Magnesium alloys - uses, applications and benefits
12 April 2022Whether cast or wrought, magnesium alloys bring excellent strength-to-weight ratios to a wide range of engineering projects. Up to 70% lighter than stainless steel and a third lighter than aluminium, easy to work with, possessing the highest known damping capacity of any structural metal and low in cost, magnesium alloys feature in applications as diverse as automotive, defence, electronic, aerospace, biomedical, manufacturing and green energy technologies.
The benefits of magnesium alloys
Invaluable in environments where components and equipment are required to be lightweight, magnesium alloys offer engineers and material scientists practical, high-performing and readily available solutions to the perennial challenge of optimising strength, weight, power and cost. Magnesium alloys offer a number of specific advantages over alternative materials.
Lightweight. With a density of 1.7g/cm3, magnesium is the lightest structural metal available. Its alloys are therefore ideal for projects where weight is a key concern, giving a weight advantage over aluminium of 33%, and as much as 50% over titanium. In the automotive industry specifically, the move towards electric and energy efficient vehicles will only accelerate demands for component parts to be made ever-lighter
Strong. Magnesium naturally provides good levels of stiffness due to its hexagonal, close-packed, crystal structure. Cast magnesium alloys have tensile strengths up to 280 MPa and yield up to 160 MPa, while wrought magnesium alloys are produced with tensile strengths up to 360 MPa and yield strengths up to 300 MPa.
Plentiful. Magnesium is the eighth-most abundant element on the planet, making it a cost effective and readily available choice. Magnesium alloys are the third-most popular non-ferrous casting material.
Resistant to unwanted mechanical vibrations. Magnesium has the highest known damping capacity of any structural metal, capable of withstanding 10x more than aluminium, titanium, or steel. It is also flexible, making it easy to machine and cast and meaning it can be injection moulded.
Widely recyclable. Posing no toxicity hazards, magnesium alloys are helpful for enhancing any project’s post-life green credentials. It’s also highly biocompatible – minimal levels of degradation or decomposition are found, resulting from interaction with bodily fluids when used in cardiovascular or orthopaedic devices.
Magnesium alloys in widespread industrial, medical and commercial use
PEO benefits from not being a line of sight process, the process can be adapted to the most complex geometries, including blind holes, bores and pockets. Because of their multiple benefits, magnesium alloys are frequently specified for use across almost every industrial sector and can be found in many aspects of daily life. Common uses include:
- High-speed industrial machinery, such as looms and printing presses
- Helicopter rotor blades and aircraft landing wheels
- Gearbox casings, brake housings and drive shafts
- Medical implants, surgical devices and prosthetics
- Glasses and optical equipment
- Cameras, laptops and phones
- Power tools
- High performance bikes and wheels
- Sporting equipment
- Domestic appliances such as vacuum cleaners and kitchen electricals
Addressing undesirable properties of untreated magnesium alloys
Counterbalancing their many benefits, magnesium alloys do have some characteristics that can make them less attractive options, rendering components susceptible to rapid corrosion and wear in demanding environments and high-performance applications due to magnesium alloys’ inherent low ductility, reduced creep resistance, low rigidity, high chemical reactivity, making them prone to galvanic corrosion, softness and flammability.
Because of their high reactivity, magnesium alloys greatly benefit from surface-coating to make them compatible with use in applications where wear and corrosion are particular concerns. There are a number of options available to engineers wishing to improve the performance and lifespan of magnesium alloys including cold spray, electroless nickel plating (ENP) and plasma electrolytic oxidation (PEO).
As well as providing performance enhancements, coatings can modify the characteristics of an alloy’s surface in other positive ways: improving the friction coefficient, introducing antibacterial properties or even improving the dielectric breakdown strength.
Keronite’s unique PEO process gives magnesium alloys corrosion and wear resistance, allowing engineers and materials scientists to specify them for use in applications where they might otherwise have been ruled out. Their low levels of thermal conductivity mean that PEO-treated magnesium alloys can function well as thermal barriers, helped also by their excellent adhesion properties.
Our approach is highly collaborative, working with project teams early on so that bespoke approaches and solutions can be developed to any and all engineering challenges. Following the PEO process, magnesium alloys are more resistant to corrosion, stronger and more stable than in their untreated state, greatly enhancing their suitability for almost every application, in every industry.
You can learn more about the many benefits of plasma electrolytic oxidation for magnesium alloys in the technical data sheet here.
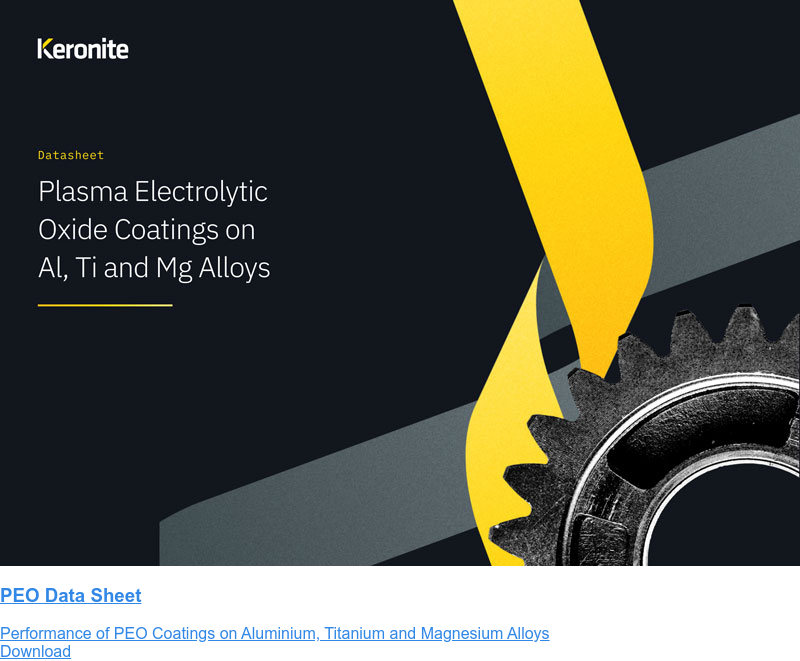
