predictable and optimised.
Rethinking engineering from the top down
With Keronite’s PEO technology, metals such as magnesium and aluminium, that had been deemed unsuitable in many industrial uses, have become cheap options that provide similar structural benefits to titanium. The advantages for engineers and component designers are clear: instead of ruling out cheaper lightweight metals as structurally unsound, Keronite means that whole projects can be based around small, lightweight, and highly resistant components.
One industry that have used Keronite’s material innovations to rethink how they operate is aerospace manufacturers. Keronite were specifically approached to see if their PEO technique could be used to redesign existing components, reducing the need to keep planes out of action for regular repairs. Keronite created a high-wear and lubricant duplex surface coating that was proven to be able to withstand extensive wear at high altitudes for long periods of time. . With this, there was much less of a need for planes to be taken out of action for repairs, and parts could be manufactured at a lower cost: the airlines’ whole operational model was changed thanks to research into surface technologies.
Bike and consumer electronics manufacturers have also used Keronite to reevaluate their use of materials, saving time and money in the process: get in touch to find out how Keronite's technical expertise can add to the performance of your components.
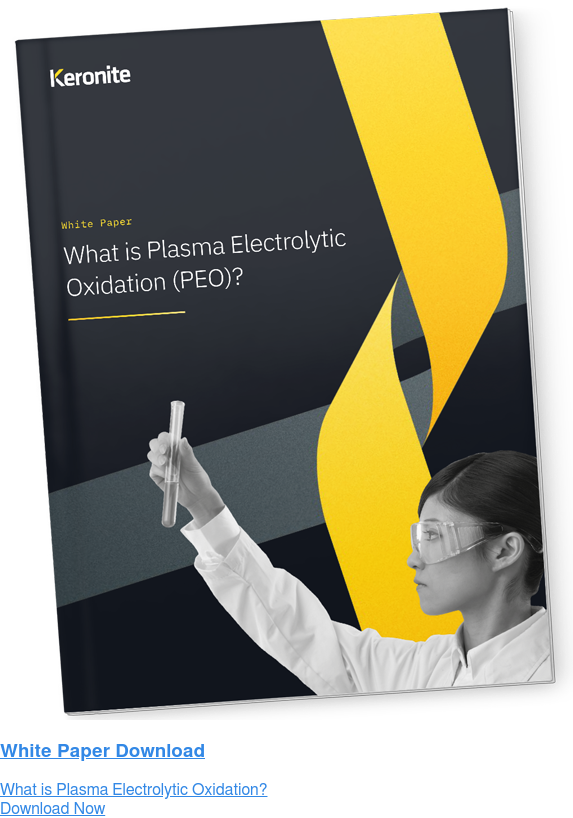
