New types of magnesium alloys and their performance
17 January 2023Magnesium-based components are becoming increasingly popular in a range of industries. As a result, there is a growing focus around magnesium alloys that improve the metal’s qualities whilst diminishing its integration challenges. Materials scientists are producing new and exciting magnesium alloys that exhibit innovative features and characteristics, helping to expand the metal’s application repertoire moving into the future.
Ultrastrong alloys - strength and ductility
It is well known that magnesium has a low surface hardness, making it difficult to use in hard-wearing and load-bearing applications. Moreover, it also exhibits inferior properties of yield strength and deformation capacity when compared to more widely used metals like aluminium and steel. Traditional cast and wrought magnesium alloys improve this strength up to 160 and 300 MPa, but these figures fail to meet required standards after more testing.
Recent advancements in material science have brought about the discovery of ultrastrong magnesium alloys. These alloys have nanocrystalline structures that have finely spaced stacking faults (SF) via long-period stacking order (LPSO) phases, or exhibit quasi-crystalline structures. SFs are planar crystalline defects in metals and alloys that can be tailored to increase strength and ductility, whereas quasi-crystals are intermetallic structures that are closely packed and exhibit high hardness and strength. By carefully adjusting the metallic content of Mg-TM-RE alloys, material scientists can achieve yield strength values ranging from 450 to 600 MPa, enabling the future possibility of magnesium in high-weight applications.
New high-pressure die casting alloy - extreme thermal resistance
The flexibility and ductility of magnesium makes it extremely easy to machine and capable of being injection moulded. Because of this, high-pressure die casting (HPDC) is a common process for mass producing complex geometry components from magnesium and magnesium alloys. However, there are no HPDC magnesium alloys available that maintain reliable structural and mechanical performance above 200°C for extreme thermal applications.
Materials scientists have recently developed a die-cast magnesium alloy (Mg-RE-Al) that exhibits reasonable yield (94 MPa) and tensile strength at temperatures up to 300°C. This is a 42% increase over the next best high temperature die-cast magnesium alloy with stable stiffness in extreme conditions. In light of this innovation, automotive and industrial engineers will soon be able to integrate complex magnesium components into combustion engines and power tools to save weight and maintain sufficient performance.
High-heat conductivity alloys - impressive heat dissipation
Heat dispersion and removal are important factors for electronics in order to avoid damage to components via overheating. Metal heat sinks are used within specialised designs to effectively dissipate the heat produced by these components in order to increase their lifespan. Aluminium is the most commonly used metal for these components as it is affordable and exhibits an efficient 210 W/m-K (watts per meter-kelvin) of heat dispersion.
Electric vehicle and handheld device designers are increasingly seeking ways to reduce the weight of their devices to improve power efficiency and provide more streamlined designs. This is achievable via magnesium, but many alloys exhibit a considerably weaker 68 W/m-K that is too low to protect important components from thermal damage.
Materials scientists have now developed a magnesium alloy (Mg-Si-Zn-Ca) that has a thermal conductivity of 126 W/m-K. This allows device designers to effectively incorporate magnesium into heat sink components to save weight and improve the efficiency of their designs. Moreover, this opens up the use of magnesium into a range of new applications by exhibiting exciting new heat dissipation properties.
Reinforcing innovative alloys using PEO
The innovative properties showcased by new magnesium alloys bolsters its title as the metal of the future. Not only does it exhibit an extraordinary strength-to-weight ratio as a standalone metal, but is now also showcasing extreme strength, heat conductivity and thermal resistance through revolutionary materials science.
The surface coating method of PEO supports the material science innovation of light metals like magnesium by providing resistance to wear, corrosion and more. Magnesium based components are placed into an electrolyte bath where an electric current is passed through to create a ceramic coating on the alloy’s substrate. As a result, the PEO-coating component gains resistant qualities to counteract the integration challenges of magnesium alloys. To find out more about how PEO coatings perform on magnesium alloys, click below to download the whitepaper.
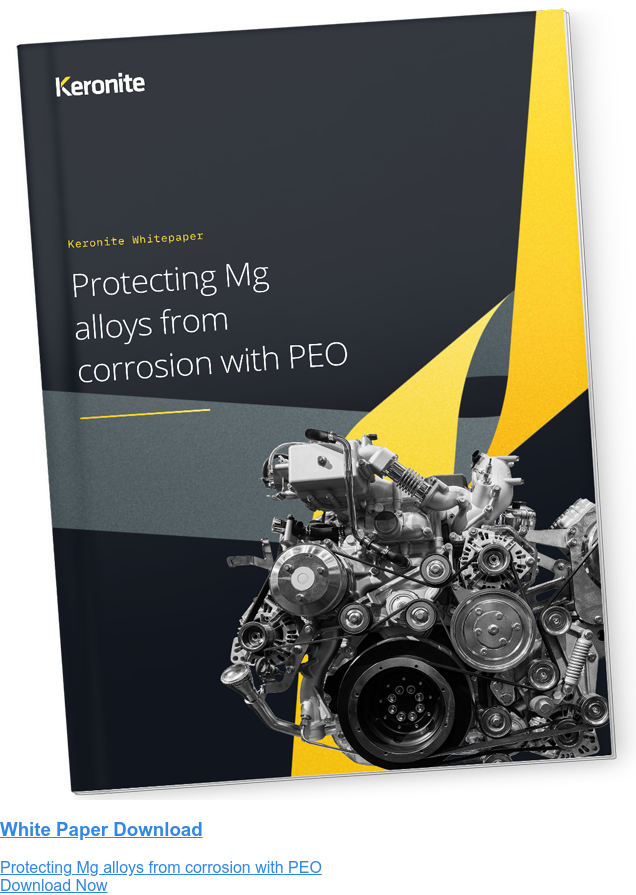
