Preventing light alloy corrosion in extreme environments
20 October 2022Light alloys such as magnesium, aluminium and titanium are increasingly replacing steel alloys across many different industries. These metals are characterised by being lightweight, yet strong. Titanium, in particular, naturally provides high levels of corrosion resistance, hence its popularity in many offshore, oil and gas, and marine applications.
Corrosion, however, still continues to present a challenge, particularly in highly corrosive environments. The presence of seawater, brackish water, and other chemical environments accelerates the corrosion process. Furthermore, other application-specific demands, such as friction, high temperatures or high pressures, can make components even more susceptible.
What modes of corrosion are most common in extreme environments?
The degradation caused by corrosion is not limited to ferrous metals. Light metals and their alloys are also susceptible to corrosion, which can be the formation of metal oxides, hydroxides, carbonates, or sulphides on the metal’s surface. The environment and exposure to external conditions play a key role in the rate of metal corrosion.
Corrosion science is a complex field as there are many types and mechanisms for corrosion. Some corrosion, such as uniform corrosion, occurs mainly at the surface and, although it presents a poor aesthetic, is unlikely to be detrimental to the structure and function of the component. Other types of corrosion, such as crevice corrosion and pitting corrosion, can be intense and localised, rapidly causing significant damage that can lead to equipment failure.
Many different environmental conditions can affect the rate and type of corrosion of light metals. Each metal and their alloy reacts with air and moisture from their surroundings to form oxides. The oxides that form on the metal’s surface are usually passive and will protect the underlying substrate from further corrosion.
Aluminium and magnesium alloys are particularly sensitive to variations in pH. Pollutants in the air, naturally occurring salts and added chemicals can alter the pH of a given environment. Acidic conditions significantly increase the rate of corrosion for light metals, and steps must be taken to protect the integrity of the metal substrate. Titanium, however, typically exhibits lower corrosion rates, due to the stable oxide film it forms.
Exposure to air and moisture at any concentration will eventually lead to corrosion. High-temperature, high-pressure and high-humidity environments accelerate the rate of light metal corrosion. As will the presence of salts and other chemicals in the air. Tests such as salt spray tests seek to replicate these conditions, testing the corrosion resistance of materials – providing a quantifiable measure of corrosion resistance.
Marine, offshore and subsea environments often create extreme corrosion conditions, but these conditions can equally form within industrial manufacturing environments. Each application and its corrosion environment is unique, and careful consideration should be given to the specific set of conditions that a metal component is exposed to when in use.
The role of surface coatings
Surface treatments are essential to protect light alloy metals from corrosion. This can increase the lifespan of metal components, while enabling engineers to take advantage of the desirable properties of light metal alloys. Surface coatings protect components from corrosion and wear and can be used to modify surface properties such as hardness and surface roughness. Performance coatings are designed to prevent corrosion by creating a passive layer to prevent air and moisture coming into contact with the metal substrate. These can include conversion coatings, paints, and powder coatings.
PEO: a versatile coating for light alloys
Plasma Electrolytic Oxidation (PEO) is an innovative coating suitable for a range of metal substrates: aluminium, magnesium, titanium, valve metals and beryllium alloys. PEO offers a high-quality, corrosion resistant finish (2,000 plus hours in salt spray testing) with no pre-cleaning required and a quick processing time. These coatings also demonstrate excellent wear resistance, strong adhesion to the metal substrate and thermal resistance.
PEO coatings are applied by submerging the component in an electrolyte bath and passing a high voltage current through the metal. The properties of the coating can be altered by changing the electrolyte composition and processing conditions. Temperature, applied voltage sequence, current density and application time can influence porosity and coating thickness.
For enhanced corrosion resistance in extreme environments, PEO coatings can be combined with subsequent coatings. For example, a polyester-based powder coating could be applied over a PEO layer on a magnesium alloy substrate to improve corrosion and scratch resistance. The porosity and microstructure of the PEO layer can be adapted to optimise adhesion between this coating and the secondary powder coat layer to maximise coating performance.
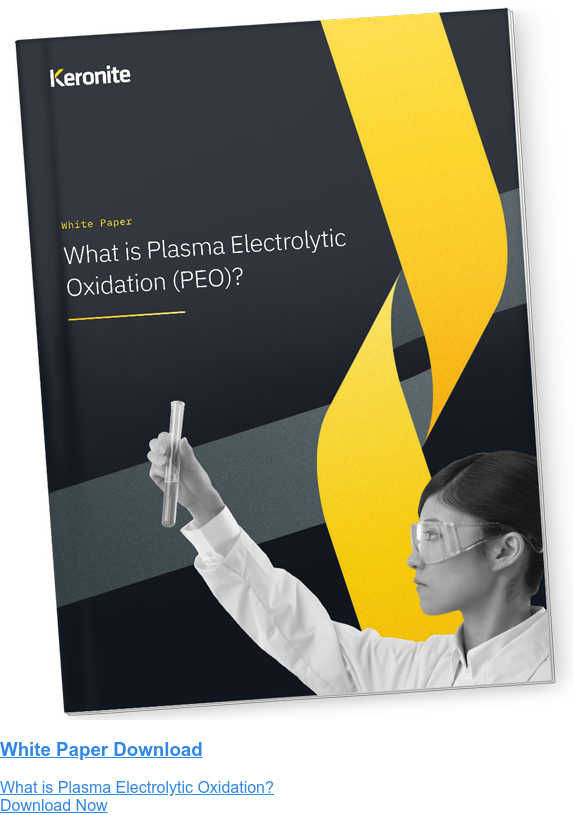
