Surface coatings for industrial tooling wear resistance
20 January 2022Society, and the industries that serve it, is constantly demanding higher performance and precision products to be delivered at a lower financial and environmental cost. As a result, industrial processes and tooling are constantly under pressure to be more efficient, sustainable and provide a greater return on investment (ROI).
This challenges engineers to design industrial processes with tooling that lasts longer, breaks down less often, is more productive and at the same time as consuming fewer resources, such as energy. To do that, the tooling components might need to be lighter, have greater wear and corrosion resistance, and high strength to weight ratio.
Without light alloys using aluminium, magnesium and other light metals, with the unique performance characteristics they offer, engineers would have limited options, mostly based around steel tooling components.
However, creating tooling from light alloys provides the material’s characteristics and resulting performance characteristics that steel cannot match. Light alloys can then be further customised to the specific tooling requirements by using surface coating solutions.
Boosting industrial tooling performance
Industrial tooling used in manufacturing processes suffers almost every imaginable stress during its operational life, including abrasion, exposure to corrosive chemicals, extreme temperature variation, high volume wear electrical and magnetic fields, electromagnetic radiation. If not optimised to withstand operational stresses, components fail, resulting in damage and downtime. This costs money.
Some materials, such as steel or ceramics, may have the necessary performance characteristics, but are heavy, and so consume more energy during operation, or require regular cleaning, or a lubricant or an antibacterial wash and so on. This all adds to the complexity of the process, meaning more things can go wrong, and the expense because consumables cost money (and can also have environmental costs).
Light metals such as aluminium, magnesium and titanium have excellent strength to weight ratios, as well as other features. However, in their pure state, as is the case in most alloys, they are typically vulnerable to chemical attack, wear easily or have low stiffness. Not ideal tooling components, therefore - until you add surface coatings.
Plating and conversion coatings for industrial tooling
The combination of light alloy components and bespoke surface coatings increases the service life of tooling while reducing the failure rate, downtime and resource consumption, resulting in higher productivity and, ultimately, a more profitable and sustainable process delivering a higher ROI.
Light alloy tooling coating solutions that adapt performance characteristics, such as sliding wear resistance, include:
Electroplating
The process of electroplating, or electrodeposition, plates one metal over the surface of another by using an electric current. The metal is plated, so the substrate sits in an electrolyte bath of a metal salt. The electric current reduces the metal cations in the bath, so a thin layer is deposited on the substrate.
The advantage of electroplating is that it is a relatively lower cost solution suitable for low-performance applications, such as moulds and dies. However, other solutions provide greater hardness and therefore greater wear resistance.
Nitriding
Introducing nitrogen into the surface of a metal provides a protective layer, improving wear resistance. Common nitriding techniques include salt baths, gas nitriding and ion nitriding. The protective layer is hard, slender in form and is grown by thermochemically introducing nitrogen to the outer surface.
Nitriding does not provide the hardness required for high performance tooling but is a good value solution for low volume processes, such as stamping.
Plasma spray coatings
A powder coating is melted using an argon-nitrogen-hydrogen-helium flame. The melt is sprayed onto the alloy, bonding firmly to the substrate on cooling. It is differentiated from other surface coatings as the substrate is not chemically changed by the process.
Furthermore, it is relatively low temperature, which can reduce/avoid damage to the alloy and so have less impact on the mechanical properties of the tooling component. However, the process is also more complex and expensive than most coating solutions.
Plasma electrolytic oxidation
This is a technique also known as micro-arc oxidation (MAO) and spark discharge anodising. The light metal alloy tooling component is placed in an electrolyte bath. An electric current is then passed through the bath. As a result, a double layered oxide coating develops on the light alloy substrate. The top layer is porous and the bottom is impervious. The electrolyte also becomes part of the coating, which is further modified by a plasma discharge.
A key advantage of PEO is the control engineers have over the coating and its characteristics. By altering the electrolyte composition, voltage, electrical regime and component fixture, the coating’s characteristics can differ. This enables engineers to create bespoke-to-application coatings that provide the light alloy tooling components with the right performance characteristics for the application.
Key factors to consider when choosing the tooling coating
Choosing the right coating for a tooling component can impact on the resulting whole-life performance of the production asset. For this reason, selecting the right material and a coating as one holistic decision is always likely to produce better results.
Factors such as the function of the tool, its position in the line/plant, the operating conditions, as well as a host of others, will drive the material and coating selection. A robot’s end of arm tooling’s performance characteristics within a clean-room environment will differ hugely from an aluminium loom in a textile factory. But there is a need for light alloys with the right surface coatings in both.
Advanced surface coating technologies that reduce wear are adaptable. Plasma electrolytic oxide coatings are created over three distinctive stages, each of which creates opportunities to uniquely adjust the processing parameters to create bespoke coatings for the precise needs of the tooling application.
You can learn more about plasma electrolytic oxidation in our free white paper, or, if you are interested in exploring the capabilities of the technique to improve your tooling design, contact us today.
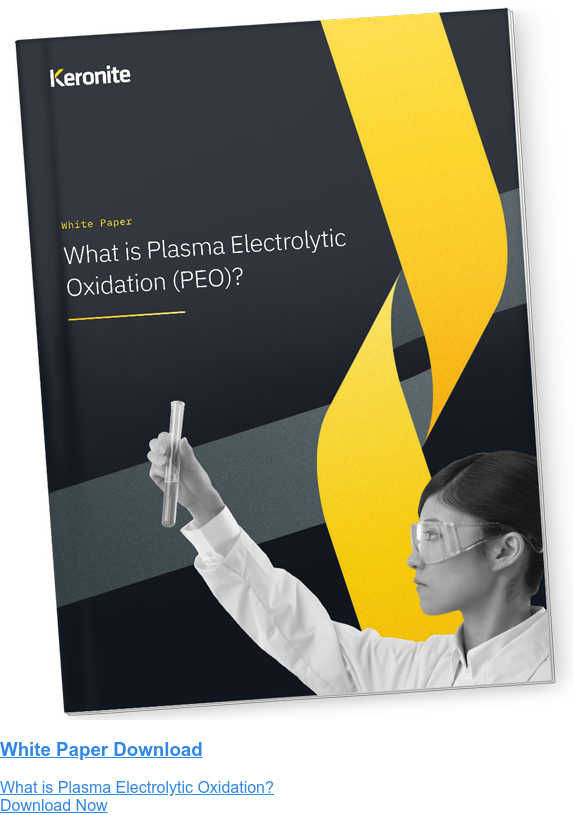
