How innovative surface technologies are supporting new challenges in oil and gas
25 May 2021Over the last four decades, the profile of oil and gas reserves has changed beyond recognition, introducing new and significant challenges across the industry value chain, including upstream, midstream and downstream.
The result has been huge advances in supply chain solutions and innovative technologies. Light metals, with their unique properties, are playing an increasing role in meeting these challenges and underpinning the new technologies.
The unconventional revolution, introducing onshore shales and tar sands alongside offshore fields going into deeper and colder waters and greater drilling depths, present complex operational parameters, including higher pressures and higher temperatures (HPHT).
Developing economically viable oil and gas prospects in these new uncharted territories, at a competitive cost and an acceptable risk level, is one of the most significant engineering challenges ever faced by the industry. And this is a sector that is not afraid of complex challenges.
New industry priorities demand fresh approaches to materials selection
Global changes in production and supply, plus operating in more demanding environments, such as corrosive HPHT wells, has led to a shift in priority. The lifespan of assets and improving operational efficiencies is now high on the agenda, according to reports.
One way to preserve assets for longer, and improve operational efficiencies is to select materials that are capable of withstanding the challenges of producing unconventional and HPHT reserves.
Advances in surface coating technologies are enabling material scientists and engineers to choose light metals such as aluminium, magnesium, titanium and the valve metals that have unique properties, but which have previously been unfeasible in these situations.
The challenges of material selection for oil and gas applications
The total annual cost of corrosion in the oil and gas production industry is estimated to be $1.372 billion, according to a NACE study. That figure can be broken down into $589 million on surface pipeline and facility costs; $463 million annually in downhole tubing expenses; and another $320 million in capital expenditures related to corrosion.
Environmentally assisted cracking and localised corrosion are the two primary forms of degradation that affect the steel and light metal alloys typically used for upstream production applications. Especially those considered HPHT, Arctic or sour. Sour fields are defined by their measurable amounts of hydrogen sulphide.
There are many corrosion challenges to overcome in the up-, mid- and downstream, such as acid-bearing fluids, sulphur and hydrogen sulphide present in crude oil, seawater and HPHT environments like oil processing plants which can reach 600°C. For the supply chain, manufacturing components and subsystems that can withstand these chemically and physically hostile environments are critical to the industry maintaining production.
Anti-corrosion technologies such as specialist surface coatings allow the use of light metals in a greater range of applications within the oil and gas supply chain, enabling engineering solutions to benefit from their highly beneficial characteristics.
The manufacturing landscape of the oil and gas supply chain
The oil and gas industry’s unique structure is supported by a complex and highly specialist supply chain, including networks of SMEs working in each area, manufacturing components and subassemblies that can withstand conditions relevant to that market segment.
Upstream
Manufacturers serving the upstream are responsible for systems designed for on and offshore platforms such as manifolds, plus components for undersea drilling and the extraction and storage of chemicals, like pipes and containers. The assembly of “Christmas trees”, comprising valves, casing, spools and fittings used to regulate the flow of oil and gas is also an important manufacturing process upstream.
Midstream
Pipelines, Pigs, pump stations, tank trucks, ships capable of transporting hazardous materials and transcontinental tankers are all crucial parts of the midstream. The supply chain in the midstream requires production of components capable of withstanding corrosion and delivering the toughness required for asset longevity.
Downstream
The downstream is responsible for converting crude oil and natural gas into usable fuels and finished products. Manufacturers working in the downstream select materials suitable for components such as crackers, pipelines and pipework, welds, fasteners and corrosion resistant monitoring and sensor equipment.
At every stage of the oil and gas industry, components used typically need to be able to withstand extreme environments over the long term, while still offering the most efficient use of weight and materials.
The benefits of light alloys for components and subsystems in the oil and gas market
Light metals and their alloys offer a range of qualities well suited to the needs of the oil and gas supply chain, and their role in this sector is increasing. Their impressive strength-to-weight ratio, high toughness and improved fatigue life are desirable qualities, but often the full potential of these metals cannot be realised because of poor corrosion resistance.
For manufacturers supplying the up- mid- and downstream oil and gas supply chain, selecting metals which are capable of withstanding the high salt loads of brine water, the presence of hydrogen sulphide and carbon-dioxide in the operating media and aerobic and anaerobic components in both the extracted products and the environment is of primary concern.
Materials specified must also be lightweight and offer an inherent strength and toughness for high-weight applications. These include the engineering of isolated stationary or floating offshore platforms weighing as much as 300,000 tonnes or downhole and sea-floor equipment that can weigh 2,000 tonnes.
