Corrosion resistant coatings for magnesium alloys
12 April 2021Magnesium offers a range of opportunities to create lighter, more efficient, and better performing components. Across a number of sectors, including the automotive and aerospace, defence and oil & gas industries, magnesium is being increasingly used to overcome some of the most pressing challenges of the current times.
As one of the lightest, yet affordable, structural metals available, magnesium and its alloys offer no shortage of opportunity. However, with low wear resistance and its susceptibility to corrosion, this otherwise benefit-rich alloy has not yet reached its full potential for many applications.
Depending on the specification, magnesium alloy components can be between 50% and 70% lighter than stainless and high strength steels, as well as a 15% and 30% weight advantage over aluminium. Not only does it tick all the boxes for lightweighting, but it also has low density, high mechanical stability, high electrical and thermal conductivity and the inherent strength many applications require.
Naturally, the question of corrosion arises. Its high chemical instability means it can corrode quickly, limiting its use in a number of applications. For this reason, surface coatings are critical to making these materials variable. To perform adequately, it needs to perform in highly abrasive environments, all while being a sound commercial decision, too.
The mechanisms of magnesium’s corrosion
Corrosion is the process of metals reacting with elements in the environment and transforming into substances such as oxides, hydroxides and sulphides. This electrochemical redox reaction includes both reduction and oxidation, meaning the metal loses electrons.
This loss of electrons can have a significant impact on the performance and stability of a metal, and as a group II element with low ionisation energy and only two electrons in the outermost shell of the atom, magnesium will corrode even in ambient conditions.
Corrosion causes cracks that propagate and lead to failure of components, and even entire systems. Corrosion mechanisms in magnesium and its alloys explains more on the science behind corrosion, how the electrochemical redox reaction works and why magnesium in particular suffers corrosion so readily.
The real cost of industrial corrosion
Corrosion is an issue that impacts on nearly all machinery. It is a problem that, according to the National Association of Corrosion Engineers’ recent IMPACT study, the real cost of industrial corrosion to the global economy is approximately $2.5 trillion annually.
The IMPACT study states that a fifth of this cost is met by the industrial sector, and manifests in several ways:
- Machine downtime
- Equipment replacement
- Overdesign
- Contamination
Corrosion-resistant surface coatings are the key to unlocking magnesium’s potential
Advances in surface coating technology have made it possible for engineers to unlock the potential of magnesium, by protecting magnesium components from corrosion and wear.
This is an exciting prospect given its hexagonal, close-packed crystal structure and density of 1.7g/cm3, making it the lightest structural metal available to engineers with an impressive level of stiffness.
A range of surface coatings preventing the corrosion of magnesium are applied, which include
- Anodising
- Thermal spray coating
- Plasma electrolytic oxidation
- Electroplating
- Chemical plating
- Chemical vapour deposition
- Conversion coating
- Powder coating
- Paints
One surface coating that has proved particularly effective at unlocking the potential of magnesium is Plasma Electrolytic Oxidation (PEO). In fact, a study by automotive giant, Ford, revealed that PEO was the only surface coating technology capable of providing superior corrosion protection when compared to conventional chrome-based conversion techniques.
PEO coatings for magnesium alloys
PEO is an electrolyte bath-based conversion coating process that uniquely improves the performance of light metals and their alloys, including magnesium. This is of increasing interest to industries looking to deliver lightweighting strategies by replacing heavier metals, all whilst maintaining the metal’s unique performance characteristics required by complex and often hostile environments.
The magnesium/magnesium alloy component is placed in an electrolyte bath. An electric current is passed through the bath. An oxide coating develops on the magnesium substrate. The electrolyte becomes part of the coating, which is further modified by a plasma discharge. This enables engineers to specify additional surface coating properties by varying the composition of the electrolyte.
There are several PEO technology providers that vary in performance, and it is a valuable exercise to compare, such as reviewing Keronite’s technologies for magnesium coating to that of alternative provider Magoxid.
PEO provides industry-leading corrosion protection for mg alloys
As introduced above, Keronite’s G3Mag PEO coating uses a combination of an electrolyte bath and plasma over three distinct stages, forming a ceramic-like duplex coating on magnesium alloys.
It has been rigorously tested in a range of corrosive environments with impressive results, including a six-hour salt spray test using 4% sodium chloride (NaCl) at 80°C. At the end of the experiment, the test strip of a ZE41A alloy showed absolutely no corrosion.
Magnesium in the defence sector
Weight reduction is an ongoing challenge for design engineers working in the defence sector, with applications such as lightweight airframes that enable greater fuel and ordnance payloads, balancing heavy armour with range and mobility, plus reducing infantry kit loads.
To broaden the use of magnesium in the defence sector, PEO coatings can be tailored to suit the exacting, but sometimes varied demands of military applications. By adjusting the PEO process, specific performance characteristics can be achieved, including:
- Improved hardness for the most corrosive environments
- Less friction and wear for high-use components
- Better dielectric strengths
- Increased thermal resistance for high temperature and high speed applications
How automotive OEMs can expand magnesium applications
Automotive engineers face increasing pressure to accelerate lightweighting strategy implementation, with increasing legislative pressure to drive greater fuel efficiency.
There are many automotive components commonly made using magnesium alloys, from engine blocks, gear boxes and clutch housings, to structural elements such as the steering wheel column, roof frames and engine cradles.
By enhancing corrosion and wear resistance, PEO is set to broaden this scope even further, providing automotive engineers with multiple solutions for designing and specifying components and sub-assemblies.
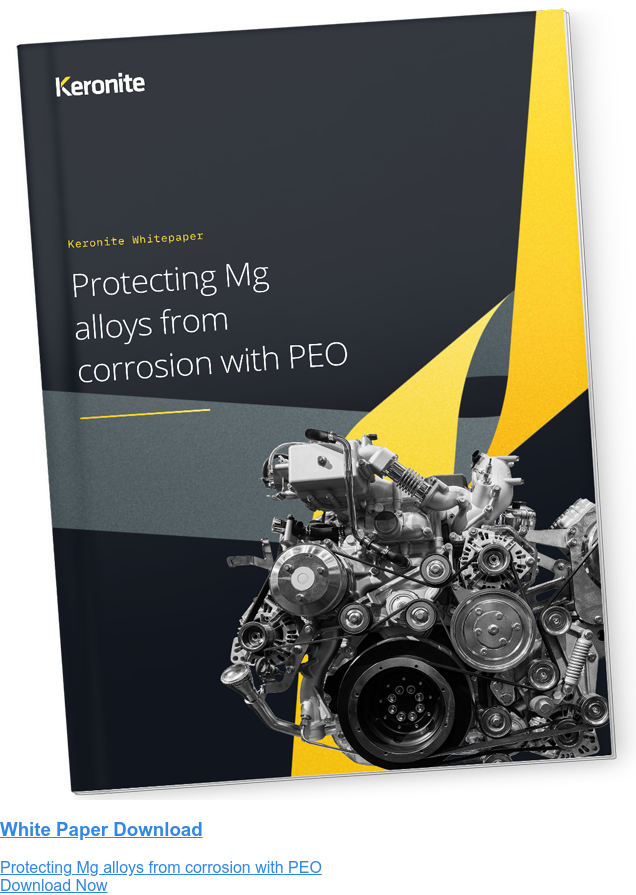
