What you need to know about Titanium surface treatments
17 April 2019Found in a variety of products, from hi-tech planes to golf clubs, the lightweight metal Titanium (Ti) is a hard-working material that can be strengthened with performance-enhancing surface treatments.
Ti alloys naturally offer an exceptional strength-to-weight ratio, great mechanical properties, corrosion resistance, and are known for their excellent biocompatibility.
It is an incredibly useful material, fundamental to a lot of components working in high-temperature environments. Titanium’s most distinctive advantage is the ability to retain strength at high service temperatures.
Picking the right surface treatment can be a struggle - thanks to all the considered variables and excellent choices available. Read on to learn the best and most popular surface treatments, and how they compare with each other.
Where is it used?
The aerospace, electronic device, defence, and medical trades all use titanium extensively, with 80% of all titanium alloys being produced commercially for the aerospace and defence industries.
Titanium-based materials also attract a lot of use as implantable materials. Their exceptional corrosion resistance has led to titanium alloys for medical implants, with Ti alloys being a staple of the dental industry since as far back as 1965.
In the future, it will continue playing a bigger role in electrical vehicles to prevent overheating between various parts; and also in seawater environments, where the protective oxide film is key in resisting aqueous corrosion.
Why are Engineers Using Titanium?
Titanium alloys are generally favoured for their moderate weight, high structural properties (e.g. strength, fatigue, toughness, stiffness), corrosion resistance (compared to steel) and an unusual ability to retain their mechanical properties at a high temperature (melting point at 1678ºc). If you are seeking a metal that is able to withstand heat, titanium alloys are the advised option, as they provide good creep resistance over a significant range of temperatures.
The titanium alloy Ti-6Al-4V, first introduced in WWII for aviation, continues to serve aerospace in numerous ways and has become an industry standard. Commercially pure titanium (CPTi, ASTM F67) is nearly 98-99.6% pure and is especially found in dental and medical applications. It is worth understanding which alloy will be picked for the component or design.
CPTi has higher corrosion resistance and is more ductile than Ti-6Al-4V. However, the latter has superior mechanical and structural properties. Either choice makes the best use of titanium’s advantages in a variety of applications.
What to be aware of before picking a treatment
From a financial perspective, titanium alloys have a high cost of extraction, and are more expensive to shape and form. Ti materials also require a treatment that can both enhance the lifespan and enhance other desired properties.
Cracking is a notorious issue with Ti. While formidable, titanium plates are sensitive to fatigue (in particular notch sensitivity). Fatigue reduces strength and consequently leads the material to crack throughout the component. Only advanced surface treatments can prevent this from happening.
One of the comparative disadvantages to titanium is perhaps its softness when observed alongside heavier metals like stainless steel or cobalt, and the higher rate of failure due to wear and friction performance. For example, Co-Cr-Mo (cobalt-chromium, otherwise used for biomedical applications) is 15% stronger than the Ti-6Al-4V alloy.
How to select the right surface treatment
Depending on the application, and required coating characteristics, surface treatments that address cracking and the high coefficient of friction, galling, and corrosion/oxidation, are recommended. Ideally, the treatment will enhance titanium’s life-span and improve the product’s performance in situ. Picking the correct treatment depends on the mandatories for the product design.
Plasma Nitriding
Plasma/ion nitriding (PN) enhances the friction, wear, fatigue and corrosion properties for components with the support of plasma. It is a hardening-heat treatment that thermochemically introduces nitrogen to the outer-surface (see figure 1) and forms a case (see figure 2). PN processes have been applied to many car components, like crankshafts, gears, and other engine parts.
Figure 1: The Plasma Nitriding process
Figure 2: Optical micrographs of Ti–6Al–4V alloy after plasma nitriding in nitrogen for 3 hours at 1000°C showing the formation of an α-case underneath the compound layer at (a) low magnification and (b) high magnification.
Source: Edrisy, A. & Farokhzadeh, K. ‘Plasma Nitriding of Titanium Alloys’. Plasma Science and Technology - Progress in Physical States and Chemical Reactions. Available at: https://api.intechopen.com/chapter/pdf-preview/49712 [Accessed: 17th April 2019]
The biggest challenge with PN methods is high temperatures during processing (usually above 540º Celsius). Not only is it costly, but Ti deformities from thermal distortion should still be considered a possibility. Lower temperature processes may reduce the coating hardness, but avoid the risk of spalling and cracking.
