Extending the life of aluminium tooling
29 December 2020As businesses and consumers demand higher quality products at lower costs and with smaller carbon footprints, manufacturers are responding with more efficient production processes. This means optimising efficiency and finding operating and energy cost savings over a production plant and process lifecycle.
Aluminium tooling parts are an essential component in the process engineer’s industrial manufacturing design toolkit. Because of its physical and chemical properties, such as strength-to-weight ratio, friction-coefficient, ductility, stiffness and chemical activity, aluminium and its alloys make ideal tooling parts for many processes.
However, although it has inherent properties making it ideal for many applications, there are production processes that are extremely hostile to any metal, including aluminium. Components can be damaged by high temperature corrosive liquids, abrasive raw materials and temperature extremes.
Furthermore, some manufacturing processes, such as those for food and beverage products, electronics or pharmaceuticals, have additional requirements. These can include a need for anti-microbial properties, hydrophobic properties, thermal barriers or even insulating properties.
Surface coatings produce the ideal tooling parts performance
Process engineers and materials scientists can extend the performance characteristics of aluminium tooling parts by adding surface coatings. And the right surface coating can be customised to deliver the target performance characteristics, overcoming the factors that negatively impact aluminium’s suitability for tooling parts.
The common challenges engineers face when specifying aluminium tooling parts:
- Substrate adhesion – as wear is a major cause of tooling failure, particularly in high-speed manufacturing applications, surface coatings used to improve wear resistance must have high levels of adhesion to the substrate to be effective. Furthermore, some techniques that use high temperature plasma sprays can oxidise the substrate, compromising the strength of the coating adhesion
- Coating coverage – complex tooling components have complex geometry, with sharp angles in the tool shape that can lead to coverage gaps when vapour and spray-deposition technologies are used.
Plasma electrolytic oxidation (PEO) is a surface coating technology that both meets the above challenges and can be further customised according to the specific tooling requirements. PEO enables process engineers to specify aluminium tooling parts for its core performance characteristics and simply add those it does not have.
For example, although aluminium is naturally corrosion and wear resistant because it forms a ceramic-like layer of aluminium oxide when exposed to air, it will suffer from corrosion and wear in a high-speed production process. A PEO coating provides the wear and corrosion resistance enabling it to perform for much longer periods without damage.
How can PEO coatings protect aluminium tooling parts?
PEO uses an electrolyte bath and plasma to form a duplex coating on aluminium and its alloys. The top level of the coating is formed from the aluminium substrate and is highly porous as a result of the plasma discharge during the formation process. Its performance characteristics can be customised by varying the components of the electrolytic bath, which become part of the outermost layer during the coating process.
Unlike spray-type coating technologies, because the tooling component is completely immersed in the electrolyte bath, the entire surface receives the same level of coverage so there are no gaps and weak spots resulting from complex geometry. The inner layer, a ceramic-like aluminium oxide layer, is also formed from the substrate. With PEO, the surface coating is part of the substrate, not an additional layer of another material. As a result, the adhesion concerns of other surface coating technologies are not relevant.
Creating a bespoke surface coating can result in the following enhancements to aluminium tooling parts:
- Applying a high-sliding wear resistant PEO coating improve hardness and as a result the tooling wear resistance is significantly enhanced
- Using polymers, such as PEEK (poly-ether-ether-ketone), in the outer layer introduces a built-in lubricant coating that reduces friction and wear
- Introducing insulating dielectric characteristics can be achieved by finely controlling the thickness of the PEO coating, which can be achieved by tailoring the deposition process. The aluminium oxide layer can be thickened to achieve dielectric strengths of 59-79 kV/mm
- A reduction in thermal conductivity can be achieved by adding silicates to the electrolyte bath, which generates a mullite-rich coating that acts as a Thermal barrier coating (TBC), protecting components that are used in high temperature and high speed applications
- Corrosion resistance is improved by adding PEO coatings with chemically inert ceramic-like properties, and thickening the aluminium oxide layers by adjusting the PEO process to provide the desired level of resistance. Hydrophobic properties also increase corrosion resistance – see below
- ‘Salting’ the PEO electrolyte with zinc and a sodium/tungsten oxide introduces anti-microbial properties, making components particularly suitable for healthcare and food and beverage processes by reducing or eliminating the need for regular anti-microbial washes
- Increasing the hydrophobic properties of the component’s surface can increase corrosion resistance by preventing liquid droplets and contaminants adhering to components such as nozzles and sprays, particularly when the liquid is hot and corrosive.
PEO can both extend the life of aluminium tooling parts, by better protecting them from their operating environment, and enable PEO coated aluminium to be used where uncoated aluminium would not be suitable.
To learn more about PEO, download our white paper ‘What is Plasma Electrolytic Oxidation?’ or get in touch with one of our materials scientists today.
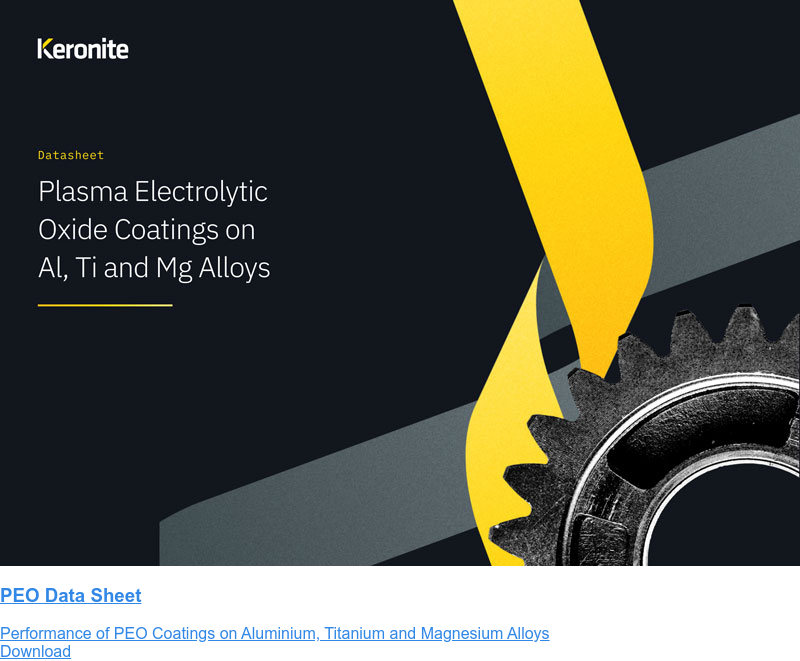
