Selecting the right lightweight metal
13 November 2023Many industries are looking for innovative ways to reduce their costs, lower the weight of their products, and reduce their overall energy consumption. As a result, lightweight metals, such as aluminium, magnesium, and titanium are being increasingly considered to replace steel components.
With new research into alloys and surface technologies like PEO, engineers are able to use these lightweight metals in ways that would previously have been considered inappropriate. To find the right material solutions, it is important to have a sense of the potential advantages and drawbacks of each metal, and how they might impact on the project at hand.
Advantages of aluminium
Aluminium has long been used as an alternative to stainless steel, given its properties are highly favourable for a number of industrial applications. First and foremost, it is cheaper than steel to cast and fabricate, and the cheapest of the metals we’re looking at pound for pound.
Aluminium has a passive oxide layer which provides innate corrosion resistance, which can be further improved through alloying and surface coating. It is about a third of the density of steel, giving it a useful strength-to-weight ratio. This can easily be further improved through alloys and coating techniques.
Aluminium also has high ductility and malleability. As a result it can be precision machined with ease, saving time in the process of fabrication, making it a greener and more economic option.
Disadvantages of aluminium
Despite its advantages, it is worth keeping in mind that there are a number of drawbacks to using aluminium for certain applications.
Its low hardness tends to mean it has poor abrasion and wear resistance. Hence, hard wearing coatings are required in many circumstances to enable its use where it otherwise provides suitable mechanical properties.
While aluminium does have a fairly low tensile strength, there are alloys that can raise it from 70 MPa to around 700 MPa, providing a very high strength-to-weight ratio. However, it should be noted that the price for such high strength tends to be a significant loss of corrosion resistance. Coatings are normally essential to prevent corrosion where high-strength alloys such as 7xxx and 2xxx series are employed.
Although it is widely used in food packaging and cooking utensils, there is some concern about aluminium’s biocompatibility and potential links to Alzheimer’s disease. Again, protective coatings can provide the answer in many cases, helping to ensure no reaction of the substrate occurs.
Industrial uses of aluminium
From aircraft fuselage to coke cans, aluminium, with its low weight, low cost, and ease of fabrication lends itself to a myriad of engineering applications:
- Apple have led the way in the widespread use of aluminium to make the distinctive bodies of their MacBooks, iPhones, and iPads. Steve Jobs’ enthusiasm for the metal even led him to order a custom aluminium yacht. Since Apple’s pioneering use of aluminium, it is now the choice material for laptops and phones.
- Many cars have a lightweight aluminium hood and other body panels. Typically, major engine components such as engine blocks and pistons are now almost exclusively made from cast aluminium alloys. Other lightweight aluminium components such as brake callipers, electrical housings, interior trim parts all help to reduce vehicle weight and increase fuel efficiency.
Advantages of magnesium alloys and coating
A surge in interest over the past decade has revealed how magnesium alloys and coating techniques can make the most of the metal’s attractive properties.
Magnesium is extremely light: it has a density of 1.74 g/cc and is 75% lighter than steel, 50% lighter than titanium, and 33% lighter than aluminium, offering serious opportunities for efficiency savings in applications using it.
It has the highest known damping capacity of any structural metal, capable of withstanding 10x more than aluminium, titanium, or steel thanks to its high mobility dislocations. It is also very easy to machine, and can be injection moulded. Additionally, magnesium is entirely biocompatible, posing no toxicity hazards – offering an immediate advantage over aluminium.
Disadvantages of magnesium alloys and coating
However, magnesium has some well known shortcomings that limit its wider applicability in industry.
For one, it is highly chemically active, meaning chemical and corrosion resistance tends to be low. Its low surface hardness, like that of aluminium, makes it difficult to use in tribological applications without a coating.
Potential concerns about flammability also often rule out the use of magnesium, but only in extreme thermal conditions rather than most industrial applications. Nonetheless, this aspect should still be considered as part of a holistic material selection process.
Making magnesium fit for industrial applications
Since the 1998 ACEA agreement, legislation limiting carbon emissions has led the automotive industry to investigate ways in which the extremely light weight of magnesium can be made fit for purpose. Prior to this surge in interest, magnesium had seemed unusable in many industrial contexts. However, recently discovered alloys have provided the surface characteristics for the metal’s successful integration into automotive designs.
Higher-purity variants of traditional alloys have resulted in a significant resistance to corrosion, and new coating techniques such as plasma electrolytic oxidation (PEO) make a thoroughly resistant neutral oxide from the metal’s substrate. Magnesium’s poor creep resistance also traditionally made it unsuitable for high temperatures, but recently discovered alloys such as ZE41 & ZWO8203 are heat resistant at extreme temperatures (c. 400 F).
Additionally, advanced surface coating technology like PEO can greatly enhance thermal and corrosion resistance, as well as providing a range of additional surface features to extend the life of magnesium alloy components.
As a result of these developments, magnesium is increasingly being used in a range of settings:
- Car seats, power tools, luggage, and cameras have all been designed to make the most of lightweight, strong magnesium.
- Military engineers have begun using magnesium in helicopter gearboxes and generator housings, as a means of providing lightweight resistance to extreme temperatures.
- High-performance mountain bike frames and wheels are increasingly made of lightweight, corrosion-resistant magnesium.
- The aviation and automotive industries are increasingly looking at ways magnesium can increase fuel efficiency and reduce greenhouse gases.