The favourable properties of titanium
Light metals such as titanium are favoured because they are highly resistant to seawater, carbon dioxide and hydrogen sulphide corrosion. Titanium also maintains its strength at temperatures as low as -240°F, which is a common temperature used to liquify natural gas. Titanium is often used in heat exchanger tubing in liquified natural gas plants and in the linings of the pressurised vessels in LNG tankers. It is also widely specified for deep-water drilling riser production, casing tubes, seawater pumps and liquid separators.
The favourable properties of aluminium and aluminium-magnesium alloys
The high strength-to-weight ratio of aluminium alloys can reduce the weight of drilling equipment, making it easier to transport.
Aluminium and aluminium-magnesium alloys AMg2, AMg3, Amg5 and AMg6 offer high resistance to crude oil and some types of gasolines. AMg2 is commonly used in the manufacture of containers, towers, refrigerators at oil refineries and condenser applications.
Resolving corrosion issues to broaden the use of light metals
Light metals, such as titanium, aluminium and magnesium have been popular in the engineering of components and sub-systems for the oil and gas sector for some time, but their application has been limited because of their low tolerance to corrosion and wear.
Components constructed from light metals such as titanium, magnesium and aluminium operating in highly corrosive environments will rapidly degrade if not protected. There are several traditional and conventional protection options, such as paints and powder coats, or spray-based plasma coatings, but it is likely that these solutions may not be able to provide the level of protection required in the intense conditions of the oil and gas industry.
Specifying surface coatings to broaden the use of light metals in oil and gas
Plasma electrolytic oxidation (PEO) is a unique and advanced technology that can be tailored to meet the specific corrosion challenges of the oil and gas industry.
PEO uses an electrolyte bath and plasma over three distinct stages, to form a ceramic-like duplex coating. The process can be adjusted at each stage to create customised coatings for the exact needs of oil and gas applications.
The coating is formed from the substrate and the contents of the bath, and is not a separate additional layer, such as a plasma or thermal spray coating or paint, which means there are no bonding issues. With a highly porous top layer, the contents of the electrolytic bath can be incorporated into the surface coating to provide additional properties alongside corrosion protection, including:
- A high-sliding wear resistant PEO coating to improve hardness
- Improved lubrication to reduce friction and wear using polymers, such as PEEK (poly-ether-ether-ketone)
- Reduced thermal conductivity by adding silicates to the electrolyte bath, to act as a thermal barrier coating (TBC)
- Improved hydrophobic properties to increase corrosion resistance by preventing liquid droplets and contaminants adhering to parts.
This advanced surface treatment is allowing engineers in the oil and gas market to fully realise the potential of light metals in applications which were previously considered too corrosive.
To find out more about PEO, download our white paper ‘What is Plasma Electrolytic Oxidation?’ or get in touch with one of our materials scientists today.
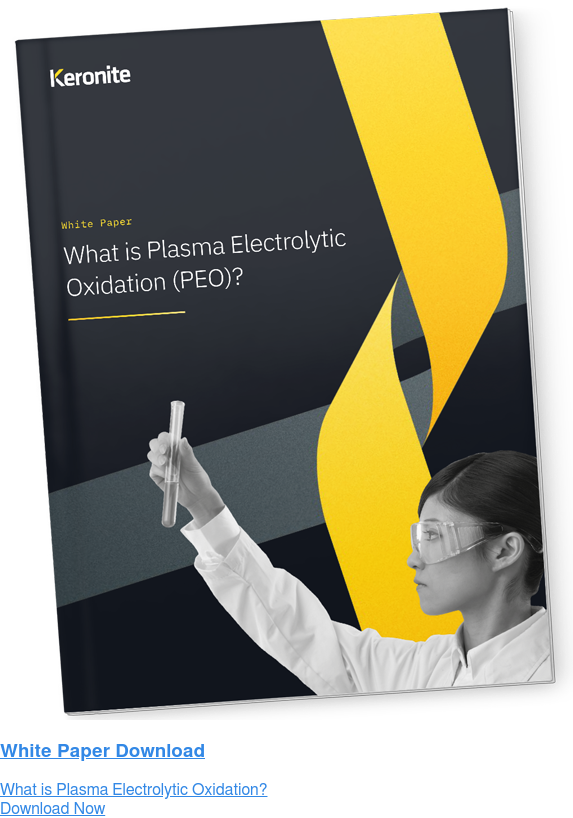
