Three key features of thermal spray coatings
3 April 2023Thermal spray coatings can extend the lifespan of components and enhance their performance to enable the use of lightweight alloys. The right spray coating method can increase wear resistance, improve corrosion performance, optimise high-temperature performance, all through a tailorable method that can produce highly controlled coatings for the end application.
The coating method: thermal spray coatings
The conventional thermal spray coating methodology
Thermal spray coatings are applied at high-temperatures and velocities to coat a substrate with molten droplets of a chosen coating solution. The droplets quickly flatten, cool and solidify on the component’s surface, creating a consistent layer of coating. Before spraying, the component’s substrate needs to be cleaned and roughened via a preparatory grit blasting process to improve the reliability of bonding and improve the surface adhesion of the coating. Depending on the specific method, varying temperatures, materials, and velocities will be used during spraying to achieve specific coating features;
Thermal Spray Coating |
Temperature (°C) |
Velocity (m/s) |
Plasma |
10,000-15,000 |
800 |
Arc |
5000 |
300 |
Flame |
3000 |
170 |
High Velocity Oxy-Fuel (HVOF) |
3000 |
1000 |
Suspension plasma spraying: advancing the art
Suspension plasma spraying (SPS) is a unique form of thermal spray coating that utilises extremely small particles to create nano-sized microstructures with specific properties. The particles used are too small to be applied through plasma thermal spraying, so they are suspended in a solution that also matches the required mechanical properties. The resultant coating exhibits complex microstructures that can be altered based on the suspension solution and features like temperature and velocity. The microstructures of suspension plasma spraying present a range of features depending on the composition. Porosity, density and resistance can all be adjusted to provide bespoke features that extend the lifespan of components.
The features of thermal spray coatings
Thermal spray coatings can be applied both by automated machines or by hand, and usually produce minimal distortion to the substrate. This makes them a suitable choice for light metals that are susceptible to wear and corrosion, and enable their use in a range of testing applications. Moreover, they can be inexpensive (depending on the method) and quick to deploy, when compared to alternative methods such as anodising and electroplating.
The protective layers produced via thermal spray range from 0.1-10 mm of thickness, and provide resistance to wear, corrosion, abrasion or heat depending on the methodology behind each solution:
Dense, hard-wearing, abrasion resistant deposition
Coating materials require sufficient kinetic energy to deform and bond on a substrate’s surface, hence the high velocity of thermal spray coatings. The greater the velocity of thermal spray coatings, the higher the density of the resulting protective layer. This dense and hard coating exhibits corrosion and abrasion resistant properties that can be tailored to meet the specific application.
Thermal resistance
Different coating materials require varying temperatures to effectively form a consistent and reliable coating on a substrate. The high temperatures of plasma and arc spray coatings enable the use of refractory materials such as oxides and high melting-point metals such as molybdenum. These methods provide abrasion and thermal resistance, alongside a range of others depending on the material.
Porosity and abradable applications
Various thermal spray coatings can exhibit a porous outer layer, such as with plasma spraying. In some applications, such as those facing extreme corrosion, this outer porous layer can reduce the useful life of a component’s substrate. However, this porosity can act as a lubricant reservoir for moving parts, providing effective wear and abrasive resistance where necessary. Additionally, additives such as polymers and graphite can be introduced to this porous outer layer to create an abradable coating; a surface which will intentionally abrade when making contact with another surface to increase conformance.
What are the applications of thermal spray coatings?
Automotive
To reduce the weight of designs for fuel efficiency and EV battery ranges, components such as engine blocks and other structural materials frequently consist of aluminium alloys. These alloys often exhibit poor tribological properties, and are prone to prolonged wear and thermal exposure.
Thermal spray coatings are utilised by automotive manufacturers to extend the lifespan of components whilst maintaining the efficiency of large volume production. Transmission parts such as synchronising rings and shift forks are widely coated via flame spraying, whereas piston rings are coated using plasma spraying.
Aerospace
In aircraft, the blade rotation path of turbine engines includes contact with shroud sections when in use. Without proper treatment, these blades can exhibit extreme abrasive deterioration that limits their lifespan and can breach aerospace standards.
Thermal spray coatings can be made abradable, enabling their use as a solution for the wear that takes place in gas turbine engines. The coating is applied to the interior-edge of the blade rotation path, intentionally wearing instead of the blades themselves. This improves the efficiency of the turbine engine by increasing the conformance between turbine and host material, extending the lifespan of the engine blades.
Industrial
Industrial environments, such as semiconductor manufacturing, exhibit a range of corrosive elements as well as extreme temperatures. These conditions not only shorten the lifespan of recruitment and demand regular maintenance, but puts operators at risk of harmful chemicals if a malfunction were to take place.
These industrial applications use thermal spray coating as a solution to regularly maintain the required surface properties of components and equipment. For semiconductor manufacture, HVOF and arc wire thermal spraying are used to provide a range of porous, thermal and corrosion resistant coatings for different components. This maintains efficiency of production by reducing the frequency of repairs and extending the lifespan of manufacturing equipment.
Bespoke-to-application, purpose-designed thermal spray coatings
The flexibility of application, configurable characteristics and inexpensive nature of thermal spray coatings makes it an attractive coating solution for a range of components. They play an integral role in extending the lifespan of components whilst maintaining performance in their respective applications. Keronite, now part of the thermal spray group at Curtiss-Wright Surface Technologies, are able to offer materials science expertise and create bespoke-to-application coatings that uniquely enhance plasma spray coatings for the needs of their customers.
Keronite’s materials scientists are actively pushing the boundaries of coating technology with innovative solutions. We provide the facilities and capability to provide thermal spraying for our customers quickly and cost-effectively. Moreover, our revolutionary Plasma Electrolytic Oxidation (PEO) coating technology can provide a duplex coating with over 30 different types of sealers to provide bespoke features for your application. To find out more about Keronite’s coating capabilities and how they can optimise your design, send an inquiry today or download our PEO whitepaper below.
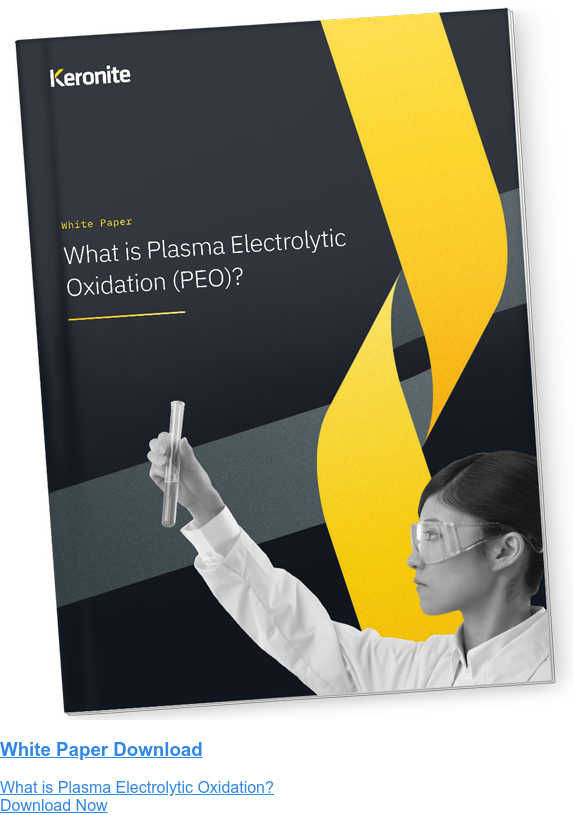
