Improving the performance of industrial robotics
3 December 2019Until recently, robots were only offering limited value to manufacturers. But now, they are proving a real asset, all thanks to breakthroughs in science and technology.
Advances in artificial intelligence and machine learning are opening more opportunities for robots. They are also changing how they work. Equipped with sensors and on-board computers, robots can respond to their environment. This is making them dependable, accurate and reliable. Now, manufacturers of all kinds are hoping to boost their productivity through robotics.
The rise of robotics in industrial settings
Demand for robotics is surging in the five largest manufacturing economies. Globally, there are 85 robots for every 10,000 employees. But in some parts of the world, there are more than 300 per 10,000 employees.
The global state of robotics
- 73% of global robotics sales come from five of the world’s largest manufacturing economies
- China leads the way with robotics: 36% of robots sold in 2017 were to the People’s Republic.
- Korea has the most robots per employee, with 710 robots per 10,000 employees in manufacturing
- Demand for robotic equipment is expected to increase by 45% before 2021
The key difference between machinery and robotics is the presence of intelligence. Intelligence facilitates thought, and any machine that thinks, can be labelled a robot. Robots respond and interact with the world around them. As software improves, robots will become more versatile. They won't only be able to automate repetitive tasks.
Applications for industrial robots
A leading robotics body has found three industries bought a quarter of a million robots in 2018. The International Federation of Robotics reports that automotive, electronics and metal industries are the biggest users of robotics globally.
These industries all share common manufacturing practices. They are all manufacturing at high volumes and their operations lend well to the use of robotics:
Robotics for transferring materials
Transporting materials from one location to another is no longer a manual process. Automotive manufacturers are using robots to transfer parts across the factory floor. Robots are taking processed parts from one part of a factory to another.
Robotics for processing parts
Robots are also now capable of manipulating tools and processing parts. Using sensors, they can track their own progress and get simple jobs done. For example, robots are often used to spray paint, grind or polish parts.
Robotics for product assembly
The repetitive nature of product assembly is light work for a robot. They can work continuously and error-free, meaning robots can outperform human labourers. They can also conduct quality checks using sensors – even in hazardous or acidic operating environments.
The next generation of industrial robotics
Robots are set to become more useful and valuable than ever before. Robots are currently working well in repeated processes. Artificial intelligence and machine learning advances will open new opportunities to introduce robots. Equally, there are opportunities to improve the performance of existing robot designs. Materials science has an important role to play, especially in the creation of advanced surface technologies that enable robots to last longer and operate in more testing conditions.
Surface technologies for industrial automation
Robots are complex machines. They contain sensors, chips and motors in significant quantities. While this helps make the machine intelligent, there are more components that can fail. This is where surface technologies come in.
Surface technologies for light alloys are critical for keeping robots functioning. They are also useful in improving throughput, making robots more productive without reducing their life. As, unfortunately, robots frequently suffer from several modes of failure:
- Fretting. One of the most common causes of machine downtime in factories. Robots that transfer materials are prone to damage, especially on contact surfaces. Fretting damages the surface which can cause corrosion.
- Corrosion. Corrosive substances and acidic factory environments accelerate corrosion. Robots that process parts are typically more prone to corrosion, especially when using corrosive substances.
- Thermal shocks. Robots are typically deployed where it is hazardous, unsafe, or unproductive to have a labourer. Therefore, robots are often employed to process parts at high temperatures. Thermal shocks expand light alloys, which can cause cracks and instigate a number of wear issues.
Robots that are built for assembly are often built intricately. Therefore, these robots often have many components with complex geometries. Sufficiently protecting light alloys in these forms becomes difficult, as many materials science solutions cannot guarantee sufficient coverage – especially on corners.
Finding the best surface coating for robotic components
Off-the-shelf coating solutions simply won’t cut it. As robotics introduces parts with greater complexity, materials need to be enhanced to suitably protect these equipment.
Keronite are the world leaders in plasma electrolytic oxidation (PEO) technology. The bath-based conversion coating can be manipulated to create some of the world’s most advanced surface coatings. Keronite’s scientists specialise in creating coatings that uniquely improve the performance of materials in tough operating conditions.
In the automotive and electronics industries, where robots are already used extensively, Keronite’s coatings offer an opportunity to improve their performance. By increasing the life of light alloys in these robots, manufacturers are able to reduce downtime, improve processing throughput and enjoy greater profits.
Keronite specialises in creating bespoke coatings where off-the-shelf solutions do not meet the grade. To learn more about plasma electrolytic oxidation, download our white paper or get in touch with our technical team to learn more about how PEO performs.
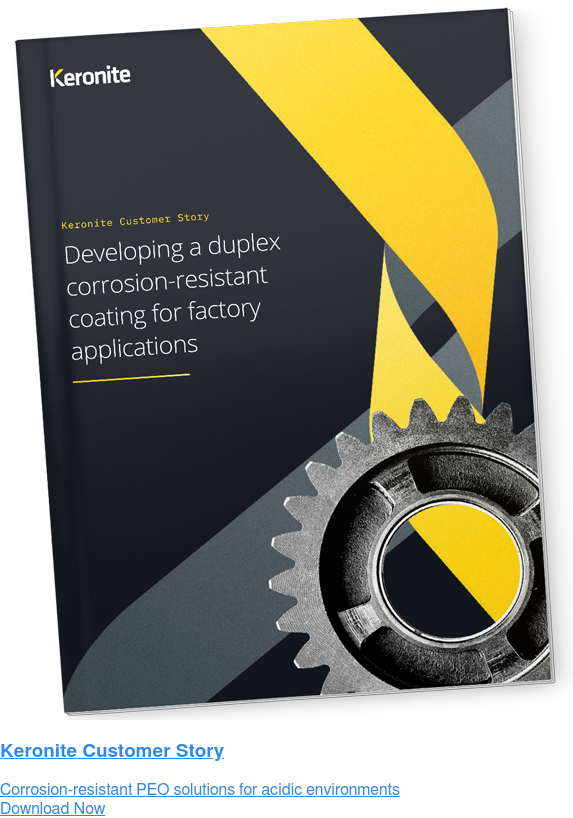
