The importance of dielectric insulation for electric vehicle battery packs
20 October 2023Electric vehicle (EV) designs and battery packs are using increasingly higher voltages to maximise driving range. As a result, battery housing components need to have a high level of dielectric strength to avoid leakage circuits and other issues.
At the same time, designers are trying to reduce the weight of designs with light metals like aluminium to maximise energy efficiency. However, these metals have a naturally low dielectric strength, which is something that can be solved with advanced surface coating solutions.
In this article, we examine the challenge of dielectric insulation in context with battery housings and surrounding components, and how advanced surface coating is an effective solution.
Dielectric insulation - why is it important?
Dielectric strength is the measurement of a material’s resistance to electromagnetic currents. Measured in kV/mm, it is the maximum point at which a material experiences electrical breakdown and becomes conductive. As such, materials with high dielectric strength are considered reliable insulators for surrounding circuits and conductive materials.
For EV battery packs, dielectric insulation is a necessary step in design to ensure safety and component reliability. The insulative resistance of surrounding materials and components can be easily affected by temperature, humidity and vibrations. As such, there needs to be a dedicated insulative layer between battery packs and their housings, or there is a risk of current leakage that can harm users and surrounding components.
Can light metals be used for battery packs and housing components?
EV designers have shifted towards higher voltages and energy capacity to battle the challenges of charging speed and driving range. This has led to larger, high-power battery packs that are typically 0.55-0.92 times the overall length of the vehicle.
Because of the higher voltages of these battery packs, the dielectric strength of surrounding materials needs to be enhanced in parallel. Without it, a leakage circuit can easily take place where the current penetrates the insulating layer to the chassis ground. This directly puts electronics and users at risk.
In terms of material choice, battery pack and housing components need to showcase a specific set of characteristics alongside a high dielectric strength:
- Thermal resistance to prevent thermal runaway.
- Good tensile strength to reliably support the battery pack.
- Low weight to maximise driving range and energy efficiency.
The three above characteristics can be found in aluminium alloys. They showcase high thermal resistance and impressive thermal conductivity (210 W/m-K) to help regulate the temperature of battery packs. Specific alloys such as the 7000 series also exhibit excellent tensile strength (up to ~750 MPa) in a lightweight package to maximise energy efficiency.
The main issue is that aluminium is a conductive metal with a low dielectric strength, but this can be solved with advanced surface coating technology.
Advanced surface coating technology to enhance the dielectric strength of light metals
Advanced surface coating technology like Plasma Electrolytic Oxidation (PEO) can enhance the dielectric strength of light metals like aluminium. It utilises a customisable electrolyte bath where a high and controlled voltage is passed through. This stimulates plasma discharges on the substrate of the submerged component, creating an outer ceramic oxide layer with a range of protective characteristics.
In terms of dielectric strength, the outer aluminium oxide layer created by PEO exhibits dielectric strengths ranging from 15-20 kV/mm. By customising the electrolyte solution with silica and other additives, this dielectric strength can be significantly enhanced by upwards of 50-80 kV/mm.
Additionally, PEO coatings have high thermal conductivities in comparison to other insulative materials such as plastics. PEO coatings typically have thermal conductivities of 4-8 W/mK, versus <1 W/mK for typical insulative plastics. This, along with a relatively low thickness of ~40-60 um, means that the thermal properties of the battery pack and cooling performance are much improved. Further, PEO coatings will not burn and are highly resistant to temperature.
For electric vehicle battery housings, PEO enables engineers to integrate lightweight aluminium components without risk to components or users. Moreover, PEO also provides resistance to thermal and vibration related wear, extending the lifespan and insulative properties of said components.
Using PEO to optimise EV design
In the constant and rapid innovation present in the EV industry, designers are looking towards lightweight components to optimise weight and maximise driving range. Where this is simple for some elements of design, areas such as battery housings require specific characteristics such as dielectric strength to be viable.
The unique PEO coating process allows for the fine tuning of specific resistances with a crystalline structure that is resistant to a range of elements and greatly enhances dielectric strength. This enables engineers across industries to safely reduce the weight of their designs whilst extending the lifespan of their components.
