Corrosion-resistant coatings for magnesium defence components
10 March 2021Magnesium has been used by the world’s military since at least the early years of the twentieth century. During the first world war, magnesium was a core element of many munitions, such as flares and tracers. More recent twenty-first century applications include structural components inside military aircraft, vehicles, personal equipment and ballistics.
The principal advantage of using magnesium and its alloys in military equipment is its low density. Weight reduction is a constant challenge faced by defence engineers. They are tasked with creating lighter airframes to enable greater fuel and ordnance payloads, while striking the balance of heavy armour with range and mobility.
However, most branches of the military must operate in the harshest environments, which includes everything from mud, weather conditions and oceans to corrosive fuels and fluids, munitions, chemicals and extreme operational stresses.
Magnesium has poor corrosion resistance and low strength. This means this light metal and its older alloys have been passed over for many defence applications where aluminium, titanium and even steel are more suitable.
That is until new alloys and innovative surface coatings were developed to overcome those performance shortcomings, protecting magnesium from corrosion and enhancing stiffness and hardness.
How magnesium use in military applications has evolved over time
Magnesium was used extensively in first world war munitions, such as incendiary flares and tracer rounds, where its flammability and intense light emitting properties were a benefit. During the second world war, the metal’s low density was exploited as it was used extensively in military aircraft.
Aircraft engines of the time lacked the power and efficiency of modern engines, so using magnesium in fuselages, structural frames, decking, in brackets, engine and gearbox parts and in wheels could significantly reduce weight and massively increase range. Some US aircraft, notably the B-36 and B-47 bombers, made extensive use of lightweight magnesium components to increase ordnance payloads and bombing range.
Post-war, the interest in magnesium in military aircraft waned as engines became more powerful, only to be reignited as the rocket age took off in the fifties, and then again during the Vietnam War. It was during this period that magnesium transitioned into military ground vehicles, such as the US designed M-274 ‘mule’.
Again, magnesium’s low density proved to be an advantage as the M-274 had a 450kg payload and a 120-180km range. This vehicle, with its magnesium axle housings and load platform, was used by the US military until the 1980s. Magnesium alloy has been incorporated into armoured personnel carriers (APCs), amphibious vehicles, main battle tanks (MBTs) and other military hardware.
Why many military applications are highly corrosive
Despite its seemingly widespread adoption, magnesium alloy demand has historically been fuelled by major conflict. During interwar periods, when the demand for materials has been less urgent, engineers have turned to steel, aluminium and ceramics, despite their higher weights. This was due to the metal’s softness, poor forming qualities at low temperatures, lower perforation resistance, low strength and susceptibility to corrosion.
Corrosion is a particular issue for magnesium alloys, as it is affected by uniform corrosion, galvanic corrosion, pitting and stress corrosion. During the process of galvanic corrosion, a conductive solution joins two metals, corroding one and protecting the other. And the average military hardware asset spends a lot of its time in contact with or immersed in conductive solutions. Think seawater, salt sprays, mud and contaminants from munitions, fuel and the chemicals found in combat environments, on military bases and warships.
Aluminium forms ceramic-like metal oxide films that resist the inward flow of oxidants causing low level corrosion. As another Group 2 (IIa) alkaline-earth metal, magnesium and magnesium alloys also form a film, but it is less effective and quickly corrodes in acidic and neutral environments.
This means most magnesium components operate in highly corrosive environments and rapidly degrade if not protected. Traditional and conventional protection, such as paints and powder coats, or spray-based plasma coatings, may not survive the intense conditions of the battlefield and military campaigns where the opportunities for maintenance and repair are fewer. This can lead to damaging corrosion causing catastrophic equipment failure, in turn costing service personnel their lives.
Choosing surface coatings to widen magnesium use in defence
However, the surface coating innovations of recent decades have led to the development of coatings that are tough and resilient. Plasma electrolytic oxidation (PEO) can be tailored to meet the highly varied yet specific challenges faced by the engineers who design and specify components and sub-assemblies in military hardware.
