Dielectric breakdown strength: PEO for high-performance power equipment
8 September 2023More than half of industrial fuel consumption could be eliminated through electrification, according to McKinsey. With renewable energy generated increasing, and supporting infrastructure being deployed, electricity is becoming the go-to energy source for heavy transport.
The remaining challenges are all focused on scale and performance: how can these applications perform more efficiently, when will the supporting infrastructure be available to support the switch? The answer to both questions could be the materials they use: advanced materials that improve performance, enable manufacturers to industrialise technology and meet their exhaustive list of requirements.
Alloys, particularly aluminium and magnesium, offer an interesting opportunity. As lightweight materials, they could provide a means of reducing the weight of heavy transport. But they also possess high strength ratios, meaning that they can be used to replace heavy metals like steel. There are tradeoffs, but with advanced surface technologies, these, increasingly, are minimal.
A commercially viable solution is available, in the form of the innovative surface coating technology plasma electrolytic oxidation (PEO). PEO adds a high dielectric strength insulating layer to the surface of light metal alloys, protecting against wear and corrosion, and extending their life. PEO allows engineers to specify light metals that reduce the weight and cost of high-performance power equipment, making them attractive commercial alternatives to current approaches.
What are dielectric properties and why are they important?
In electrical assemblies, some components need to conduct, others must be insulated. Dielectric strength is a measure of a material’s insulating performance, and is measured in kV/mm, or volts per unit thickness. A material’s dielectric strength also tells engineers and materials scientists at what voltage the material will decompose and start conducting.
A material with a high dielectric strength is a good insulator. Conversely, low dielectric strength materials are poor insulators. Aluminium and magnesium alloys are increasingly used in heavy transport and industrial electrification projects but are excellent conductors. If the light metals are in contact with live parts, the assembly could fail, causing both safety and cost issues.
Dielectric strengths vary widely. For example, the dielectric strength of air is 3 kV/mm. Typically excellent conductors, metals do not have a dielectric strength as they do not insulate. Polypropylene, a widely used electrical cabling insulator, has a dielectric strength of 22 kV/mm. Most surface coating technologies will deposit aluminium oxide on the surface of an alloy, which, depending on the alloy, will have dielectric strengths varying from 14.6 to 16.7 kV/mm.
Why are dielectrics relevant to electrification projects?
Materials with high dielectric strengths are excellent insulators and perform an essential role in electrification projects. Industrial plant and vehicle electrification depend on high dielectric strength materials. Structures, assemblies, components, pylons, power lines and cables, switchgear and cabinets must all be insulated.
Polymers are excellent insulators, but many applications require materials with specific properties, which eliminates most polymers. Lightweighting is a key factor in electric vehicle design because it extends range, so aluminium and magnesium alloys are attractive. But they can only be used if they are non-conducting, which means introducing an insulating barrier between the metal and live components.
Light alloys require high dielectric strength surfaces
There are many types of insulating barriers. Examples include polymer coatings, inert gasses, or a surface coating that uses the metal alloy’s oxide as the insulator. Aluminium is widely used in power electronics for cables, switchgear components, racking and pylons, which bring the alloy into contact with live parts, so it needs an insulating surface.
Light metal surface oxide layers provide limited insulation, so uncoated aluminium components may not provide sufficient insulation for a high voltage application such as switchgear. Magnesium components are widely used in electric vehicles with similar challenges of unintentional contact with live parts.
To benefit from lightweighting, engineers and materials scientists can choose a surface coating technology that can be tailored to provide specific dielectric strength, for example PEO.
What is PEO?
PEO is a surface coating that provides a high dielectric strength layer on light metals. This enables aluminium and magnesium alloys to be used in electrification projects and power electronics. PEO uses plasma in an electrolyte bath to form a dielectric coating on the surface of the light metal component. The component is placed in an electrolyte bath and plasma-chemical processes result in the deposition of an oxide layer.
The light metal’s surface coating can be adapted to the specific needs of the application. This is achieved by controlling the oxide layer’s thickness. Thickening the oxide layer increases the dielectric strength. Aluminium oxide, the main component of the PEO surface layer on an aluminium alloy, has dielectric strengths ranging from 14.6-16.7 kV/mm. When silica additives are included in the electrolyte bath, the resulting surface coating develops dielectric strengths of between 59 and 79 V/µm.
The components are immersed in a bath and not sprayed, so complex shape edges are crack-free. This prevents localised dielectric failure caused by penetration. The electrolyte bath is non-harmful so there are no environmental concerns. Depending on the final application, design engineers and materials scientists can choose from a wide range of dielectric coating solutions. In turn, this means that light alloys are now commercially viable and sustainable in a much broader range of applications.
For more information about PEO coatings and how they offer commercially-attractive insulating options for power electronics and electrification projects in heavy transport and industry, get in touch. Our experienced team of materials scientists can develop custom dielectric coatings for aluminium and magnesium, designed to provide insulation in new electrical applications.
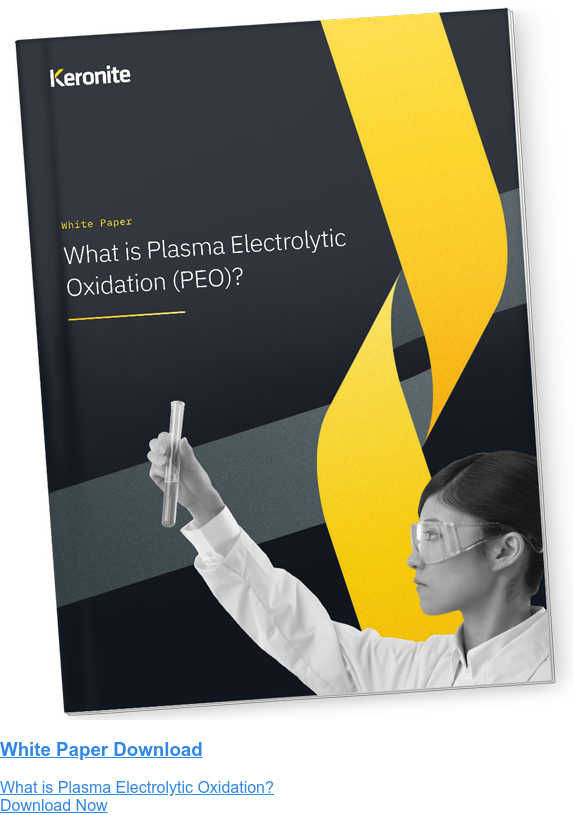
