Everything you need to know about Magnesium Alloys
23 December 2022Magnesium is being described as the metal of the future, with global demand expected to grow by about $1.1bn between 2022-2026. Its impressive strength-to-weight ratio, castability, machinability and damping qualities make it an attractive metal for a range of industries, with big automakers like Ford and Volkswagen integrating it into their mass-produced designs.
Features
Lightweight & simple castability - Magnesium holds the title of being the lightest structural metal on earth. It has a density of 1.7g/cm3, making alloy components between 50-70% lighter than those of steel and 15-30% lighter than aluminium components. It is also flexible, making it easy to machine and cast whilst also enabling the use of injection moulding.
Strong & dampening - Even though magnesium is light and flexible, it has an impressive strength-to-weight ratio. It also provides a good level of stiffness due to its hexagonal, close packed crystal structure. Cast magnesium alloys have a tensile strength of up to 280 MPa and yield strengths of up to 160 MPa. Wrought magnesium alloys have even greater strengths, with up to 360 MPa tensile and 300 MPa yield. Alongside its strength, magnesium also has impressive dampening properties caused by the high mobility dislocations in the metal.
Abundant, green & recyclable - Alongside being the lightest metal on earth, magnesium is also one of the most abundant elements on its surface. Over 60 different minerals are known to have a magnesium content of 20% or greater, making it the eighth most abundant element in the earth’s crust. Magnesium is also 100% recyclable and dissolves naturally when being disposed of, making it one of the most eco-friendly metals as well to tick all three boxes.
Applications
Automotive
The combined features of lightweight, high strength and easy castability has made magnesium a widely used material in the automotive industry. It was initially used in the 1920s for racing cars to reduce weight and improve handling. Since then, magnesium has become an integral part of automotive production to improve fuel efficiency by reducing weight.
Aerospace
Aerospace engineers are regularly trying to reduce the weight of their designs whilst meeting safety compliance of components. In light of this high demand for high-performing and lightweight materials, magnesium alloys are becoming increasingly adopted; helicopter transmissions, electronic housings and flight control systems are all taking advantage of the lightweight and high strength properties of the material.
Electronics
Amongst its properties of lightweight, strength and sustainability, magnesium also exhibits electrical conductivity and EMI shielding properties. All these features combined make magnesium a perfect material choice for electronic applications that wish to replace materials like plastic that are unsustainable and less effective. Cameras, laptops and portable media device housings are increasingly incorporating magnesium into their designs as a result.
Challenges
Magnesium is susceptible to corrosion as its outer oxide layer fails to adequately protect components in acidic and neutral environments, rapidly exposing the metal underneath to further attack. So, unless it is alloyed with other elements to improve its corrosion resistance, or is protected with a surface coating, magnesium’s applications can be limited.
That said, even when magnesium is alloyed together with aluminium it remains susceptible to corrosion in carbon dioxide or sodium chloride containing environments. It is also susceptible to wear due to its low hardness and high chemical reactivity, making it unsuitable for long-term usage in wear heavy applications. Both of these weaknesses make surface coating a necessary factor in incorporating magnesium based components into designs.
PEO as a coating solution for magnesium
The lightweight, strong and sustainable features of magnesium alloys place it as the alloy of the future. Designers from a range of industries can improve designs by incorporating the metal, but require sufficient coating to ensure components are properly protected from corrosion and wear. The unique surface coating technology of plasma electrolytic oxidation (PEO) provides protection against these elements and more.
To coat magnesium components using PEO, they are placed into an electrolyte bath where an electric current is passed through to create a ceramic coating on the alloy’s substrate. As a result, the PEO-coating component gains wear, corrosion and heat resistance qualities to counteract the integration challenges of magnesium alloys. To find out more about how PEO coatings perform on magnesium alloys, click below to download the whitepaper.
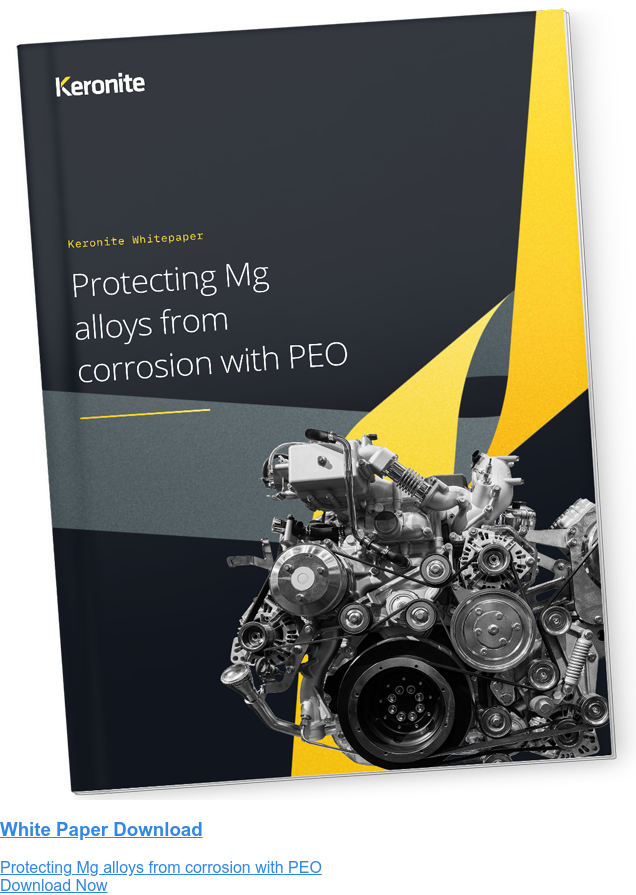