PEO’s unique technology for light metals such as magnesium and its alloys uses an electrolyte bath and plasma over three distinct stages, which forms a ceramic-like duplex coating. During each stage, engineers can adjust the process to create tailored coatings for the exact needs of their defence application.
The coating is formed from the substrate, the magnesium/alloy, and the contents of the bath, and is not an additional layer, such as a plasma or thermal spray coating or paint, so there are no bonding issues. The top layer is highly porous, so it can incorporate the contents of the electrolytic bath in the surface coating to include additional properties with the corrosion protection. These can include:
- Applying a high-sliding wear resistant PEO coating improves hardness
- Using polymers, such as PEEK (poly-ether-ether-ketone), in the outer layer introduces a built-in lubricant coating that reduces friction and wear
- Introducing insulating dielectric characteristics can be achieved by finely controlling the thickness of the PEO coating, which can be accomplished by tailoring the deposition process. The additively manufactured part’s oxide layer can be thickened to achieve dielectric strengths of 59-79 kV/mm
- A reduction in thermal conductivity can be attained by adding silicates to the electrolyte bath, which generates a mullite-rich coating that acts as a Thermal barrier coating (TBC), protecting magnesium components that are used in high temperature and high speed applications
- Corrosion resistance is improved by adding PEO coatings with chemically inert ceramic-like properties and thickening the oxide layers by adjusting the PEO process to provide the desired level of resistance. Hydrophobic properties also increase corrosion resistance – see below
- Increasing the hydrophobic properties of the component’s surface can increase corrosion resistance by preventing liquid droplets and contaminants adhering to parts.
PEO’s fine microstructure and surface texture create an ideal physical ‘key’ for top coats – resulting in much stronger adhesion of the top coat than other surface coating technologies, such as hard anodising.
This duplex system combines the improved corrosion protection of both elements synergistically to provide unparalleled corrosion protection. This enables engineers to use magnesium alloys in military applications for use on the modern battlefield that were previously not possible.
To learn how surface coatings such as PEO enable engineers to exploit the full range of magnesium’s properties in wider defence applications by preventing corrosion, click below to download the whitepaper.
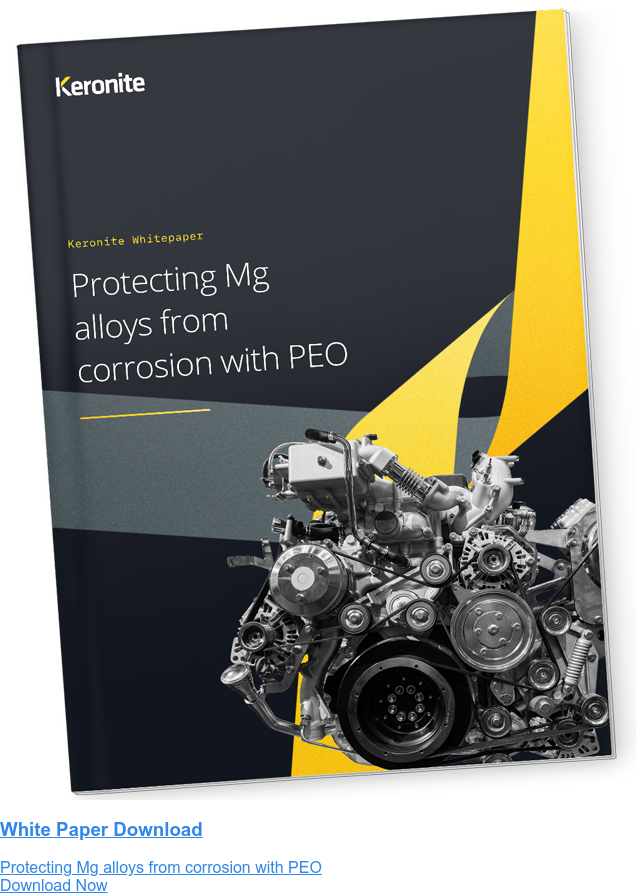
