A guide to spray coatings for light alloys
13 October 2022How spray coating techniques improve the performance of light alloys
Light alloys are the go-to option for engineers seeking materials with high strength-to-weight ratios. In industries that require more than high-strength, light alloys can also increase the efficiency of machinery, vehicles and planes by offering a lightweight alternative to materials like steel. But these produce another concern – component longevity. And this is where surface coatings become critical.
Spray coating options for light alloys
There are a number of potential surface coatings that offer solutions to many of the challenges facing light alloys. Each of these provide unique characteristics that can enhance the material in terms of its:
- Wear resistance and hardness.
- Corrosion and rust resistance.
- Dielectric breakdown strength.
- Thermal properties and heat sinking characteristics.
- Optical properties such as reflectivity and solar absorption.
Applying spray coatings offer an inexpensive route to making light alloys far more interesting propositions in strenuous applications. Engineers have the option of applying all sorts of sealers, not limited to:
- Ceramic sealers.
- Prismatic sealers.
- Epoxy coatings.
- Thermoplastic sealers.
- Non-stick sealers.
- Polyurethane
- ... and more
These sealers and coatings can be applied in combination with one another to create duplex coating solutions, or even applied with a conversion coating technology like plasma electrolytic oxidation (PEO) to further enhance their performance.
What are the benefits of spray coatings?
Spray coatings are capable of increasing the life of light alloys and other metals. They help increase the life of components, making materials perform better in their final applications. For instance, the following coatings have been widely used to enhance performance:
- Epoxy coatings have proven highly effective coatings for anti-corrosion applications.
- Powder coatings are capable of improving the wear resistance of light alloys.
- Electrophoretic coatings can improve the electrical resistance of components.
Whilst these improvements are clear, there are a number of considerations that should also be made whilst deciding upon a surface technology. Particularly in high-stress applications, there are a number of downsides, which other techniques may offer a solution for. These include:
- Adhesion strength. Typically, spray coatings exhibit lower adhesive strength than alternative coating techniques, such as conversion techniques.
- Application complexity. Some spray coating technologies require multiple steps to apply – such as cleaning, pretreatments and shot-blasting.
- Coating thickness. Spray coatings, due to the process methodology, are typically harder to control with regards to the resulting coating thickness. For applications requiring ultra-thin coatings, or high levels of precision, this is a necessary consideration.
- High defect rates. Without industry-leading equipment, spray coatings can produce high numbers of defects.
What are the best applications for spray coatings?
- Industrial - Machinery used for manufacturing applications face a continuous amount of abrasive and corrosive elements, resulting in regular maintenance in order to remain effective. Spray coating reduces the amount of maintenance required by providing abrasion and corrosive protection to components in a short process, reducing the frequency and overall cost of repairs.
- Aerospace and Defence - Different components on an aircraft experience a range of strenuous elements; turbine engine components face considerable thermal strain, landing gear needs to manage extreme pressure and weight, and the engine and fuel compartments need to be corrosive resistant. Spraying provides aerospace engineers with the versatility to coat each component with the relevant surface features and protections, minimising overall production time.
- Automotive - Bodies for automotive vehicles need to be aesthetically pleasant as well as resistant to corrosion. Spray coating sealers such as polyurethane provide sufficient corrosion resistance whilst enabling a range of colours and aesthetic finishes for designers. This both saves cost and provides versatility for design and engineering teams.
Thinking about a spray coating solution? Consult our materials scientists
Spray coatings pay an integral role in enabling materials in some of today’s advanced engineering applications. At Keronite, we’re helping engineers maximise the length of life and whilst actively reducing component weight.
Keronite applies over 30 different types of sealers to light alloys, catering to all needs and materials requirements, as well as relevant MIL specifications. We help deploy these coatings for our customers quickly and cost-effectively. We’ve used spray coatings to help our customers achieve:
- Corrosion resistance.
- Wear resistance.
- Reduced fatigue debit.
- Thermal control greater than 750°C
To get expert, no-obligation advice on spray coatings, their usage and fit for your project, get in touch with our materials science team. We’ll work with you to find a coating solution that works just as you need, when you need it.
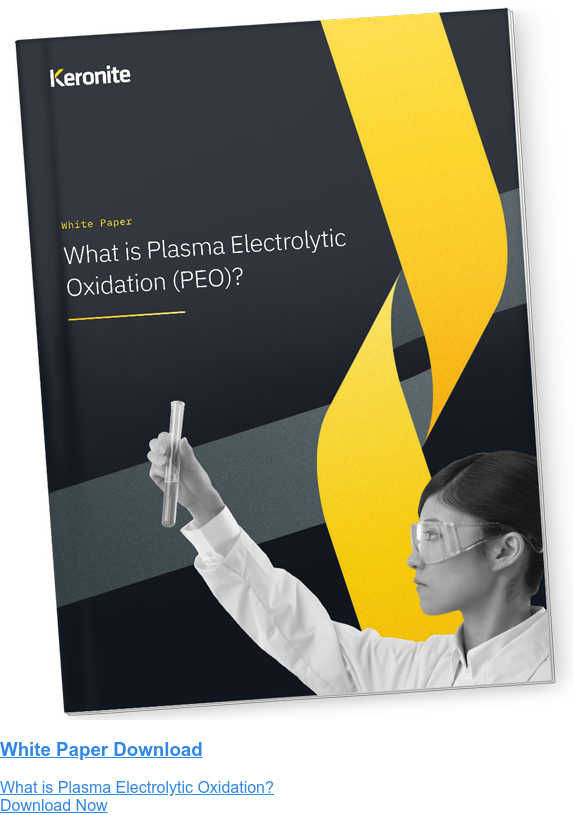
