How surface coatings are enabling automation in the medical market
8 July 2019Medical instruments are every bit unique. Surgical instruments, for example, come in varying shapes and sizes and with a wide range of applications. Some instruments, such as surgical scissors, forceps, and scalpels; bear semblance to more ordinary household tools. Other instruments, including retractors, speculums and suction tools; are atypical in their design. All, however, share certain mechanical properties which ensure their effectiveness, safety and sustainability in a medical setting.
Medical equipment needs to feature superior strength, light-ness, corrosion-resistance and PH neutrality. To achieve this, manufacturers tend towards using certain metals; such as surgical steel, titanium, tantalum, platinium and palladium; which are able to meet these demands to varying degrees.
As greater innovation enters the medical equipment industry, such as automated laboratory equipment, manufacturers are asking more of materials. Surface treatments are now able to enhance key properties to improve material performance, so they function to cater for more sophisticated types of equipment. Much of this equipment needs to exhibit wear, corrosion and thermal resistance; while conforming to the high standards necessary for medical application.
Wear resistance
Different types of steel are often used to manufacture strength in surgical instruments, as is Titanium. This is not only due to the inherent strength of these metals, but also their relatively low cost and due to the fact that they are easily machined, welded, hot or cold-worked.
The metals are, in this way, very versalite; in that they can be easily fabricated into various shapes despite their strength. Titanium has the highest strength to weight ratio of any known metal, so it is often used to make medical instruments which need to be tensile while remaining very lightweight.
The application of these types of metals in medical equipment, however, does have its limitations. Nowadays, with automated medical devices, metals need to have improved mechanical properties that are not only strong in the moment, but wear resistant to the repetitive demands of automated tasks.
Also true, is that medical equipment manufacturers don't share the economies of scale enjoyed by other industries; so expensive resources, such as metals, need to last longer.
Innovative new collaborative robots, or ‘cobots’ are tasked with dealing with repetitive demands; such as the handling and sorting of blood samples for analysis, maintaining patient hygiene, or even performing back massages on patients.
Alloys need to be highly resistant to the types of wear caused by repetitive movement, regardless of how lightweight or compact they need to be. Commonly used metals, such as titanium, tend to exhibit poor fretting and wear resistance even when sliding against softer material.
With the right type of surface treatment, however, light alloys can be made tough to extreme wear caused by a combination of repetitive movement and tensile forces. For aluminium parts, it is possible to treat surfaces with hard anodizing. This creates an oxide layer on the metal which gives it about half the hardness of glass.
Hard anodizing, however, doesn’t provide the wear resistance necessary to withstand the repetitive friction and strain many medical applications are forced to withstand.
With a surface technology like plasma electrolytic oxidation (PEO), you are able to enhance metals so they have twice the hardness of glass. This is made possible by submerging the metal substrates in an alkaline electrolyte bath composition and then applying volts, which oxidises the surface, creating plasma discharges which form across the coating.
Due to the plasma discharges, crystallites of high hardness are formed in the coating, offering an attractive combination of high hardness and low stiffness – perfect for high fracture toughness, high adhesion and, therefore, wear resistant metal for medical application.
In one application, the coating was used to strengthen an aluminium part where glass slides would be placed, aligned and removed 1.4million times during the instruments 7 year lifetime.
Corrosion resistance
Medical equipment must also be tough to corrosion. In medical settings, health and safety requirements are notoriously rigorous and demand that medical applications are frequently sterilised using strong chemical solutions.
For medical implements, medical grade steel is often used due to is anti-corrosion properties - a property largely afforded by the addition of chromium.
In laboratories, however, the equipment has to be resistant to a larger variety of chemicals. Tantalum, a metal often thought of for its highly corrosion-resistant properties, is resistant to corrosive attack by acids and liquid metals and is therefore often used to make components inside laboratory equipment.
However, tantalum is expensive, and innovations in laboratory equipment mean different metals now have to deal with multiple chemicals at more frequent intervals.
