Extending the service life of rotating industrial machinery
24 November 2020Rotating manufacturing machinery is highly prevalent in almost all forms of manufacturing – from the steam turbines and electric motors, to the pumps and actuators. While this equipment is extremely common, there remains significant opportunities to increase throughput, reduce downtime and increase the life of rotating components.
High-speed, high-voltage rotating components in machinery are often subject to cyclic, dynamic loads and vibrations that result in unpredictable multiaxial stresses. Due to these stresses, materials scientists have sought to understand the characteristics and relationship between coatings and materials to find opportunities to improve their performance.
Although there are more challenges than just wear. Chemical stresses are common in food and beverage, healthcare and pharmaceutical industries, even textiles and petrochemicals offer these challenges. All in all, that means materials must face friction, vibration, high temperatures, wear, abrasion and even corrosion. Under these extreme conditions, though, new surface technologies are offering solutions to boost performance.
Aluminium innovation
Historically, steel is preferred by materials engineers designing components for these tough manufacturing applications. However, over the last two decades, the emergence of high performing aluminium alloys have enabled them to effectively replace steel. This would not have been possible without innovations in advanced surface technologies that uniquely improve the performance of aluminium in these environments.
Manufacturing plant design and process engineers choose component materials based on a range of criteria. As well as physical and chemical properties, such as strength-to-weight ratios, friction-coefficient, ductility, stiffness, chemical activity, wettability, immune response, dielectric properties and heat coefficients, the sums – cost, lifespan and service intervals – are often the key decision criteria.
In industrial applications, General Electric’s pioneering value engineering approach has become the de-facto approach to selecting materials. Put simply: it’s the sums that are pointing more engineers to aluminium alloys over steel. While steel is typically lower cost, and aluminium alloys therefore require greater investment, the lifespan advantages they can achieve over the long term trumps the smaller initial investment.
Increasing manufacturing yields and efficiency
The major advances in aluminium coating technologies are enabling the creation of components that last longer, operate under more intensive environments and can be more easily repaired.
From a pure financial assessment, coated aluminium components last longer, do not require replacement as frequently, do not require quite as regular service intervals. Additionally, as aluminium is lighter than steel, they require less power, use less energy and are not as likely to fail unpredictably.
All these factors make manufacturing processes more efficient and sustainable, impacting on the final manufacturing and environmental costs, the profitability of the product being manufactured and overall return on investment (ROI).
Aluminium’s performance in high speed manufacturing applications
Rotating machinery components face unique challenges in high-speed manufacturing applications. In addition to the multiaxial stresses, rotating parts are subject to:
- Fatigue arises from the cyclic multiaxial dynamic stresses the rotating component suffers during normal operation. Microscale structural damage is the first sign of fatigue, which progresses into cracks that grow to eventually cause failure.
- Wear from abrasion and adhesion; there is wear caused by abrasive manufacturing raw materials such as fibres and webbing. Long-term wear occurs from high throughput – the sheer volume and speed of production.
- Temperature extremes that include both high operating temperatures through high speed processes, or the process itself uses high temperature gasses, liquids or raw materials, such as in food and beverage, textile and petrochemical production. The process may also feature extreme temperature fluctuations that can cause microstructural defects, leading to cracking, plasticity and failure.
- Corrosion caused by anything from hot glue guns through corrosive textile dyes and lubricants to everyday food and beverage ingredients; this can strip the ceramic oxide layer from a light metal alloy exposing the underlying metal to further chemical attack. Furthermore, the unique combination of corrosion and multiaxial dynamic stresses causes stress corrosion cracking in unprotected aluminium alloy components.
- Embrittlement from contact with high temperature liquids and water saturated air, resulting in microstructural defects and plasticity that can cause the component to fail mechanically.
The effects of the above can have a dramatic impact on the efficiency of a production line. Rotating component life is reduced and the risk of failure increased unless the components are treated with suitable surface coatings.
How PEO surface coatings enhance rotating components
Plasma electrolytic oxidation (PEO) is a surface coating technique with multiple advantages. It uses an electrolyte bath and plasma to form a duplex coating on light alloys. The top level of the coating has high porosity and, uniquely, PEO enables the composition of the surface coating to incorporate components of the electrolytic bath as well as the substrate. Customising the PEO surface coating can enhance rotating components in the following ways:
- Tooling wear resistance is improved, through using high-sliding wear resistant PEO coating to improve hardness
- Lubrication can be introduced, which reduces friction and wear, by using polymers, such as PEEK (poly-ether-ether-ketone) in the top coating
- Thermal barrier coatings (TBCs) can be added by introducing silicates to the electrolyte to produce a mullite-rich coating that reduces the thermal conductivity
- Corrosion resistance can be enhanced through PEO coatings with ceramic-like chemically inert properties that resist chemical attack
- Anti-microbial properties can be introduced in healthcare and food and beverage processes that reduce or eliminate the need for regular antimicrobial washes, by doping the PEO electrolyte with zinc and a sodium/tungsten oxide.
PEO can not only extend the life of rotating components, but also enhance their utility by introducing new characteristics, such as the anti-microbial element and lubricant.
To learn more about PEO, download our white paper ‘What is Plasma Electrolytic Oxidation?’ or get in touch with one of our materials scientists today.
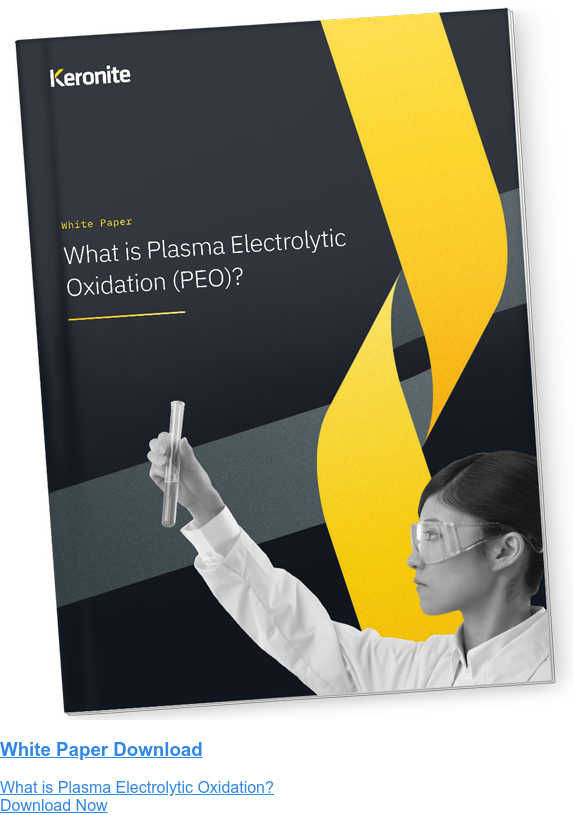
