Could surface coatings revolutionise additive manufacturing?
4 February 2021Faced with challenges such as creating highly intricate parts in low volumes, engineers are increasingly turning to additive manufacturing as a production and prototyping solution. The advances in 3D printing technologies have facilitated this transition.
It was plastics that led the 3D printing revolution, but now additive manufacturing uses materials such as plastics, paper, ceramics and glass, a whole range of metals and even concrete. That enables engineers and materials scientists to gain all the benefits that light metals such as aluminium and titanium usually offer, alongside the benefits of 3D printing.
But once created, complex additively manufactured light metal parts face the same challenges as forged, cast, stamped, milled and machined materials. Factors such as wear, corrosion, temperature, hygiene, immune response, wettability, dielectric properties continue to create challenges for engineers and materials scientists.
Just because the highly complex aluminium alloy component intended for an attack helicopter gearbox, or the titanium implant with a specific surgical geometry have been created by additive manufacturing does not mean they are immune to wear, corrosion or bio-incompatibility. In fact, the additive manufacturing process can worsen some of these characteristics, such as wear resistance.
The good news for engineers who want to use the winning combination of light metals and their alloys and additive manufacturing is that there is a surface coating technology, plasma electrolytic oxidation, that works just as well on 3D printed parts.
What are the benefits of additive manufacturing?
The fundamental difference of additive manufacturing when compared to nearly all other production techniques is that it builds a part layer by layer, rather than taking a block of material or blank and shaping it to the desired configuration by removing material.
The shape and geometry are limited only by the additive manufacturing process and material. With the huge advances in 3D printing technologies, the limit is now more often that of the designer, because intricate shapes are now possible in a huge range of materials.
This means the approach is ideal for rapid prototyping, one-of-a-kind or very low volume production and for creating components as a single piece that may have previously required multiple sub-components.
It can also be used to build legacy parts where the tooling is no longer available. Not only does 3D printing create the obvious time saving benefits – it can also improve quality, strength and reduce costs. Significant value improvements and cost savings can be made through reducing wastage for high value and complex high parts using expensive materials.
How additive technology uses light metals to overcome new challenges
One of the many strengths of additive manufacturing is that the process can create highly complex geometrical shapes from light metals and light metal alloys that conventional techniques find very difficult, uneconomical or just impossible. And it can do this rapidly and with little wastage, compared to conventional techniques.
This has generated a revolution in many high-performance sectors. Assemblies of multiple machined components can now be replaced by a single additively manufactured part, with strength, time and cost benefits. Additively manufacturing parts from light metals such as aluminium enables further weight reduction with minimal impact on performance, such as strength.
However, there are some material processing issues for most additive manufacturing technologies that require addressing. This means many 3D printed light metal alloy parts are not ready for final use until further work and finishing, such as machining, has been completed. These include:
- Porosity: caused by multiple factors, it can impact negatively on mechanical properties of the additively manufactured part. For example, the quality of powder feedstock can significantly influence porosity, or the atmosphere of the manufacturing process environment. Poor quality porous aluminium powder will be heated into porous laminations, as inert gases can become trapped during the manufacturing process. High porosity can reduce strength and cause component failure.
- Surface roughness: caused by multiple factors, including the thickness of the laminations. Wider laminations result in greater surface roughness above the 10-micron tolerances demanded by aerospace applications. However, processes with small laminations take longer and add cost to the process, so it can be a trade-off.
- Surface cavities and cracks: metal parts additively manufactured by melting can suffer from shrinkage, as the light metal alloy liquid cools to a solid. This can also cause delamination between layers.
- Localised oxidation: light metals such as aluminium oxidise easily in air. If the manufacturing process is not contained in a sealed chamber with inert gases, then oxidation can occur. This can cause delamination, as the layers cannot adhere, impacting on component strength.
Using PEO to finish and protect complex 3D printed parts
Some material processing issues can be easily addressed by adding a surface coating. Additively manufactured aluminium and titanium parts can be protected from corrosion and wear. The surface coating can also smooth the surface roughness, as an alternative to machining. And depending on the end application, the surface coating can change or eliminate porosity.
But not every surface coating is suitable. Many, such as thermal and plasma spraying, require pre-treatments. Furthermore, line of sight spray techniques deliver incomplete coverage of highly complex geometric shapes. This in turn leaves the untreated areas susceptible to wear and corrosion and exposes excessively porous and cracked surfaces.
