The lightweight future of space design and material selection
8 June 2023Lightweight materials are critical in a future of low-cost, sustainable and reusable space travel. As the latest space race concludes, there’s a growing appetite to make space a cheaper place to access, as well as talk of a future Mars colonisation, where humans could settle in the future. But to make this dream a reality, the modes of space transport, haulage and missions need to be overhauled.
Materials, their properties and their weight play an important role. Heavier materials, while more reliable, increase the cost of a launch. Lighter materials, while cheaper to launch, do not necessarily meet the requirements of the harsh, intensive environment in space. They won’t last as long - light alloys are more prone to thermal effects, corrosion and mechanical failure.
Scientists are inventing new solutions to the most prevalent modes of failure to light alloys in space. In practice, it means that heavy materials can be replaced with lighter ones, yet perform just as well, and last just as long.
Some technologies, such as Keronite’s plasma electrolytic oxidation (PEO), even enable parts to be reprotected from their hostile environments. Read on to learn how the most prevalent materials used in space are changing, and how light alloys are making more adventurous projects possible.
Reinventing the space industry with lighter materials
The resurgence of the space industry has a lot to do with the influx of commercial, private companies entering the space market. Since 1989, there have been 432 licensed commercial space flights. To put this rapid growth into perspective, more than 15% of these were issued in 2021.
Now, more space missions and flights are taking place, and providers are keeping a close eye on the cost of a launch, with concerns over how much it costs to build, launch and land a rocket.
Source: https://www.faa.gov/data_research/commercial_space_data/
Beneficially, an increase in industry output means there are greater opportunities to achieve economies of scale. A recent Morgan Stanley industry report concludes that: “The cost to launch a satellite has declined to about $60 million, from $200 million, via reusable rockets, with a potential drop to as low as $5 million. And satellite mass production could decrease that cost from $500 million per satellite to $500,000.”
There are many areas in life where innovations in the space industry have led the way for the rest of the world. Artificial limbs, scratch-resistant glass, and even the materials in modern shoes all owe a great deal to innovations in the space industry. Materials science, once again, is creating new technologies specifically designed to improve the lifespan and performance of materials used in space, especially around composite materials and light alloys.
The new space race is about weight
One interesting measure prevalent in the industry is cost per kilo. This figure aggregates and averages the total cost of a satellite, rocket or any other form of spacecraft, dividing it by its weight. Put simply, a heavier vehicle costs more to launch and there is potentially more space waste (as different launch stage equipment is abandoned).
Most launches, according to the Center for Strategic and International Studies, fall within the $10,000-$20,000 cost per kilo range. This is expected to fall even more significantly with the market for small rockets and smaller payloads booming over the coming years. When combined with the influx of reusable launch systems and components, the cost per kilo could fall even further.
Light alloys, light weight, light payload
Light alloys may not be new to the space industry, but the technologies that enhance them are increasingly capable. Conversion coatings, such as plasma electrolytic oxidation (PEO), can provide corrosion protection, passive thermal control and reflectivity control that is required in space, in addition to:
- Protection from cold welding, fretting and physical impacts.
- Excellent adhesion to avoid particle generation, which can reduce the longevity of light alloys in space.
- Resistance to radiation in its many forms including AO, P+, E- and ultraviolet.
- Outgassing protection, tested by total mass loss (TML) and collected volatile condensable materials. The extreme conditions of Mercury require less than 0.1% of outgassing.
- Resistant to extreme temperatures and heat fluctuations. Materials need to cope with extreme temperatures of up to 450 °C and cryogenic temperatures as low as -185 °C.
- Corrosion resistance during time spent in storage. Protecting $2bn worth of work from corroding in cleanroom storage before launch.
To learn more about the advanced surface technologies used widely across the space industry, download ‘What is PEO?’, an introduction to Keronite’s proprietary surface coating and all the protective characteristics it provides.
For more information about how PEO could be used to enhance the performance of light alloys in your space project, get in touch with our technical team.
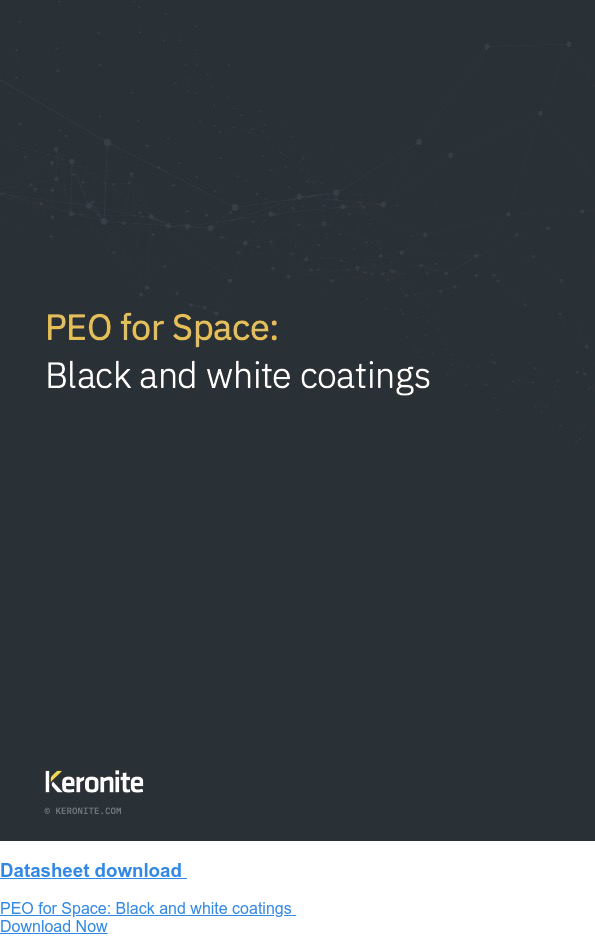
