Surface coatings for the thermal control of light alloys
25 October 2021Light alloys such as aluminium, magnesium and titanium are increasingly being used to replace steel in a variety of applications. Their low density and high strength-to-weight ratio makes using these materials attractive to many industries, especially those looking to reduce weight without compromising on performance. But how do light alloys cope with the high-temperature environments that many of these applications require?
Advances in surface treatment technologies means that light alloys can now be used to fabricate more and more industrial components. Introducing wear resistance (through performance coating techniques) to aluminium and magnesium alloys means that they can rival steel and cast iron in a variety of applications. Their low density and high strength mean that transport industries such as automotive, aerospace and marine, are adopting light alloys in their bid to reduce weight and fuel costs.
In these applications, metal alloys are not only exposed to wear and corrosion, but also extreme temperatures. Take an internal combustion engine as an example, temperatures can reach up to 900 °C. This can put a huge strain on the surrounding metal components, affecting tensile properties and propensity to cracking, not just affecting performance, but increasing risk to life.
How do light alloys perform in high-temperature environments?
Extreme temperatures can have a number of detrimental effects on metal components. Some of these effects, such as changes in ductility and temporary loss of mechanical strength, are reversible.
Creep and relaxation are irreversible changes which can be accelerated by high temperatures. Creep is a phenomenon which covers a wide range of deformation mechanisms. This can occur as a result of exposure to high mechanical stress and is generally more severe in materials that are subject to high temperatures for prolonged periods of time.
Aluminium
Pure aluminium melts at 660 °C. It is also relatively soft and demonstrates poor wear resistance. When we talk about the use of light metals in industrial applications, we’re referring to the use of light metal alloys. When aluminium is doped with alloying elements such as silicon, manganese, copper or magnesium, its useful properties dramatically improve.
Certain aluminium alloys (e.g. 2618 alloy) have been specifically designed for heat-resistance, retaining mechanical strength, ductility and creep resistance when exposed to elevated temperatures. They can be used for generator/compressor impellers, vacuum pump rotors and engine pistons.
Magnesium
Magnesium alloys are also used for light-weighting. In the automotive industry, magnesium alloys are mostly used for interior components. Yet, they have the potential to be used in electronic products and aerospace applications in place of aluminium, steel or plastic parts. Rare-earth elements can be added to magnesium alloys to improve creep resistance at high temperatures and reduce flammability.
Titanium
Titanium alloys typically have high tensile strength and toughness. Like aluminium and magnesium, titanium alloys are often used for light-weighting in the aerospace industry. The high cost of titanium components limits their use in high-throughput manufacturing applications, so titanium alloys are generally used for high-performance parts within the aerospace industry. High strength-to-weight ratios, excellent corrosion resistance and endurance of high temperatures means that titanium alloys can be used for aeroplanes, missiles, and rockets.
Further improvements for heat resistance
Selecting the correct alloy for a given application is key to maximising the lifespan of a metal component. But additional measures can be taken to improve temperature resistance of light metals. Surface coatings can be used to create a barrier between the extreme temperature environment and the metal substrate.
Thermal barrier coatings (TBCs) are designed to insulate metal components, protecting them from large or prolonged heat exposure. TBCs generally have high thermal resistance and excellent insulation properties. Yttria-stabilised zirconia (YSZ) coatings are well-established TBCs used in the automotive and aerospace industries. However, these are typically applied using plasma spraying or electron beam physical vapour deposition. Application is complex, expensive and adds significant processing time to component manufacture. The resulting coatings can also have variable thermal barrier properties.
PEO coatings as TBCs
Plasma electrolytic oxidation (PEO) can be used to apply thermal barrier coatings (TBCs). This involves submerging the metal component in an electrolyte bath and passing through a high-voltage current. A uniform ceramic coating is formed at the metal surface, which can achieve low to moderate thermal conductivities, as low as 0.2 W/mK. For comparison, a typical YSZ surface coating (EBPVD applied, 6 – 8% Y2O3) might have a thermal conductivity in the region of 2.5 W/mK.
Coating thickness, composition, and thermal conductivity of PEO coatings can be tailored by altering the composition of the electrolyte bath and the applied voltage sequence. Mullite-rich or alumina-rich coatings can be developed, depending on the expected usage temperatures of the component. Keronite has developed coatings for aluminium engine pistons which are stable up to 900 °C. These coatings have demonstrated excellent performance when compared to anodised aluminium and further testing has been carried out to predict fuel consumption performance. Results showed a 3 – 5% improvement in efficiency under part-load conditions.
PEO coatings have the potential to improve thermodynamic performance in combustion engines. This, combined with the effects of reducing component weight through the use of light alloys has significant performance implications for a range of applications, including automotive and aerospace. For more information on our world-leading surface treatments for light alloys that can be specifically tailored to your application, get in touch today.
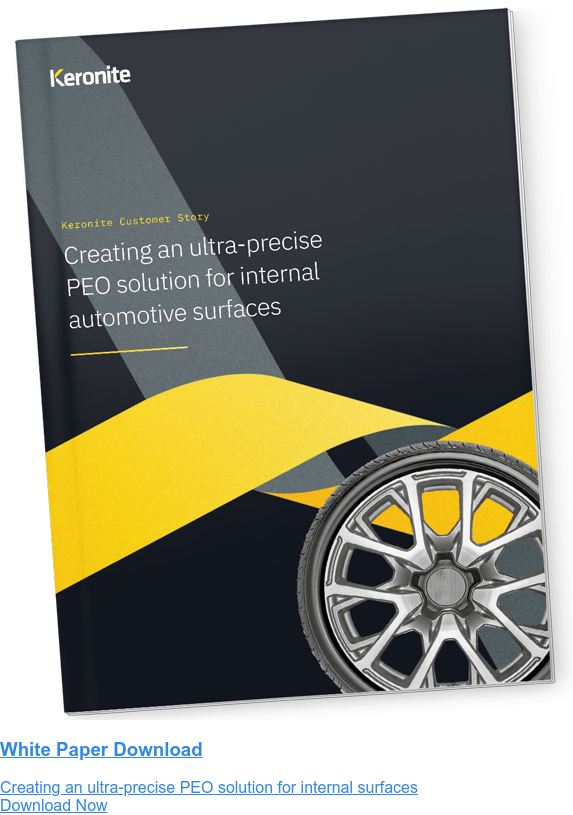