- Complex, light, and strong components such as those found in engines can easily be moulded out of magnesium.
Exciting developments in magnesium alloys, manufacturing methods and coating technologies are making magnesium an increasingly viable candidate for a strong, lightweight, and cost-effective solution.
Advantages of titanium
Titanium is significantly stronger (220 MPa) than both aluminium and magnesium, although its higher density means that strength-to-weight ratios for the three metals tend to be similar. It is often the first port of call for engineers looking to replace steel in a lightweighting exercise for stressed components.
Titanium has the additional advantages of being highly corrosion-resistant and having an innate resistance to extreme thermal environments, reaching highs of approximately 550°C before mechanical performance deteriorates. Both these features are present without the use of alloying, and can be enhanced further when alloys are introduced.
Disadvantages of titanium
Titanium plates and components often run into the complication of cracking. They are sensitive to fatigue, especially in the cases of the notch sensitivity effect; areas of geometric discontinuity have a detrimental effect on the fatigue strength of the metal, causing it to crack.
Titanium also has a high cost of extraction and fabrication, which may rule out its use for the general consumer market and a number of industries.
Industrial applications of titanium
In industry, titanium can be found:- On ship hulls, submarines, and other structures exposed to seawater, due to its high corrosion-resistance
- In hip replacements and dental implants, due to its high biocompatibility and strength.
- In aircraft, spacecraft, and missiles.
If money is no issue, titanium is an excellent choice for a strong, lightweight material. This is only enhanced with the use of advanced surface coating like PEO that can eliminate its susceptibility to cracking and enhance its already prominent features..
Integrate lightweight metals seamlessly into your designs with PEO
Aluminium, magnesium and titanium each showcase unique properties that can bring certain optimisations to specific designs. But one thing they all have in common is the ability to reduce the weight of designs, which is a design challenge that permeates through almost every sector of engineering.
Like their benefits, each of these metals showcases certain weaknesses to different environmental and mechanical elements. As a solution, PEO’s advanced electrolyte bath process provides a protective outer ceramic layer that provides a number of customisable surface characteristics; hardness, corrosion resistance, thermal protection, dielectric strength, enhanced adhesion and many more.
To find out more about the PEO process and how it can enhance the properties of aluminium, magnesium and titanium for your design, send an enquiry today.
FAQ
Which metal is best for high thermal applications?
Titanium is the best of the three metals for high thermal applications. That said, certain magnesium and aluminium alloys can greatly enhance thermal performance. When paired with PEO, these metals can also exhibit mechanical performance in extreme temperatures.
How sustainable is each metal?
All three metals can be 100% recycled naturally, however certain coating solutions such as chromate conversion processes prevent their recyclability and can produce harmful byproducts. PEO is free of organic compounds, COV or strong acids and enables full recyclability of components.
What is the application of magnesium alloy in aerospace?
With thorough coating solutions such as PEO, magnesium can be used in a variety of structural and internal components in aerospace applications to optimise weight and enhance fuel efficiency. Keronite’s PEO technology was chosen as the coating technology for NIRSpec after extensive mechanical and thermal testing
How effective is each metal for structural applications?
Each metal can be integrated into structural components with varying degrees of success, with magnesium having the lowest tensile strength and titanium exhibiting the highest. With PEO, the structural capabilities of each metal can be enhanced to be successfully integrated into a number of structural components.
What is magnesium alloy used for/what are magnesium alloy applications?
Various magnesium alloys provide specific characteristics; high-pressure die casting provides extreme thermal resistance, ultrastrong alloys provide extreme tensile strength, and high-heat conductivity alloys enable heat dissipation and management characteristics. This enables the use of magnesium in structural components, those within and close to engines and in heat management/dissipation systems. PEO enhances the characteristics of each alloy, greatly extending the life of these components.
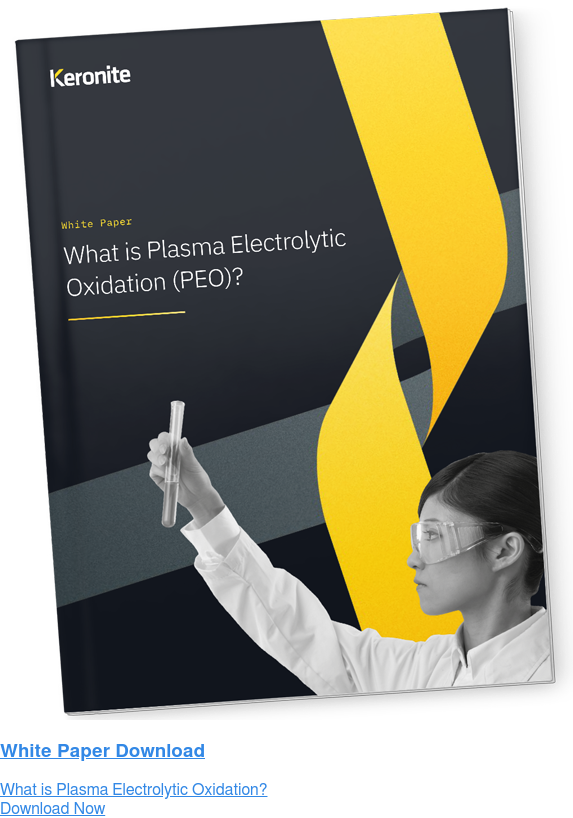
