White, reflective coatings for satellites and spacecraft
26 September 2019As the fiftieth anniversary of Apollo 11 reminds us, innovation in materials technologies have proven critical in space. They’ve long helped to protect on-board equipment, as well as satellites and spacecraft themselves; allowing for more ever more adventurous experiments to be undertaken.
Keronite has been involved with plenty of space missions over the years. In the recent European Space Agency (ESA) mission to Mercury, Keronite developed a brand new coating solution capable of improving the reflectivity of light alloys in space.
As the ambitions grow for deeper, and more frequent, space exploration, materials scientists are on the lookout for protective coatings that prevent vital equipment from damage. Read on to learn more about Keronite’s new coating technology that’s on the BepiColombo satellite, which is expected to reach Mercury in October 2025.
Facing the next frontier
Space poses clear problems for material engineers who must protect spacecraft from extreme conditions. Solar illumination, cryogenic temperatures and extreme radiation exposure are all capable of wreaking havoc on equipment travelling through space. The ESA’s engineers soon realised that BepiColombo would face a new challenge on its mission to monitor Mercury: 700°K (426°C) temperatures as it approached Mercury, the planet closest to the sun.
The ESA had its target in mind: to launch a satellite that would complete a comprehensive study of Mercury and its atmosphere. What they weren’t yet sure of was how to make that dream a reality. How could the observational equipment maintain full precision while experiencing the punishing conditions of space travel? Enter Keronite.
Interplanetary solutions
The ESA came to Keronite with targets already set. In order to guarantee the satellite could arrive at Mercury able to observe the planet with total accuracy, they needed a coating which offered:
- Protection from cold welding, fretting and physical impacts.
- Excellent adhesion to avoid particle generation, which can reduce the longevity of light alloys in space.
- Resistance to radiation in its many space-shaped forms including AO, P+, E- and ultraviolet.
- Outgassing protection, tested by total mass loss (TML) and collected volatile condensable materials. The testing conditions of Mercury requires less than 0.1% of outgassing.
- Resistant to extreme temperatures and heat fluctuations. Materials need to cope with extreme temperatures of up to 450 °C and cryogenic temperatures as low as -185 °C.
- Corrosion resistance during time spent in storage. Protecting $2bn worth of work from corroding in cleanroom storage before launch.
By carefully adjusting the parameters of Keronite's plasma electrolytic oxidation (PEO) technique, Keronite’s engineers were able to pioneer a new coating that made the mission possible: PEO in white.
Plasma electrolytic oxidation changes what's possible
At the beginning of the BepiColombo project, it was apparent that existing coating technologies were not meeting the grade. As it stood, the satellite’s sophisticated onboard measurement devices would likely have suffered damage, potentially failing. To ensure this didn't happen, the ESA set two benchmarks for any coating to make the grade:
- The coating would need to absorb less than 25% of alpha radiation (⍺S < 0.25)
- Reflect over 85% of infrared radiation (𝜀IR > 0.85)
Before the project began, coatings formed by plasma electrolytic oxidation could only obtain absorption and reflectivity values of ⍺S > 0.3 and 𝜀IR < 0.7.
Knowing the previous strides they’d made with PEO coatings, Keronite’s scientists were convinced they could transform the highly-tailorable coating technology to meet these benchmarks.
Keronite set up a development program to ensure the BepiColombo mission could go ahead with the lightweight alloys key to its success. By carefully adjusting the parameters of the PEO technique, Keronite’s engineers launched a systematic study to see if they could expand the possible and bring the ESA to Mercury. Their research investigated the effects of:
- Coating formulation (how could variations the electrolyte bath, applied voltage and more modify the characteristics of the coating?)
- Coating thickness (how would thickness affect ⍺S and 𝜀IR values?)
- Use of sealers and various top coats (how would top coats adhere and perform?)
An industry-defining advancement in ultra-white coatings
Keronite’s careful testing resulted in a new material with unprecedented properties: PEO in white. The new white coating exceeded the ESA’s specifications, making the BepiColombo mission to Mercury (due to arrive on Mercury in 2025) a reality. In the process, Keronite had broadened industry, material science and space exploration by:
- Developing two all-new PEO coatings for thermal control; low solar absorptivity and high infrared emissivity.
- Identifying a clear relationship between coating thickness and ⍺S and 𝜀IR. values.
Yet there's still room for improvement. Recent research and development at Keronite has highlighted opportunities to offer comprehensive top-coats with even higher reflectivity values. To learn more about our progress, get in touch with our technical team.
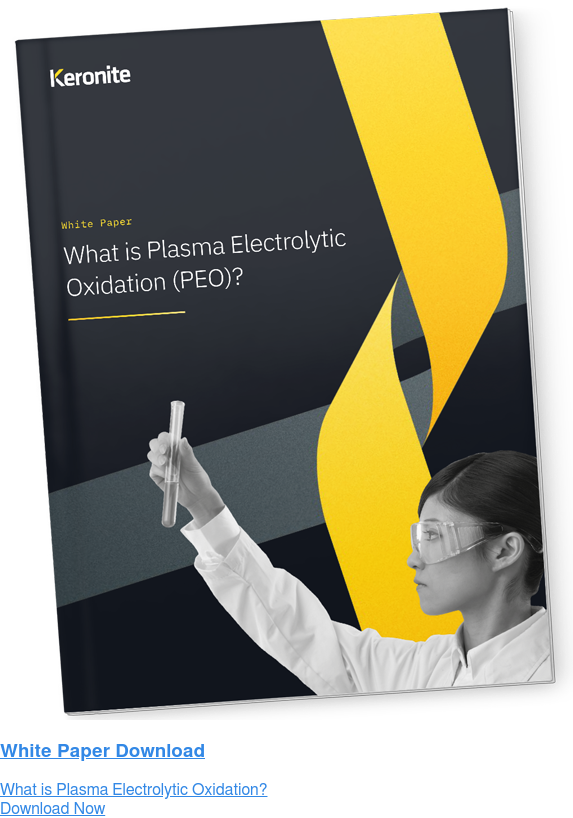
