Can magnesium alloys work in structural aerospace applications?
20 July 2023Structural materials used in aerospace are required to meet exacting performance (and safety) standards whilst being as lightweight as possible. It is therefore an ongoing challenge for manufacturers to find techniques that reduce the weight of their aircraft, where every gram of component matters. Thanks to their impressive strength-to-weight ratios, magnesium alloys are extremely useful lightweighting options in an engineer’s arsenal.
Corrosion control & enhancing the life of Mg alloys
Primarily because of magnesium’s high levels of chemical activity (giving poor thermal management and increased levels of corrosion), its alloys have not always been routinely specified for use in structural applications in the aerospace industry. They also have poor creep resistance, which can render components unsuitable for use in high temperature environments such as those found at launch and take-off.
Chrome platings have been widely used, thanks to the improved hardness, durability, corrosion resistance and smooth finish they give. However, toxic chrome is now being increasingly phased out across the aerospace industry. Chrome components and platings are being replaced by lighter materials such as coated magnesium alloys, that are not only greener on production, but also contribute to greater fuel efficiency and reduced CO2 emissions in use.
Coated magnesium alloys offer new solutions for aerospace engineers
Across high performance industries such as aerospace, there is continued demand for advanced lightweight and high-performing materials that are corrosion resistant. Coated magnesium alloys can now offer component designers high-temperature characteristics, pressure tightness, and the ability to consistently produce complex shapes by casting, machining, extruding, or forging, in large volume. The use of surface-treated magnesium alloys enables engines and power transmission systems to run safely at higher temperatures without gear misalignment or the need to seal the component against oil seepage.
Of course, in any sector (such as aerospace) that is governed by strict regulations and requiring extremely tight manufacturing tolerances, it's important that any and all new developments, such as surface coatings, are strictly controlled. Working together with a leading aerospace manufacturer, Keronite has developed a pre-treatment for magnesium components, Plasma Electrolytic Oxidation (PEO), which has greater adhesion than comparable processes and therefore improves resistance to wear, corrosion and high temperatures. Advances in PEO technology have brought additional, and very significant, benefits - reducing the need for protective paintwork, which can otherwise add approximately one tonne to the weight of an aircraft. PEO-coated magnesium components can therefore drive impressive weight reductions, as well as improving maintenance requirements.
PEO technology enables new aerospace applications for magnesium alloys
Aerospace engineers specifying coated magnesium alloys for use in structural applications can now benefit from their excellent strength-to-weight ratios with no compromise on levels of wear and corrosion. PEO brings a number of benefits for the very specific challenges of the aerospace sector:
- Providing thermal stability up to 900oC. AS8049 of the SAE Aerospace Safety standards allow magnesium components into commercial cabin interiors, as magnesium alloys can now meet tough flammability standards
- Enabling the corrosion protection of magnesium without the use of outlawed chrome or any restricted metals
- Providing minimal fatigue debit, with less than 5% reduction in the endurance limit of some magnesium alloys
- Featuring incredibly high wear protection
- Acting as an ideal ‘key’ for any subsequent coats used in duplex coating systems
- Environmentally sound - the process does not employ any restricted or hazardous substances. This contrasts with treatments such as chromic acid anodising, dichromate sealers, hard chrome plating and chromate conversion coatings that are now increasingly regulated
- Enabling aerospace manufacturers to become REACH and RoHS compliant
In conclusion, Keronite’s PEO process makes magnesium alloys highly suitable for use across a wide range of structural applications in the aerospace sector. Bringing increased hardness, thermal and chemical stability and high levels of resistance to corrosion, surface-treated magnesium alloys can very successfully address the many challenges faced by engineers when lightweighting aerospace projects.
You can learn more about the many benefits of plasma electrolytic oxidation for magnesium alloys in the technical data sheet.
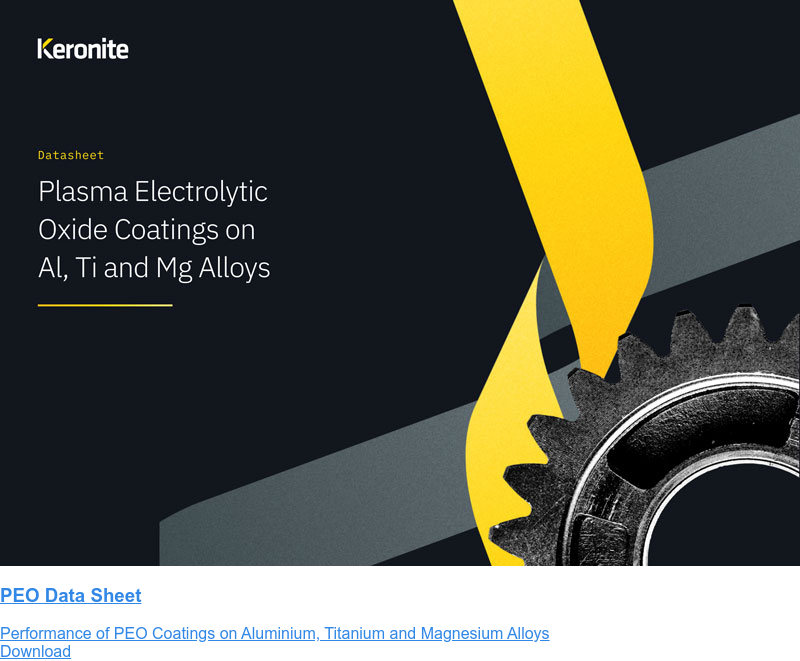