If designing for heavy loads on large machine parts, like shafts and spindles, PN offers huge benefits as it generates a surface hardness between 1100-2500HV for Ti materials.
Titanium Anodising
Titanium anodising is typically used for improving strength by increasing the thickness of the oxide layer on the metal’s surface.
Ti-Med 2 (type 2) anodising is primarily used on titanium for medical implants and in the aerospace industry. Qualities include enhanced friction performance, anti-galling, increased wear resistance and little-to-no dimensional change (the primary benefit).
Anodising is a preferred choice in the metal finishing of products. By adjusting the oxide level of the metal’s surface, the spectrum of light is changed, altering the perceived colour. This delivers the advantages of hardening and colouring, without changing titanium’s mechanical properties.
The end result also provides a lasting colour and allows easy identification and organisation of parts within complex designs (as with planes). The sanitary, additive-free finish allows the alloy to retain its high resistance to corrosion and heat.
Plasma Electrolytic Oxidation (PEO) for Titanium
Plasma electrolyte oxidation (PEO)-induced coatings are capable of withstanding more than twice as much wear versus SAE52100 steel (in block-on-ring dry sliding wear tests). They also address the issue of cracking.
The 3-stage coating process is favoured for its comparative flexibility. For example, during the process, the electrolyte bath can be modified for the introduction of new materials in the coating This gives the Titanium materials a bespoke-to-application characteristic that suits the engineer’s design.
The innovation of PEO applications has led to its adoption in the most competitive aerospace, defence, automotive, and medical companies.
Specific benefits for Ti materials undergoing the PEO process includes a reduction to the coefficient of friction from ∼0.8 to ∼0.4 against steel, which would lessen the damage from galling.
Conclusion
The likes of the aerospace and medical implant industries rely heavily on titanium, and for good reason. Titanium is often called on for its corrosion resistance and success with high temperatures. In some industries, it has become standard.
To improve the lifespan of your parts and remain competitive, businesses must seek the correct treatments for their titanium. Materials science companies like Keronite continue to develop new solutions and are frequently surprised by the likes of plasma electrolytic oxidation; new, dynamic techniques that improve performance without compromising.
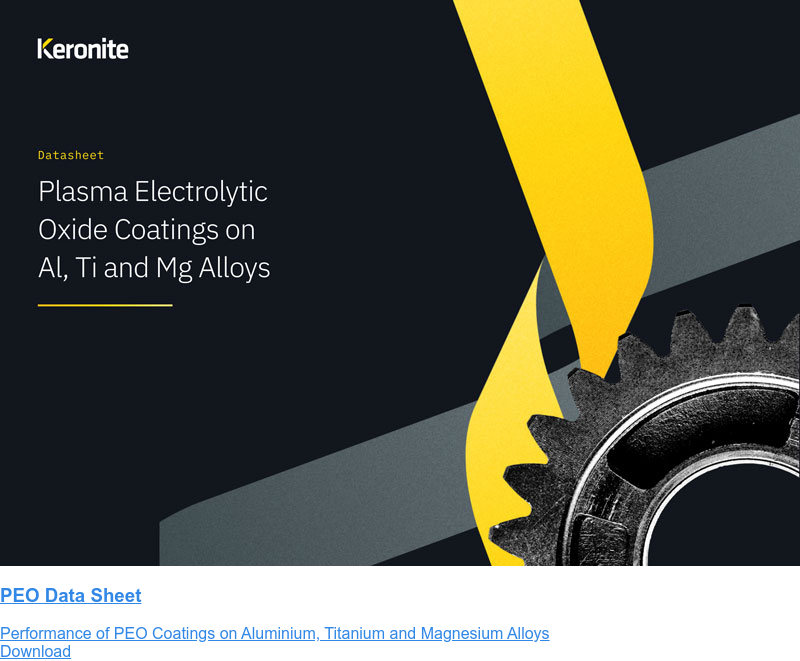
