Increasing the lifespan of light alloys: why and how
29 March 2021Global pressures are instigating a host of innovation in materials technologies supporting light alloys. This is resulting in far greater material choices for engineers, especially as the rules of material compatibility are being rewritten. For example, some of the challenges that prevented the use of aluminium, magnesium and titanium are much easier to overcome. But in the toughest of operating environments, just how well can these materials perform compared to their heavier counterparts?
Who, for example, would specify a soft metal such as aluminium as a loom arm in a high-speed textile mill, surely it would quickly wear away and fail? But advanced surface coatings technologies provide wear resistance, enabling aluminium to be used in many applications that the metal or alloy alone could not survive.
Multiple advances in metallurgy and materials chemistry have led to new alloys and surface coatings that have significantly expanded the applications and extended the life of light metal alloys
In tough environments, light alloys are now capable of providing equivalent or, in some instances, improved performance over heavier metals such as steel. Technologies such as plasma electrolytic oxidation (PEO) uniquely improves the performance of materials like aluminium, titanium and magnesium, which enables their use in tougher applications.
Common reasons why light metals and their alloys fail
Despite their excellent strength to weight ratio and many other favourable characteristics, the light metals and their alloys are not without their flaws. Some common reasons why the life of aluminium, magnesium and titanium products and components can be shortened include:
Corrosion – despite their natural oxide coatings, all three major light metals and certain of their alloys can be easily corroded in harsh environments.
Hardness and wear – both magnesium and aluminium are relatively soft materials, as is titanium, when compared with steels and ceramics. Abrasion and adhesion cause material loss that leads to failure.
Thermal breakdown – magnesium and aluminium alloy melting points are relatively low, typically up to 670 degrees centigrade. This restricts the applications of uncoated alloys.
Fatigue – aluminium does not have a fatigue limit, so when subjected to regular loading will crack and fail. Magnesium and titanium do have fatigue limits, which vary widely according to the type of alloy.
Stiffness – when used in structures and components, magnesium and aluminium are considerably less stiff than steel and titanium is half as stiff.
Cost – although not strictly a property, one of the reasons titanium is not used more widely is because of cost. Many processes that improve titanium’s performance are expensive.
How to extend the life of light metals and their alloys
Corrosion, wear and fatigue can all contribute to the early failure of components and solutions created from light metals and their alloys. However, there are multiple strategies that can address these weaknesses. These include:
Alloying: at a very basic level, pure aluminium is mostly used for cabling, in packaging and foil; similarly, pure magnesium is rarely used in high performance applications. Both metals are typically alloyed with a range of agents including each other, copper, zinc, calcium, manganese and other substances. These result in a range of performance improvements that can include greater strength and fatigue resistance, corrosion resistance, hardness and heat resistance.
Titanium is alloyed with a wide range of metals that include aluminium, manganese, iron, chromium, cobalt, nickel, and copper and also valve and rare earth metals such as molybdenum, vanadium, niobium, tantalum and zirconium. These result in a huge range of performance improvements which, if the metal and its alloys were not so expensive, would result in titanium being used in many more applications.
Thermal mechanical surface treatments / heat treatments: the properties of light metal alloys can be enhanced by heat treatment, rapid heating and cooling, and simultaneous heat and mechanical treatments, such as hot rolling. These treatments change the crystalline structure and internal stresses of the metals in the alloy in various ways. The results include improved thermal barrier properties, increased hardness, greater strength, changes in elasticity, ductility and stiffness and improved fatigue resistance.
Most temperature mechanical treatments involve heat, but there are specialist cryo-rolling treatments applied at minus 190 degrees centigrade to aluminium alloys that create an ultra-fine-grained structure that results in high strength and ductility with improved corrosion resistance.
Mechanical surface treatments: techniques include hammering, deep-rolling, roller burnishing / polishing, blasting and shot-peening of cold aluminium and titanium alloys, resulting in greater fatigue resistance. The treatments induce compressive stresses that can extend the life of the alloy. They can also remove minor structural faults in the metal’s surface.
Surface coatings: there are a wide range of surface coating technologies. At a basic level, these include paints, powders and polymer coatings, alongside roll-to-roll coatings. Electro-plating, anodising, chemical and physical vapour deposition, thermal plasma sprays and plasma electrolytic oxidation (PEO) are all examples of coating technologies.
Depending on the coating used, the benefits can include thermal barrier coatings (TBCs), hard surfaces or lubricants to reduce wear, corrosion protection and improving stiffness. More flexible and sophisticated techniques, such as PEO which has a unique duplex coating with a porous outer layer, can be used to provide multiple benefits.
The most effective combination of the above life extending strategies will depend on the specific application, and which of the light metals, aluminium, magnesium or titanium, is used. For example, a high strength aluminium alloy with a PEO coating that provides greater wear and thermal resistance could be the optimal solution for extending the life of a helicopter gearbox component. However, an alternative approach may best suit a magnesium damper arm engine mount.
To learn more about how PEO surface coating technology can extend the life of light metals, download our white paper ‘What is Plasma Electrolytic Oxidation?’ or get in touch with one of our materials scientists today.
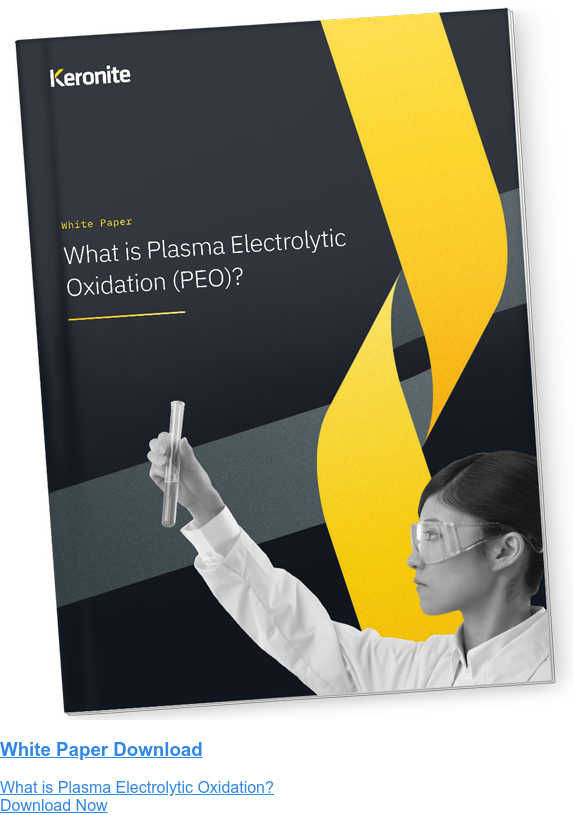
