High-Hardness Surface Coatings for Dry Sliding Wear Resistance
30 March 2020Historically, light alloys haven’t been well suited towards applications involving friction. While they do offer extremely positive strength-to-weight ratios, their poor wear resistance limits their use. This has led to steel’s – and other heavy metals – continued dominion over light alloys, even where weight is a key factor.
Materials science is a continually evolving field. As technology improves, new surface coating solutions are emerging. Light alloys are now capable of offering equivalent wear performance, while retaining their weight-saving properties. This means that, with the right surface technology, light alloys can be enhanced for friction and dry sliding wear performance.
What is sliding wear?
Dry sliding wear occurs when two surfaces slide over each other. Sliding wear on the surface of light alloy components occurs in two ways:
- Abrasive wear happens when there are hard particles between the two surfaces. These particles scrape or plough material from one or both of the surfaces, causing material loss.
- Adhesive wear is caused when the two surfaces bond during sliding and material is transferred from one surface to the other or lost. This type of wear is most common when there is no lubrication.
Wear is progressive, and the material loss increases as the motion continues or increases. The eventual result is wear failure as a result of the surface changes caused by the wear. Wear can also contribute to an accelerated rate of corrosion.
Sliding wear resistance
Wear comes in many forms, with different types of relative motion producing various material-removing impacts on light alloys. For a light alloy to become more resistant to wear, there are several key characteristics required. Hardness used to be thought of as the key characteristic for wear performance. However, compliance, i.e. the ratio of stiffness to tensile strength, is also key. For this reason, a cobbled road will be more hard wearing than a single tarmac layer.
An uncoated light metal alloy, such as an aluminium or titanium alloy, has a low wear coefficient. As a result, when a light alloy component is subject to wear under operating conditions, it will lose material at an accelerated rate, thereby reducing the useful life of a component.
However, by adding a surface coating, the performance characteristics of the light alloy can be radically altered. For example, the wear coefficient of aluminium oxide is significantly higher than the wear coefficient of a typical aluminium alloy. It loses much less material when subjected to wear and is therefore less likely to fail, in theory. But not all surface coatings are able to withstand the same levels of wear.
Surface coatings that significantly increase the wear coefficient of light alloys include hard anodising, nitriding, electroless nickel plating and plasma electrolytic oxidation.
Plasma Electrolytic Oxidation (PEO)
Plasma electrolytic oxidation is an advanced surface coating solution for light alloys. Coatings are created by applying a current to a component in an electrolyte bath, like anodising. However, by applying higher voltages and complex electrical regimes, PEO instigates plasma discharges. This helps create a compliant, highly adhesive layer with high hardness.
One of the key features of the process is the control scientists have over the resultant coating. By altering the electrolyte composition, voltage, electrical regime and component fixture, the coatings characteristics can differ. This enables materials scientists to create bespoke-to-application coatings that provide the wear resistance necessary for the requirements of the design.
PEO coating structural metallurgical factors improve wear resistance
PEO grows a crystalline oxide film coating on the underlying substrate that has an irregular porous microstructure, as shown in figure 1. Pore length ranges from nm to microns, as can been seen in figure 2.
The irregular structure reduces adhesive wear, as the irregular surface is difficult to bond. The oxide layer is partially formed from the substrate and is tightly bonded. Together with the irregular crystalline structure, it provides a friction-bearing surface that has high strain tolerance and hardness. The edges of the coating around complex shapes are crack free. This prevents impurities lodging in the surface and causing abrasive wear.
Figure 1: Crystalline oxide film
Source: University of Cambridge, The Gordon Laboratory https://www.ccg.msm.cam.ac.uk/research-areas/the-plasma-electrolytic-oxidation-peo-process
Further customisation of the surface coating is possible by adding secondary, or duplex coatings. This is again due to the irregular porous microstructure, which provides an excellent surface for adhering additional coating layers. A fluorocarbon-based duplex layer, or sealer, can be introduced that increases lubricity, reduces friction and therefore reduces wear.
Figure 2: Irregular surface structure of PEO surface coating.
Source: https://en.wikipedia.org/wiki/Plasma_electrolytic_oxidation#/media/File:PEO_surface.jpg Reproduced under a creative commons licence. No owner specified.
As highlighted above, hardness is one of the key components of the wear coefficient. When compared to other materials and surface coatings, PEO has significantly greater sliding wear resistance, as shown in figure 3 below.
Figure 3: PEO wear resistance compared to other materials and coatings.
Source: Keronite whitepaper PEO sealers.
Conclusion
Sliding wear resistance is an essential property for light alloys used in high performance applications. Materials with a high wear coefficient resist wear and are less likely to fail when used in sectors such as aerospace, automotive, oil and gas and industry. Light alloys typically have low wear coefficients, but surface coatings can improve this. PEO’s unique crystalline oxide film coating with an irregular porous microstructure provides light alloys with a sliding wear-resistant surface. PEO coatings enable high performance applications to benefit fully from the strengths of light alloys.
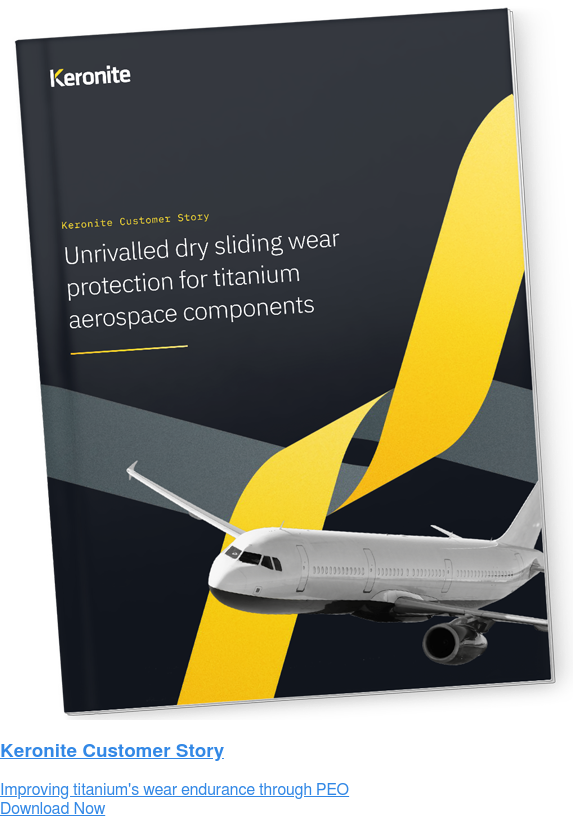
