Protecting magnesium components from corrosion and wear
25 February 2019Every industry can enjoy the benefits lighter materials bring. Automotive manufacturers are using aluminium and titanium to improve the specs on their latest sports cars. Space companies are finding ways to deploy light alloys in their satellites, to keep them in orbit for longer. Consumer electronics manufacturers are even using light alloys to make their products lighter and to give them a premium feel.
Magnesium is yet to reach its full potential within these industries. This is understandable, given its reputation as a reactive, wear-prone and vulnerable-to-corrosion material. Only now are materials scientists beginning to realise its potential. So, how can a material with limited wear, corrosion and thermal characteristics become fit-for-use within the toughest applications for metals in the world?
Promising properties, enhanced
With a density of 1.7g/cm3 making it the lightest structural metal available to engineers. This fact alone has given magnesium a certain aura, with engineers continually looking at ways to tap into its unfulfilled potential. Not only is Mg incredibly lightweight, but it naturally provides good levels of stiffness due to its hexagonal, close-packed, crystal structure.
The benefits are not purely due to its lightness, though. Magnesium is the 8th most abundant element on the planet and it’s easy to machine and cast. So it’s not only light on the load, but it’s also light on the pocket. Magnesium is widely recyclable, too, so it’s helpful for enhancing post-life green credentials.
Further benefits include its biocompatibility and thermal conductivity properties.
Modifying magnesium
Despite having an attractive array of benefits, magnesium is best known for its biggest drawback: it’s highly reactive characteristics. This limits its usage in wear and corrosion-concerned industries. To enable its use, materials scientists over the last decade have conducted in-depth research projects to find ways to deliver its benefits to engineers.
So, what surface coatings are capable of enhancing magnesium so it can be used in tough, high-performance applications?
Cold spray technologies
Thermal spray techniques traditionally involve propelling heated material (usually in a molten state) towards the substrate. This instigates a rapid process of oxidation, which can present residual stresses to a substrate.
However, cold spraying is a different technique that seeks to disrupt the natural oxide layer formed on the surface of magnesium. Rather than propelling particles at a high temperature, cold spraying uses compressed gases, allowing the coating to be deployed at the lowest popular temperature.
Cold spray technologies:
- Deliver highly, dense local galvanic corrosion protection for magnesium alloys
- Are relatively inexpensive, but can be costly to process in high volume production plants
- Can be modified based on the gas type, particle type, nozzle design and standoff distances to achieve different coating characteristics
Electroless-Ni-plating
Electroless nickel plating (ENP) is another option often considered for improving the corrosion resistance of magnesium alloys, where the coatings performance in marine environments has a great reputation.
The process involves submerging components in a plating bath with predetermined chemistry and composition. However, the coating typically requires specific preplating requirements, such as surface preparation and cleaning, which can add to manufacturing complexity and cost – making it a less than optimal choice for high volume production components.
ENP delivers:
- Great marine corrosion protection qualities
- Moderate-to-good levels of hardness and wear protection
- Relatively high substrate adhesion
- Customisable coatings depending on the surface preparation, cleaning and plating bath parameters
Plasma electrolytic oxidation
Plasma electrolytic oxidation (PEO) is a bath-based conversion coating which creates a scratch and corrosion-resistant ceramic coating on magnesium alloys. Using the same fundamental techniques as used in anodising, parts are immersed in an electrolytic bath, whereby a voltage is applied and the metal oxidises. However, unlike conventional anodising, the use of plasma modifies the surface structure to create an ultra-hard, incredibly adhesive layer which can be transformed to create a variety of surface characteristics, based on the application at hand.
In a study conducted by Ford, the automotive manufacturer, plasma electrolytic oxidation was the only surface coating method which provided superior corrosion protection when compared to conventional chrome-based conversion techniques.
PEO:
- Enables the corrosion protection of magnesium without the use of outlawed chrome or any restricted metals
- Provides minimal fatigue debit, with less than 5% reduction in the endurance limit of some magnesium alloys
- Features incredibly high wear protection
- Acts as an ideal ‘key’ for any subsequent coats used in duplex coating systems
- Is entirely green as the process does not employ any restricted or hazardous substances
Magnesium for the future
The potential of magnesium is beginning to be understood and put into use within a variety of high-intensity industries. The material now features within many vehicles, aircraft and satellites. Keronite has been working with leading manufacturers within each of these sectors to create uncompromising coatings through plasma electrolytic oxidation, enabling these industries to minimise weight and extend the life of their components.
For more information about PEO, download the white paper ‘What is PEO?’ or get in touch with our technical team to get more detail about how plasma electrolytic oxidation could be used within your project. Keronite provides full testing facilities and can develop bespoke PEO variants to overcome the surface challenges faced within your industry.
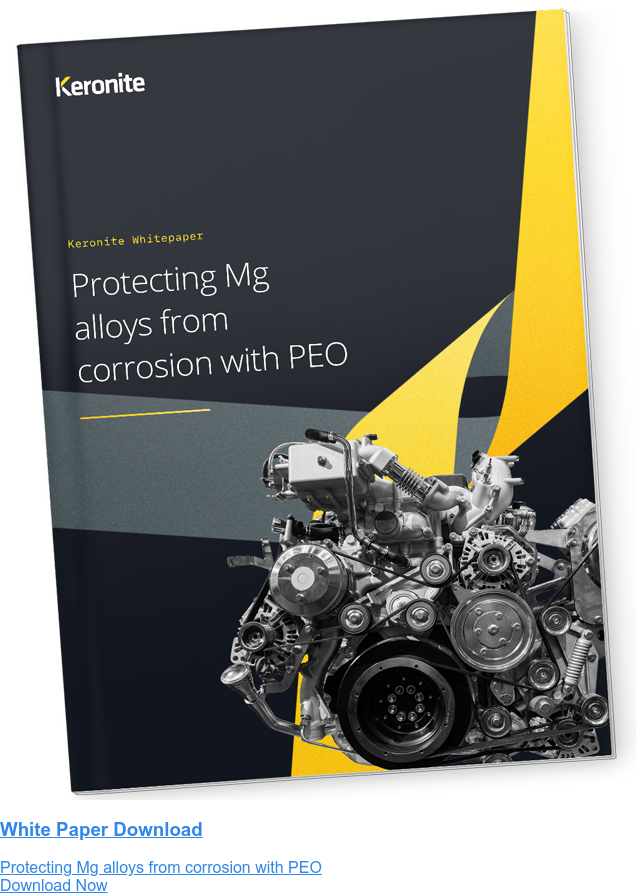
