Assessing the role of magnesium in structural applications
31 January 2023Magnesium was a structural part of the aerospace, defence and automotive industries during the early to mid 20th century. Its impressive strength-to-weight ratio, flexibility and sheer abundance set the stage of modern engineering by reducing the weight of designs and improving efficiency. However, the various weaknesses of magnesium have caused its use to diminish as a structural metal, which is something modern materials scientists are seeking to reverse to enable lighter designs across industries.
How effective is magnesium for structural applications?
Historically, magnesium’s use in structural applications has been widespread across industries, so much so that it is the third most used metal for structural applications behind steel and aluminium. Magnesium is the 8th most abundant metal, has an impressive strength-to-weight ratio, and is extremely lightweight, which are all factors that attribute to its popularity as a structural metal. But in modern applications where conditions are more extreme and demands of the metal are higher, the various weaknesses of magnesium have become increasingly apparent.
Magnesium has typically weak ductility, low fatigue/yield strength and is extremely reactive, making it susceptible to corrosion. All of these weaknesses result in the metal being the inferior choice when compared to its stronger counterparts of steel and aluminium for specific structural applications. In light of this, materials scientists are testing new magnesium alloys and casting methods to produce structural components that can withstand extreme conditions.
What industries use magnesium for structural components?
Automotive
The structural application of magnesium has been present in the automotive industry since the early 20th century. Volkswagen introduced magnesium produced engine blocks and gearboxes using AS41 and AZ81 alloys. As a result, automotive producers were able to reduce the overall weight of vehicles and improve fuel efficiency when compared to their counterparts that used aluminium and steel based components.
The greater power requirements of engines in both operating temperature and load has since led to a drop in the use of magnesium for these components. Most magnesium alloys begin to soften and weaken at high temperatures of around 200°C, making it an unsuitable choice of structural metal for modern engine blocks. However, advancements in magnesium alloys such as new high-pressure die casting methods have elevated its operational temperature to around 300°C. Breakthroughs in the materials science of magnesium have in turn led to its resurgence and world-wide use in automotive applications as a structural metal. Moreover, as the industry is trying to push electric vehicles to eventually substitute combustion engines, structural magnesium components can also help increase their range and make them more consumer friendly. Helping bring the eventual shift to renewable driving solutions closer.
Defence
Magnesium has a longstanding history with the defence industry. It was used extensively during the World Wars for munitions, helped reduce the weight and increase the range of B-36 and B-47 bombers, and has helped optimise the structural designs of armoured personnel carriers (APCs) and other military vehicles. In the context of military vehicles, structural components such as frames, fuselages and housings were developed from magnesium during the late 20th century. However, due to the materials softness and relatively low creep resistance, modern defence industries have turned to steel, aluminium and ceramics as substitutes.
Advances in materials science and coating technology have breathed new potential into magnesium as a structural application defence industry. Ultrastrong magnesium alloys and bespoke coating methods provide greater yield strength of up to 600 MPa and a hardened outer layer to protect against abrasion and wear. As a result, defence contractors can look to take advantage of the impressive strength-to-weight ratio of magnesium to optimise their designs once again.
Aerospace
Magnesium was used extensively in the aerospace industry during the 1940s and 1950s for structural components. Its impressive strength-to-weight ratio enabled designers to reduce the structural weight of aircraft to improve performance. That said, the high reactivity of magnesium has reduced its use in aerospace due to its susceptibility to corrosion and perceived safety hazard by bodies such as the International Air Transport Association.
Magnesium has started to become a viable option in engine and transmission related components. But with the help of advanced surface coating technologies that provide sufficient protection against corrosion, magnesium could once again be a structural element of aerospace designs.
Supporting magnesium in structural applications using PEO
The automotive, defence and aerospace industries share the same relationship with magnesium as a structural metal; an early adoption before a gradual decline after realising the weaknesses and risks of using it. Thanks to modern material science, magnesium is once again revolutionising designs with its useful and impressive features. One pivotal aspect of modern material science that is helping to achieve this is advanced surface coating such as Plasma Electrolytic Oxidation (PEO).
PEO’s unique technology for light metals such as magnesium and its alloys uses an electrolyte bath and plasma over three distinct stages, which forms a ceramic-like duplex coating. During each stage, engineers can adjust the process to create tailored coatings for the exact needs of their structural application. By introducing various customizable reagents, engineers can alleviate the weaknesses of magnesium and fully enjoy its use as a structural metal.
To learn how surface coatings such as PEO enable engineers to utilise magnesium’s properties in modern structural applications, click below to download the whitepaper or contact us today.
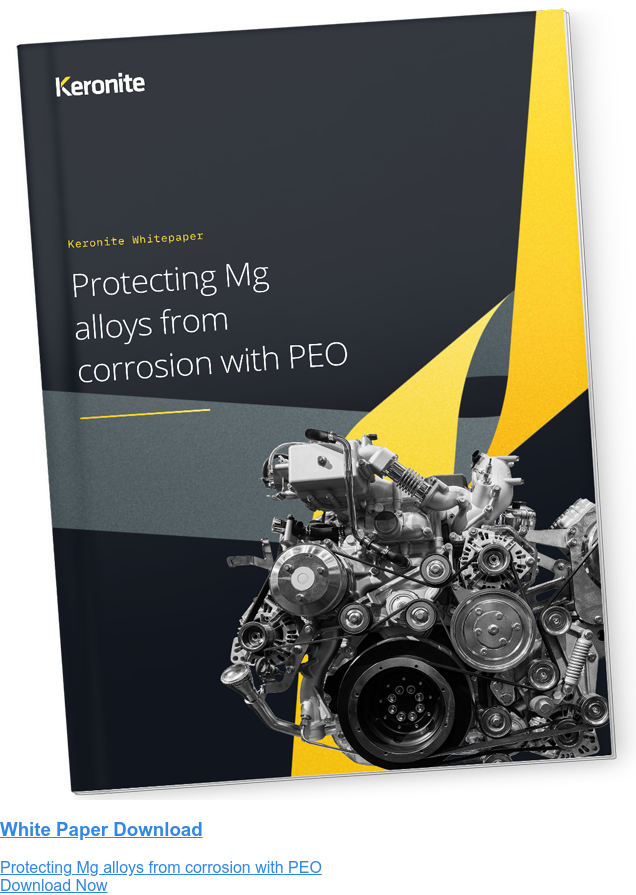