To find out more about how PEO can help reduce the weight of EV designs without detriment to dielectric insulation, send an enquiry today.
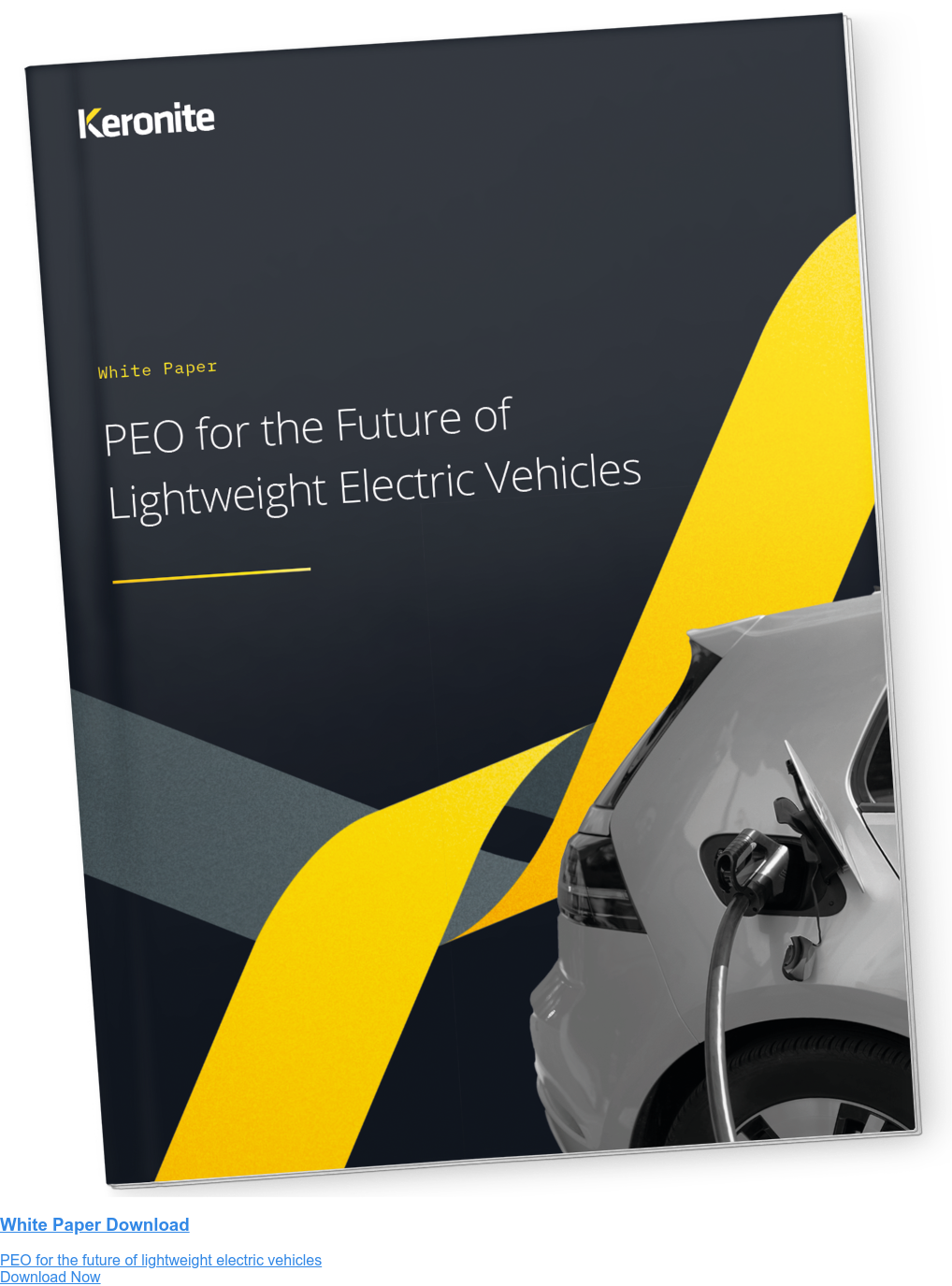
