What is the microstructure of magnesium and how does it affect performance?
5 January 2023Magnesium is now commonly described as the metal of the future thanks to its impressive lightweight features and strong material structure. Magnesium cast alloys have a high strength-to-weight ratio, a product of its unique microstructure.
What is the microstructure of magnesium?
The microstructure of cast magnesium alloys is a hexagonal, close-packed (HCP) crystalline structure that provides the metal’s properties of strength and stiffness at a surprisingly low weight. However, it exhibits a weak coverage of the outer oxide layer that protects most metals from ambient corrosion, sometimes even forming a porous film that leaves the substrate unprotected. This microstructure also suffers from poor formability at room temperature, which is the amount a component can be deformed before it is damaged.
What causes corrosion in magnesium?
Magnesium is a highly reactive metal. It is in group 2 of the periodic table, meaning it has two valence electrons in its outer shell at an atomic level. Group 2 elements are highly reactive as these electrons easily combine to other elements. Additionally, magnesium also has a low electronegativity of 1.3; the lower an element’s electronegativity, the easier it is for them to lose an electron to another element in a chemical reaction. Other metals like aluminium and zinc have electronegativities between 1.6-1.7 in comparison, which is why it is often alloyed with them.
Corrosion is a chemical reaction in which a metal reacts with oxygen or/and water to form oxide, hydroxide and sulphide substances after losing its electrons, which then leads to a reduction in the metal as a result. Due to the highly reactive nature of magnesium, the energy required to lose its valence electrons is available in typical ambient conditions. Most metals have a natural outer oxide layer that can defend them from this level of corrosion, but magnesium’s is particularly weak after studying its microstructure. As a result, magnesium can corrode extremely easily in normal conditions when compared to most other metals; though this can be a feature in certain applications that require degradation at a desired rate, such as osseointegration.
Corrosion prevention techniques (coating, plating, etc.)
Thermal spray coatings - Thermal spray coatings are the projection of heated, small softened particles onto a metal’s substrate where they adhere and form a protective coating. This simple coating process provides resistance to elements such as wear, corrosion and heat to the outer layer of the metal. However, thick coatings are difficult to achieve through thermal spray coatings, and can have a negative effect on the plastic deformation of magnesium’s microstructure.
Electroplating - Electroplating is the method of coating a metal’s surface with a chosen material through using an electrolyte bath and electrical current. For magnesium, electroplating is used to coat it with other metals like zinc, copper and nickel to protect components from corrosion. A major drawback of electroplating is the amount of hazardous waste it produces that can be dangerous for the environment.
Anodising - Anodising is a similar process to electroplating using an electrolyte bath and electrical current, but instead forms a thick oxide layer on the metal’s surface. This helps improve the surface properties of the metal by thickening its natural oxide layer; for magnesium, anodising improves corrosion resistance and hardness. That said, anodising has trouble coating complex geometries and surfaces, often resulting in cracks that reduce the fatigue strength of the component.
Role of materials science in enabling the use of magnesium
Advanced material science is needed to efficiently incorporate wrought and cast magnesium into designs without negatively affecting its microstructure. Moreover, the environmental impact of certain forms of metal coating can have consequences when used in mass production.
Fortunately, plasma electrolytic oxidation (PEO) ticks all the boxes for effective microstructure protection, full coating and adhesion to the substrate, and zero harmful waste products.
PEO uses an electrolyte solution and electrical current to create plasma discharges on the metal’s surface, creating an outer ceramic coating. The coating is consistent and provides protection against corrosion, heat, wear, and much more. Better yet, the electrolyte solution is chemically benign and consists of 99% distilled water, making it completely safe to dispose of normally.
Download our whitepaper to find out more about how PEO can enhance corrosion and wear resistance of magnesium, and broaden the scope of magnesium-based components.
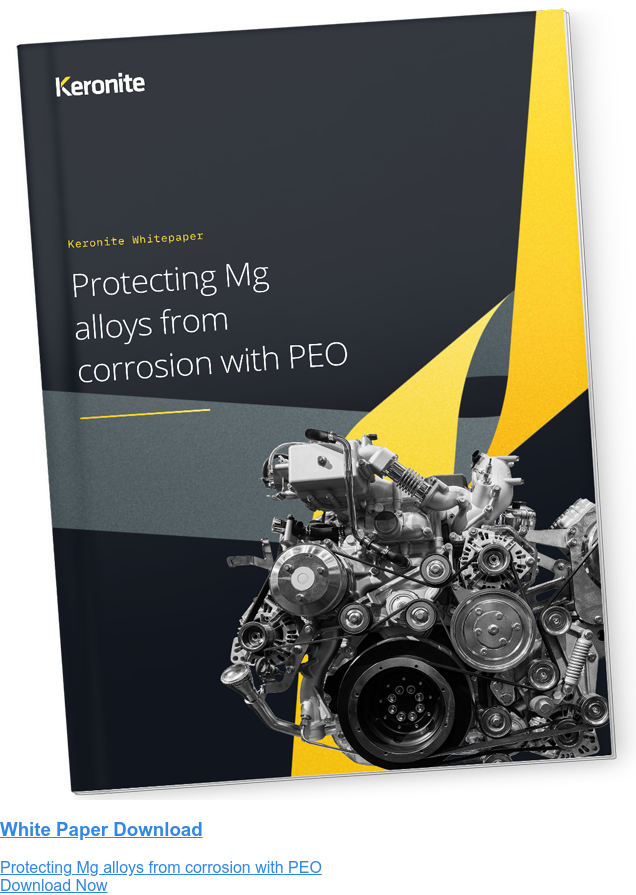