Increased automation in laboratories means surfaces - used for chemical sorting and testing devices - come into contact with a mixture of acids, peroxides and hydrocarbons intermittently, every single day.
To weather this consistent chemical interaction, metals need to be protected using advanced surface treatment technologies.
With the use of PEO technology, metals can be made more corrosion resistant. It’s inert ceramic structure provides excellent natural chemical stability and corrosion protection.
To further enhance corrosion-resistance, you are able to apply a polyester powder coat to the porous PEO layer - this effectively fills the porous microstructure created during the formation of the PEO layer. To find out more about how PEO surface treatments can be sealed to offer comprehensive corrosion protection, read our article on sealers.
With added corrosion protection, metal can weather frequent contact with corrosive substances for much, much longer than without; making PEO treatment a perfect solution for specialist lab equipment.
Thermal management
Specialist lab equipment is often-times used to perform tasks that requires metal to transfer heat.
In one application developed by Keronite, a coating was created for a metal plate which transfers heat to a glass slide (up to 100C). The metal is exposed to elevated temperatures everyday, and with automated machines, there is no let-up - the metal has to deal with daily heat exposure for years. In the case of stainers, it has to deal with elevated heat temperatures while also maintaining mechanical properties - such as corrosion and wear resistance.
With the use of PEO technology, specialist coatings can enhance metals to perform thermal transmission (up to 900C), without elevated heat temperature impacting other vital properties.
As automation becomes more ubiquitous in the medical equipment industry - within which metals often need to handle corrosive substances, deal with heat transfers and weather the storm of repetitive action - this type of surface treatment technology will become increasingly sought.
PEO for life science machinery
Automated equipment is expensive, it needs to work and it needs to last. Metals often relied upon in the medical and chemical industries - such as steel, titanium and aluminium - cannot perform with the longevity or rigour necessitated by the automated equipment industry.
When it comes to building machines that need to be relied upon, often to save lives, only the most effective surface treatment technology will do. PEO is proven to significantly enhance properties in metal; including its wear, corrosion and thermal resistance, more so than any other surface treatment and all at once.
From a material performance perspective, lab equipment is notorious for having to cope with multiple requirements, which makes PEO treatment a perfect coating solution. To find out more about how PEO technology can be used to enhance performance in automated equipment, please get in touch with a materials scientist at Keronite with details about your project.
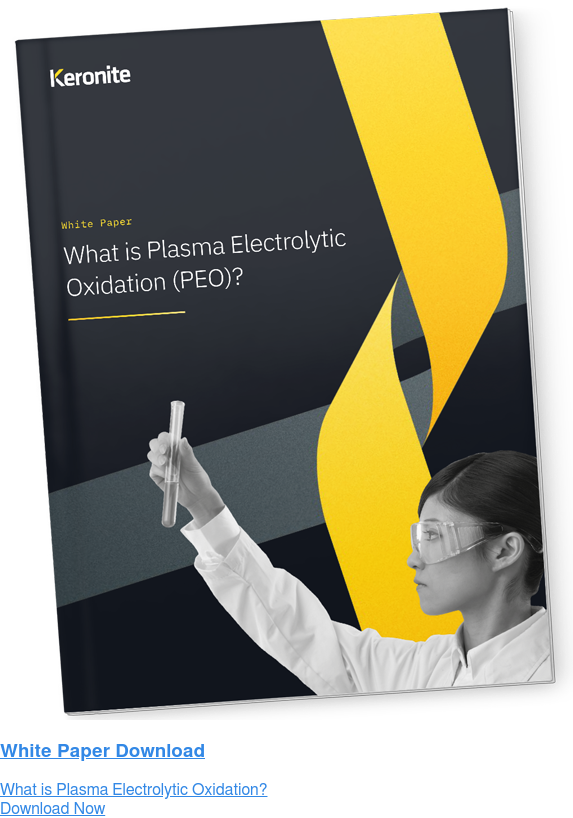
