Drones, magnesium and flying taxis: the materials science behind the world’s first VTOLs
2 March 2023Carbon emissions continue to be a worrying consequence of modern living, with the atmosphere currently holding 40.2 Gt CO2. The automotive and transport industry is a significant contributor to this global footprint, accounting for 7.7 GT CO2 after an 8% growth from 2022.
As engineers seek ways to improve fuel efficiency and reduce emissions, congestion in urban areas has become a known culprit for the needless emissions via transportation; Londoners spend a record 156 hours a year stuck in traffic, closely followed by Chicago IL at 155.
Alternative forms of transportation that circumvent congestion are usually found underground in tubes and subways, but now designers are looking to the skies with VTOLs. But what exactly are VTOLs, and what are the materials challenges involved in utilising them as a modern form of transport?
VTOLS - the 3D form of transportation
Vertical take-off and landing (VTOL) aircrafts, as their name suggests, can become airborne without the need of a runway. Examples of VTOLs are often found in military applications for their ability to function in urban environments, from traditional helicopters to the Harrier family of jets. It is this urban functionality that makes VTOLs an avenue of transportation engineering to transform travel from restrictive 2D to the freedom of 3D.
Joby represents the future of urban travel via an airborne ridesharing service. It is an electrically powered VTOL aircraft that operates completely within aviation sound guidelines via its quiet electric multirotors. Users will be able to travel at a range of 150 miles at speeds of under 200mph, free of the congestion found below. Not only does Joby optimise journeys and reduce the number of vehicles on roads, but exhibits zero emissions to reinforce its potential for sustainable travel.
What materials challenges hinder the launch of VTOLs?
Electric VTOLs such as Joby have the potential to cause significant change in the direction of environmentally friendly travel. That said, there are various challenges that have hindered its widespread adoption in relation to materials science:
Strength vs weight - Propulsion power sized electrical system necessitates lightweight components; In order for electric VTOLs to travel at the required distances and speeds to be applicable in urban environments, components need to be lightweight. Subversly, they also demand tensile strength to carry passengers and heavy motors, creating a challenge of balancing the two. Plastics have been a considered solution, but are nonconducting and transparent to EMI (electromagnetic interference and RFI (radiofrequency interference), which can potentially interfere with important internal components.
Corrosion & wear - In the particular case of Joby, its electric multirotors exhibit moving parts that provide its VTOL capabilities. These moving components often become susceptible to abrasive wear in long-term use, as well as corrosion from extreme weather conditions at high altitudes. As a result, these components demand resistances from both of these elements whilst maintaining the balance of strength and weight as previously mentioned.
Magnesium and surface coating - the solution to VTOL aviation
Magnesium in of itself is the world’s lightest metal that also exhibits an impressive strength-to-weight ratio, making it an attractive choice for the lightweight demands of VTOLs. It also has impressive vibration-dampening capabilities caused by high mobility dislocations in the metal, helping to provide a smooth journey for passengers. That said, standard magnesium lacks the proper wear and corrosion resistance to be used for VTOL components.
Magnesium alloys, on the other hand, can provide the light metal with additional strength and hardness, even extreme cases of both in some recent examples. There are also surface coating methods that can protect the metal from corrosion such as anodising, but can still lack the tensile strength required for demanding VTOL components.
Keronite - material science that pushes the boundaries
Magnesium has the potential to help launch commercial VTOLs via its unique lightweight properties, and in turn help push sustainability into the transport industry. That said, the light metal needs help from modern materials science, and advanced surface coating in particular.
Keronite’s unique Plasma Electrolytic Oxidation (PEO) coating process provides light metals with the key resistances they need to be introduced to harsh and demanding environments. Magnesium components are placed into a controlled electrolyte bath where plasma discharges create a porous ceramic coating. This coating not only provides impressive strength, hardness and resistance, but offers duplex capabilities via introducing specific regents into the porous layer.
In the case of VTOLs, PEO can provide engineers with components that are resistant to corrosion and wear whilst having usable tensile strength and weight. PEO represents modern materials science that is pushing the boundaries of modern engineering. Contact us or download our whitepaper below to find out how to become a part of it.
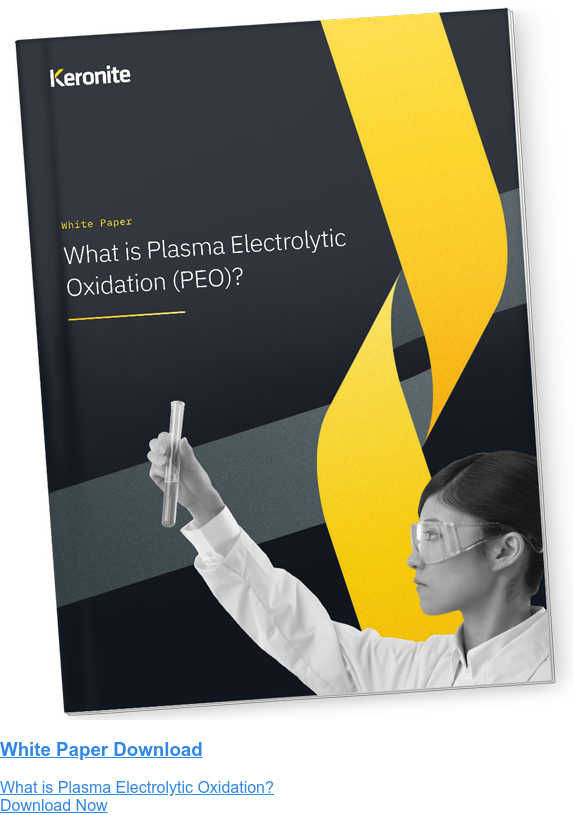
