Black coatings for light alloys in space: solar absorptivity and infra-red emissivity
5 October 2022For materials engineers aiming to reach the depths of space, the night sky represents the two colours most likely to help them in their quest. The bright white of the stars mimics the low solar absorptivity and high infra-red emissivity provided by ultra-white surfaces. Keronite have shown how their white coatings are helping the likes of the European Space Agency (ESA).
Complementing the bright white stars, the dark swathes of the rest of the galaxy represent the extremely high solar absorptivity of black surfaces. By absorbing stray light, black surfaces channel thermal energy to enable extremely precise optical measurements. Although a relatively new discovery, Keronite's black coatings have already been taken up for all sorts of uses on satellites, spacecraft, & the International Space Station. We'll explore a few of these uses in this article. Yet Keronite's scientists have identified means in which to improve the performance of these coatings for more extreme applications – more on that later.
Lightweight Dreams
While the lightness of aluminium makes it theoretically ideal for spacecraft (keeping weight and fuel costs down), its tendency to corrode when untreated can affect its ability to travel in space. The extreme temperatures of take-off can warp aluminium, while the humidity levels of up to 70% RH that the ISS is exposed to accelerate corrosion. On Earth, surface coatings including paint & anodising have been used as 'good enough' solutions (although increasing environmental awareness is making all industries wary of these approaches due to their toxicity). In space, they won't quite cut it.
Conventional anodised coatings are simply not able to provide the stable thermo-optical properties essential for space exploration. Recent environmental legislation has prevented the use of nickel sulphide and cobalt sulphide due to their lasting toxic effects. Keronite were approached by a range of aerospace organisations (from ESA to the Institute de Astrofisica de Canarias) to research how their carefully controlled PEO coatings could create an aluminium coating capable of withstanding the intense demands of space travel.
Black Surface Solutions
The extremely high solar absorptivity of black surfaces makes them an ideal coating for space exploration. They minimise light reflection to ensure accurate optical measurements and effectively control thermal transfer across all components in a spacecraft. But could black surfaces be used to enhance and protect lightweight aluminium components for space travel?
Keronite's scientists used PEO technology to successfully develop a new black coating for aluminium. A micrograph comparison of black Keronite and black hard anodised coatings shows the superior stability and regularity of the Keronite black coating:
Figure 1. SEM images: Hard anodized coating on a sharp corner (left), Keronite's PEO coating on a similar sharp corner (right). Both coatings were formed on a AA7075 substrate. Note the cracks in the hard anodized coating, where the PEO coating is more uniform and shows better coating retention.
Figure 2. Optical micrographs: Hard anodised coating showing through-thickness columnar cracks (left), and a Keronite PEO coating showing uniform coating coverage and good edge retention (right).
By looking in more detail at a few of the ways space exploration has already adopted PEO in black, we'll see how Keronite's surface technology is set to revolutionise the aerospace industry (and beyond) with environmentally friendly, extremely durable coatings.
Black PEO coatings in space
Keronite's scientists worked to space agencies' requirements by experimenting with variables such as the applied voltage, electrolyte composition and time treated to find a number of solutions that uniquely improve material performance in space.
Keronite's black coatings can already be found in space, such as these four pioneering examples:
Satellite barrels
Figure 3. Barrel for satellites treated with Keronite. This coating has been extensively tested for humidity, vibration, debris formation and low optical reflectivity. Image courtesy of Cilas Marseilles
Cilas Marseilles have seen how Keronite's black PEO coatings is an ideal casing for satellites. Extremely lightweight, they've demonstrated the extreme humidity, vibrations, and debris formation that PEO can withstand, all while reflecting less than 0.1% of light (a better value than any reported for super black Ni-P coatings).
Cryogenic sliding bearings
Figure 4. Keronite and MoS2 composite coating on EMIR GRISM cryostat wheel bearing. The coating has been tested for wear resistance, debris formation and stickslip behaviour.
Keronite's PEO technique allows extremely precise adjustment of every parameter. This means the porosity and crystallisation of the coating can be closely controlled. The Instituto de Astrofisica de Canarias wanted an extremely resistant coating, capable of resisting cryogenic temperatures while providing ultra-low friction for bearings to be used in space exploration.
Keronite's engineers created a black coating with suitable porosity to contain a solid lubricant (MoS2). The resultant coating maintained an extremely low friction coefficient at cryogenic temperatures: outperforming plastics and ideal for spacecraft!
Micro-calorimeters with thermal-control
Figure 5. Keronite coated micro-calorimeter mounted on the MEDET system for the ISS.
CNES, ESA, the University of Southampton and ONERA launched the Material Exposure and Degradation Experiment (MEDET) in 2007. Keronite coated thermal control micro-calorimeters were mounted on the MEDET flight hardware and are now located on the ESA's Colombus Laboratory on the ISS. Keronite's bespoke black coating made sure the calorimeters survived the impact of takeoff, and continue to absorb light radiation to ensure accurate measurements can take place.
Sun sensors
Figure 6. Corse Sun Sensor (CSS) – left. Fine sun sensor (FSS) – right. Both treated with Ultra-black Keronite.
The extremely high absorptivity of PEO's black coatings (>90% light absorbed) make them an ideal housing for sun sensors: without them, stray light reflected from other components would make the sensors' results too inaccurate to trust. The versatility of Keronite's PEO method means fine or coarse housing can be created depending on how a sensor is meant to react to other components around it in a spacecraft.
Back in ultra-black
With PEO, Keronite have made lightweight aluminium an integral part of space exploration, without the need to compromise corrosion resistance, radiation absorptivity, or environmental impact. The PEO process is readily scalable, with potentially radical applications on Earth and far beyond!
Keronite continually hones their coatings to meet the developing needs of industry: thanks to customer set targets, as of 2019 Ultra-black applied to 6000 series aluminium alloys now absorbs 96 percent of solar radiation and emits over 90% of infrared, all while providing high levels of corrosion and wear resistance.
Get in touch to see if Keronite's surfaces could give you a lightweight solution that can even withstand extreme exposure to galactic levels of wear and radiation!
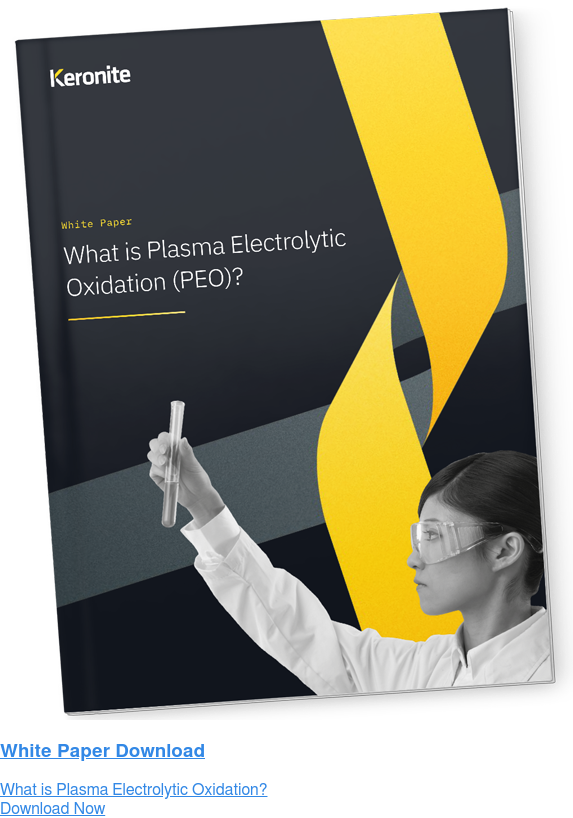
