Automating high speed packaging processes with light alloys
18 December 2020To meet the demands of consumers and just-in-time supply chains, packaging machinery operates at ultra-high speeds. A single high-volume production line can produce 20 million single use contact lenses a year. A mid-range tea bag machine produces 420 bags per minute. That is seven bags a second, almost faster than the human eye can see.
Speed is not the only requirement of modern packaging processes, tea bags and contact lenses are delicate, requiring precise and gentle handling. For fast-moving consumer goods, it is a margin game. Packaging machinery that works fast, effectively and efficiently is critical for their margins.
That is why light metal alloys are becoming the favoured materials of high-speed packaging machinery. They are able to offer a combination of properties and performance characteristics enabling higher speed and more robust packaging processes. They represent the ideal choice for high-speed packaging machinery makers, and their extensive supply chain of component and tooling manufacturers.
How can light alloys accelerate high-speed packaging?
Complex gears, pulleys, servos, wheels, cogs, lugs, spools, reels, tubes, in-feeds, feeders, nozzles, levers, jaws, magazines, fasteners and the hundreds of other components in high speed packaging machinery and robotics require highly specific properties and performance characteristics. There is a wealth of choice in terms of materials including steel alloys, ceramics, composites, plastics, light metal alloys, textiles and even natural fibres.
However, it is light alloys, such as aluminium, that feature many of the properties needed for high-performance components in an ultra-high-speed packaging line. Light metal alloys have mechanical and physical properties such as high strength-to-weight ratios, low specific gravity, malleability, ductility and machinability, along with non-magnetic and thermal conduction properties that make them ideal as machinery components. They may also have desirable chemical properties such as corrosion resistance and be non-toxic in solid form.
Component materials such as steel and ceramics may have most of the necessary performance characteristics, but are heavy, and so consume more energy during high speed operation. They may require regular cleaning, lubrication and disinfecting and so on. These measures introduce additional complexities into an already highly complex machine, so component failure is more likely.
The unique combination of properties offered by light metals enable engineers to design packaging machinery that can operate at extremely high speeds and process hundreds, or even thousands, of units a minute, with greater reliability.
Packaging machinery component operational stresses
Virtually every consumer product found in homes today has been manufactured or processed by a primary, secondary or end-of-line packaging machine. These include food and beverages, healthcare, pharmaceutical and medical, electronics/electricals, textiles and clothing and FMCG (fast-moving-consumer-goods), not forgetting the range of B2B products.
This vast array of products will include every known property and operational environment that could have a negative impact on or damage components in contact with the product and/or the packaging. The eventual result could be component failure, resulting in the line stopping and halting production. This can have a significant financial cost, alongside impacting on just-in-time supply chains and reputational damage.
Just some of the operational challenges faced by packaging machinery components include:
- Abrasion and adhesion, resulting in wear and sliding wear
- Corrosion by exposure to products, such as foodstuffs and lens saline, and packing processes such as hot glues and lubricants
- High operating temperatures and steam, and in some environments, very low temperatures
- Pressure differentials
- Dust and powders
In addition, in sectors such as food, pharmaceutical and electrical parts, there must be zero or near zero material loss from surfaces during operation – no flaking or chipping and high wear resistance.
Protecting light alloy components with tailored surface coatings
Imagine the challenge facing an engineer who is creating a primary packaging machine for filling single serve sauce pots. The sauce is corrosive and abrasive and must be created in a hygienic food safe environment and the pot lids are heat sealed. What component materials have chemically inert, wear resistance, antimicrobial and heat resistant properties?
Sauce pots are low margin high volume consumables, so high production speeds, minimal line downtime, low energy consumption and long service life are additional challenges. What materials offer the best combination of cost, reliability and strength to weight ratio?
No single material, not even light metal alloys, can meet all these requirements. However, customising the component material’s performance characteristics by using surface coatings is a viable solution. Specifically, plasma electrolytic oxidation (PEO) is a surface coating technology enabling engineers to customise the solution’s performance criteria.
PEO uses an electrolyte bath and plasma to form a multi-layer coating on light metal alloy components. The surface of the coating is porous and, uniquely, the PEO process enables components of the electrolytic bath to be incorporated into the composition of the surface coating. Machinery components can be produced, and their properties tailored to order by the component manufacturer.
- Component wear resistance can significantly improve, through using high-sliding wear resistant PEO coating to improve hardness.
- Introducing polymers, such as PEEK (poly-ether-ether-ketone) in the top coating builds in lubrication, reducing friction and wear, which means a potentially hazardous / contaminating lubricant is not required.
- Introducing silicates to the electrolyte creates a coating that reduces the thermal conductivity, adding a thermal barrier coating (TBC).
- Corrosion resistance is improved by PEO coatings with ceramic-like chemically inert properties that resist chemical attack. The coatings can reduce and virtually eliminate surface material loss preventing contaminants from the machinery entering the product.
- Anti-microbial properties can be introduced in healthcare and food and beverage processes that reduce or eliminate the need for regular antimicrobial washes, by doping the PEO electrolyte with zinc and a sodium/tungsten oxide.
PEO provides high speed packaging machinery component suppliers and machinery design engineers with a range of solutions to some of their most demanding challenges.
To learn more about PEO, download our white paper ‘What is Plasma Electrolytic Oxidation?’ or get in touch with one of our materials scientists today.
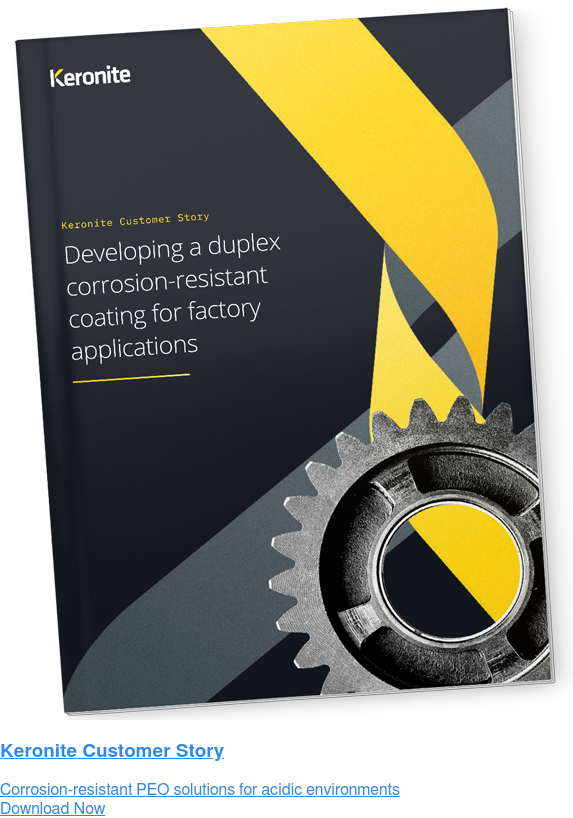