Techniques such as powder coating lack the fine control needed for tolerances in the tens of microns range, which are basic requirements for precision high performance parts in sectors such as aerospace and defence, medical implants and electronics.
PEO uses an electrolyte bath and plasma that forms a multi-layered coating on additively manufactured parts made from aluminium and titanium and their alloys. The outer layer of the coating is formed from the substrate, the light metal or light metal alloy. It is porous, so the coating’s performance characteristics can be customised by varying the components of the electrolytic bath, which become part of the outermost layer during the coating process. This approach can deliver the following benefits:
- Applying a high-sliding wear resistant PEO coating improves hardness
- Using polymers, such as PEEK (poly-ether-ether-ketone), in the outer layer introduces a built-in lubricant coating that reduces friction and wear
- Introducing insulating dielectric characteristics can be achieved by finely controlling the thickness of the PEO coating, which can be achieved by tailoring the deposition process. The additively manufactured part’s oxide layer can be thickened to achieve dielectric strengths of 59-79 kV/mm
- A reduction in thermal conductivity can be achieved by adding silicates to the electrolyte bath, which generates a mullite-rich coating that acts as a Thermal barrier coating (TBC), protecting additively manufactured components that are used in high temperature and high speed applications
- Corrosion resistance is improved by adding PEO coatings with chemically inert ceramic-like properties and thickening the oxide layers by adjusting the PEO process to provide the desired level of resistance. Hydrophobic properties also increase corrosion resistance – see below
- ‘Salting’ the PEO electrolyte with zinc and a sodium/tungsten oxide introduces anti-microbial properties, making additively manufactured light metal parts particularly suitable for medical and dental applications
- Increasing the hydrophobic properties of the component’s surface can increase corrosion resistance by preventing liquid droplets and contaminants adhering to parts. Titanium alloy medical and dental implants benefit from improved osseointegration.
Unlike spray-type and powder coating technologies, because the part is completely immersed in the electrolyte bath, the entire surface receives the same level of coverage so there are no gaps and weak spots resulting from complex geometry.
The inner layer is a ceramic-like oxide - aluminium oxide or titanium oxide and is also formed from the substrate. This eliminates adhesion problems, as the entire surface coating is part of the substrate, not an additional layer of another material.
PEO’s unique technology not only eliminates the challenges associated with additively manufactured parts, such as surface roughness and cracks. It also enhances the characteristics of the part. This enables many more applications to benefit from additive manufacturing.
To learn more about PEO, download our white paper ‘What is Plasma Electrolytic Oxidation?’ or get in touch with one of our materials scientists today.
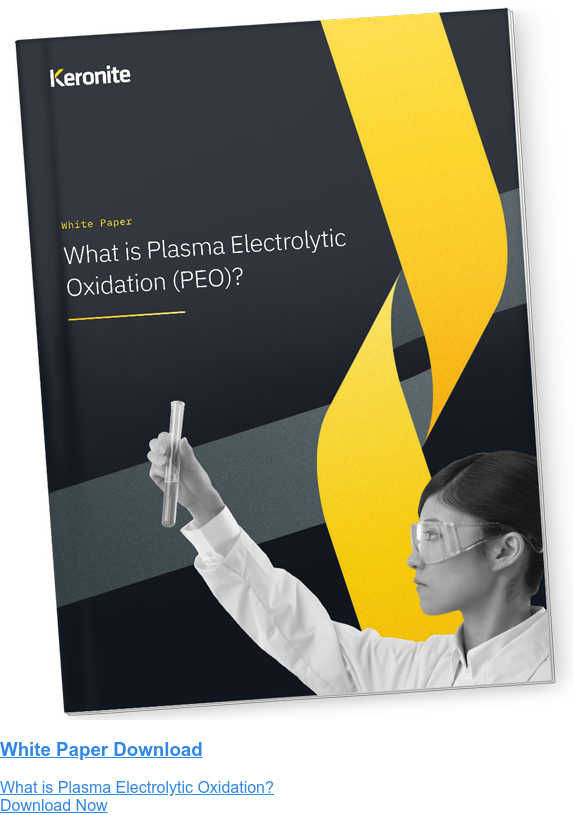
