Is there a growth market for magnesium alloys in automotive?
14 February 2023The magnesium alloy market is seeing steady growth thanks to its increase in use across industries such as defence, aerospace and automotive. The automotive industry in particular is a driving force for this growth, from reducing the weight of luxury and racing vehicles to improving the fuel efficiency of new commercial designs. However, there are challenges still to overcome for magnesium alloys to become widely used and accessible to automotive consumers worldwide.
Why are magnesium alloys being used in the automotive industry?
Magnesium as a standalone metal has an impressive strength-to-weight ratio, effective vibration dampening capabilities, and is the eighth most abundant element on the planet. These features make it an attractive choice for the automotive industry to improve fuel efficiency and reduce the CO2 emissions of designs. That said, magnesium faces challenges of strength and creep resistance that can make it difficult to integrate into a range of components.
Magnesium alloys solve many of these challenges that inhibit its widespread use. They provide greatly improved strength (upwards of 300 MPa yield and tensile strength) whilst maintaining effective ductility and castability for mass production. As a result, magnesium alloys are becoming increasingly popular in the automotive industry as the third most used metallic material in automotive designs.
Market growth for magnesium alloys
The use of magnesium alloys have been growing dramatically in recent years, with a market that is expected to account for approximately $2 billion by 2029. A significant amount of this growth is driven by the widespread use of magnesium alloys in the automotive industry. Both die casting and aluminium alloying in the automotive industry account for almost three-fourths of the total growth of the magnesium alloy market (approximately 35-37% each).
Examples of this market growth are shown in a range of modern automotive designs by established manufacturers. The Volkswagen XL1 showcases the use of magnesium alloys in stiffening beam supports, wheels, and crash structures. More specialised examples include the Porsche 911 GT3 RS which has a magnesium roof and wheels to maximise weight reduction. Though these are luxury designs, they showcase the application and future potential of magnesium alloys for commercial automotive components.
What are the challenges of using magnesium alloys for automotive designs?
The increasing popularity of magnesium alloys has, inadvertently, also raised attention to the challenges of using it for automotive components. The main obstacles in the way of mass market expansion for magnesium alloys is cost uncertainty, corrosion resistance and temperature creep.
- Cost uncertainty - Even though magnesium is one of the most abundant materials, demand is incredibly high and only increasing. Many industries as well as automotive have a high demand for magnesium to optimise the weight of their designs, making it a very competitive market. Because of this, European magnesium prices surged near 100% in 2021 amid supply cuts.
- Corrosion resistance - Magnesium is a highly reactive metal, making it susceptible to galvanic, pitting and stress corrosion. Where alloying can help improve strength and creep resistance, many fail to provide sufficient corrosion resistance to be effectively used in a wide range of components.
- Temperature creep - For automotive components like engine blocks, metals need to have a high temperature creep resistance to maintain sufficient stiffness and strength at extreme temperatures. One of the highest temperature creep resistant magnesium alloys are those created via high-pressure die casting (HPDC) of up to 200°C, which is insufficient for a range of automotive designs.
PEO - Innovative coating technology that enables magnesium alloy components in the automotive industry.
The use, demand and popularity of magnesium alloys is growing at a steady rate in the automotive industry. It’s lightweight, strong and versatile features make it an ideal choice for a range of applications. However, its weaknesses to extreme heat and corrosion make it unsuitable in a range of components, further driving the cost uncertainty of the metal compared to other traditional alloys like aluminium.
Advanced surface coating technology can help solve these issues by providing magnesium alloys with sufficient protection from corrosion, heat and more. Plasma Electrolytic Oxidation (PEO) is an innovative surface coating technology where plasma modifies the surface structure of magnesium alloy components submerged in an electrolyte bath. It creates an ultra-hard, incredibly adhesive layer which provides a range of surface characteristics.
In a study conducted by Ford, the automotive manufacturer, PEO was the only surface coating method which provided superior corrosion protection when compared to conventional chrome-based conversion techniques. If you want to find out more about PEO and how it can introduce magnesium alloys to your automotive designs, contact a member of our team today or download the whitepaper.
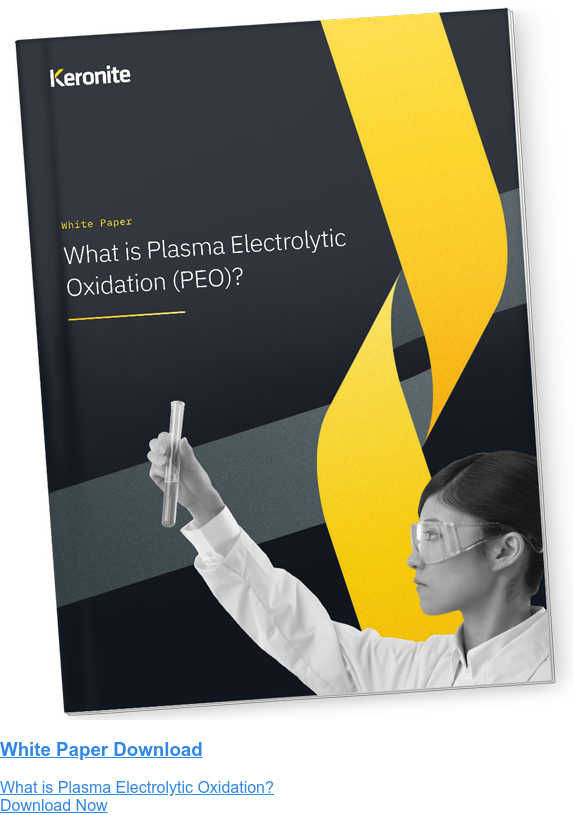
