3 high dielectric strength coatings for light alloys
30 August 2023As the world transitions from fossil fuels to electricity, the role of materials is fundamentally changing. To cope with higher power systems and the need for greater efficiency, materials need to provide excellent electrical performance while retaining other necessary qualities. Work by materials scientists at Keronite is highlighting exactly how organisations are managing these new requirements.
For example, new electric vehicles are launching with multiple high voltage motors. These are capable of offering efficient performance, but to be lightweight and safe materials need to be electrically insulating while lightweight. With advanced surface coatings, light alloys of aluminium can be transformed so that they are up to the task.
What is a dielectric surface coating?
In high voltage systems, protecting people and other electrical equipment is critical. To do this, dielectric surface coatings create an electrical barrier, reducing conductivity and increasing the dielectric breakdown strength of the material.
While the dielectric breakdown strength is an important factor, there are other considerations while selecting an appropriate coating. Coated components can also display different thermal properties, often reducing the thermal conductivity of the component, which can be a challenge where the component also performs a cooling function. Dielectric coatings can also alter optical properties, making a component more or less reflective or emissive.
By choosing the right dielectric surface coating, materials scientists and engineers can specify light alloys for many applications across the aerospace, automotive, industrial, energy and consumer products sectors. Surface coatings enable light alloys to be used in new and exciting ways in these industries. The resulting performance characteristics provide benefits including weight savings, longer service life and improved safety.
What is dielectric strength and why is it important?
Measured in volts per unit thickness, usually kV/mm, dielectric strength is a measure of a material’s insulating performance. It also identifies the point at which the voltage applied is high enough that the material starts to breakdown and conduct. A high dielectric strength means good insulating performance. A low dielectric strength means the material is a poor insulator and, when a sufficiently high voltage is applied it will start conducting.
To put dielectric strengths into perspective, air has a dielectric strength of 3 kV/mm. Insulators used in applications like electric cabling, such as polypropylene, have dielectric strengths of 22 kV/mm. Aluminium oxide as formed on the surface of aluminium alloys as a result of most surface coating technologies has a dielectric strength ranging from 14.6-16.7 kV/mm, depending on its exact composition. While relatively high, this clearly is not sufficient for many applications so special measures are needed to form coatings with higher dielectric strengths.
Dielectric coatings for light alloys
Many high performance applications require materials with performance characteristics that are like both a light alloy and a ceramic. They need the high strength, low weight characteristics of a light alloy, but also need to have insulating properties like a ceramic. For example, magnesium alloys have unique radio frequency (RF) shielding properties and are used widely in electronic devices. However, if components are not kept electrically isolated then then devices could fail or cause safety issues. Dielectric surface coatings make this possible.
There are several approaches to forming dielectric coatings:
1. Thermal spray coatings
The thermal spraying approach superheats particles, usually in powder or wire form, into droplets and sprays them onto the substrate. The droplets adhere to the metal alloy substrate forming an insulating layer. Ceramic coatings with high dielectric strengths applied as thermal sprays include aluminium oxide and magnesium aluminate.
This technique is effective for maintaining dielectric strength in tough environments with high temperatures. However, it has several limitations. The droplets result in a coating pattern that makes it unsuitable for sensitive microelectronics applications. Because of the spray application, it provides inconsistent results across components with complex geometries.
2. Hard anodising
Hard anodising uses an acid bath with an electric current running through it to accelerate oxide growth on the light alloy’s surface. A distinctive feature is that the thickness of the oxide layer can be tightly controlled. The result is some control over the performance characteristics, such as corrosion resistance, thermal conductivity and dielectric strength. Thicker oxide layers deliver greater dielectric strength and they can operate at high temperatures, up to 5000 degrees centigrade.
Hard anodising is impacted negatively if there are impurities in the substrate. This results in localised dielectric strength reduction that in turn can lead to current penetration through the oxide layer. The sulphuric acid bath required for the anodising process requires specialist treatment before disposal. The high defect density and columnar pores typically seen in hard anodised coating, particularly for complex geometries, is also not good for dielectric strength.
3. Plasma electrolytic oxidation (PEO)
PEO uses an electrolyte bath and a plasma mediated process to form the dielectric coating. The light alloy part sits in a room temperature electrolyte bath and a high voltage is applied. This stimulated plasma discharges at the surface of the part which drives the conversion of the surface into a ceramic oxide layer.
The oxide layer’s thickness can be finely controlled, enabling engineers to adapt the resulting characteristics to the application. Thickening the oxide layer increases the dielectric strength. Aluminium oxide, the main component of the PEO surface layer on an aluminium alloy, has dielectric strengths ranging from 14.6-16.7 kV/mm. Recent research has shown that aluminium with a PEO surface coating that includes silica additives have dielectric strengths of 59-79 kV/mm.
The edges around complex shapes are crack free, which prevents localised dielectric failure as a result of penetration. And there are no environmental concerns, as the electrolyte bath is non-harmful. Further since PEO coatings are formed at least partially by conversion of the substrate (in contrast to most other processes that deposit an additional layer only), the adhesion to the substrate is exceptionally strong.
Conclusion
Most surface coating technologies, such as thermal spray, add a layer of a material rather than directly converting the substrate. Many apply a coating of a silica or polymer-based coating to provide the insulating layer. In contrast, PEO forms the coating at least partially from conversion of the substrate forming a very high dielectric strength coating which is well adhered to the substrate in one step. A further advantage of coatings such as PEO is how multiple performance criteria, such as thermal and optical properties as well as dielectric strength, can be controlled.
Depending on the final application, design engineers and materials scientists can choose from a wide range of dielectric coating solutions. In turn, this means that light alloys can be used in a much broader range of end-applications than was previously possible.
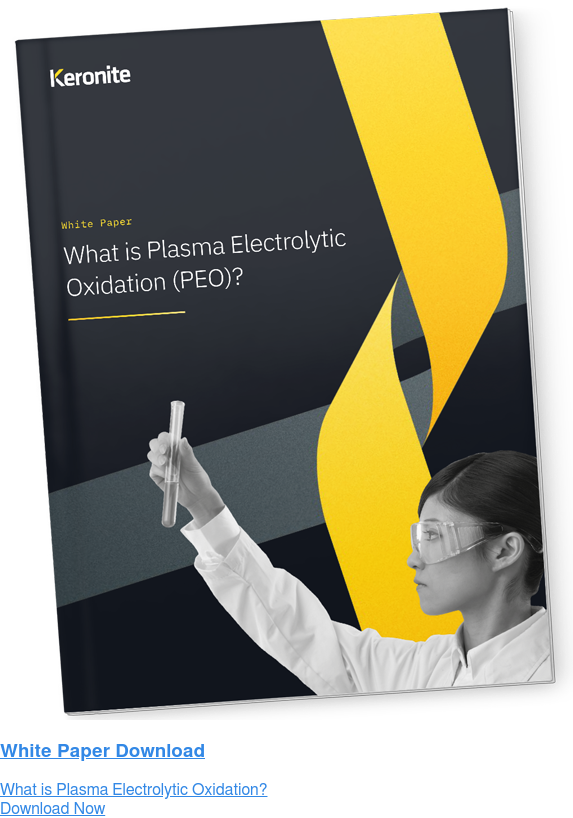
