An in-depth look at plasma electrolytic oxidation technology
28 July 2022Surface coating technologies have been developed for a century, extending the lifespan of components and enabling new materials to be used in established designs. In recent years, a revolutionary technology with customisable properties is leading the industry of coating technology; plasma electrolytic oxidation (PEO).
Keronite has developed and established PEO as a sustainable and superior surface coating technique since 2000; but what exactly is PEO, and why is it so significant?
What is plasma electrolytic oxidation?
Plasma electrolytic oxidation (PEO) is an advanced surface coating technology that provides extreme resistance to various corrosion, temperature and wear related elements. The process involves an electrolyte bath with a high voltage current that creates plasma discharges on the substrate’s surface, creating a layer of ceramic. PEO is a consistent and effective form of surface coating, allowing the full protection of complex geometries.
The part that separates PEO from similar forms of bath-based coatings like anodising is the plasma modification used. Plasma is used to alter the microstructure of the coating during the process, resulting in no-through-thickness cracks that are often seen in conventional anodising, as well as providing benefits of corrosion resistance and fatigue strength. This part of the process also creates a porous outer layer to the coating, enabling certain additives to be introduced to the coating that uniquely enhances its performance.
The idea behind PEO
PEO was first observed by Soviet scientists in the USSR during the early 1970s. What began as a highly unpredictable and energy consuming process evolved into the potential of wear resistance coatings by the mid 1980s. PEO was introduced into the Mir space station, but the technology was mostly untouched afterwards due to its unpredictability and demands on energy.
In 2000, early Keronite engineers saw the potential of PEO that could be harnessed to provide a new world of available metals to designers. They developed and refined the makeup of the electrolyte solution, the precise time of exposure to current, and the electrical regime employed. All of these factors made the process of PEO better understood, enabling a full range of available coating characteristics. As a result, Keronite has been able to enhance light metals such as aluminium and magnesium alloys, providing designers with a new perspective on component materials.
PEO and bespoke coating capabilities
Keronite has since further developed the PEO process with a team of advanced engineers, chemists and scientists leading its development. As a result, PEO has become a bespoke coating method through the customisability it offers in the process. The outer ceramic layer of PEO is porous, which allows for specific duplex coatings to be introduced during the process to enhance various resistances. For example, micro and nano-crystals such as Al202 corundum can be introduced into the ceramic layer of aluminium for enhanced hardness.
The versatility and tailor-made capabilities of PEO can be further enhanced by adjusting the parameters of the process and the metal alloys used; the resistance, porosity, conductivity and hardness can all be adjusted for an optimal lightweight solution. The customisability this offers designers presents revolutionary capabilities for long-lasting components that are lightweight, simple and cheap to manufacture.
Keronite as the pioneers of PEO
The surface coating technology of plasma electrolytic oxidation enabled the introduction of light alloys into components that were previously too weak to be sustainable. The technology has enabled vast developments across industries, as well as new opportunities for designers.
Keronite works directly with project teams and manufacturers to provide specific PEO solutions. What began in 2000 as an idea has now grown into a full scale industry, with Keronite getting AS9100 certification for PEO facilities and basing various PEO-dedicated technology centres. We have also invested over £1m in our US facilities to treble production capacity.
To find out more about the PEO process read our full whitepaper below.
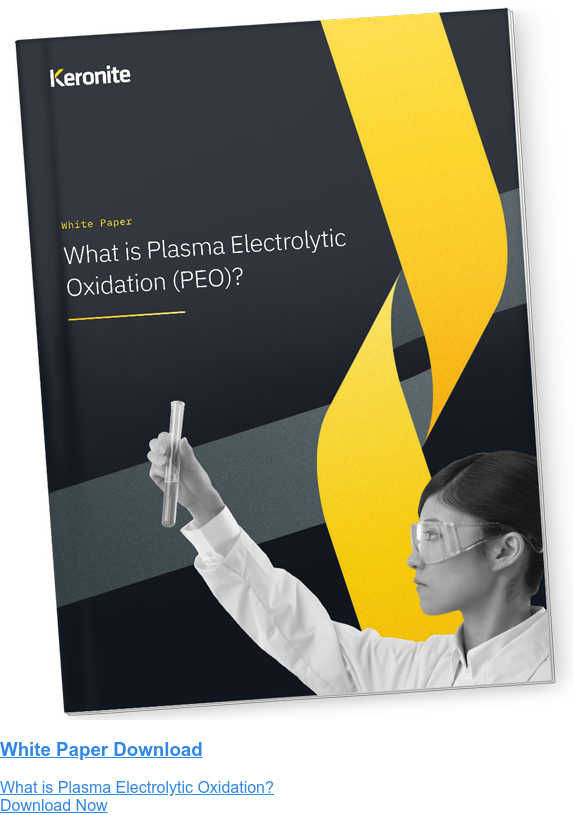
