Aluminium’s role in the automotive sustainability agenda
2 November 2022Sustainability has become a key strategic priority for the automotive industry. Manufacturers are not only electrifying, but they are adopting more sustainable materials and operating in far greener ways to reduce the impact they have on the planet.
The industry has already made huge strides, demonstrated by the growth in electric vehicle sales. Last year, electric vehicle sales doubled, hitting a global sales volume of 6.6 million vehicles, while production has trebled since 2018.
Materials science has been a significant technology enabler in this transition. Aluminium provides a light, yet high-strength, alternative to steel which is more than two-thirds heavier than some Al alloys. But what’s interesting about aluminium is its recyclability – which has many wondering: could aluminium alloys allow us to create a fully-recyclable car? If so, what materials challenges are preventing automakers from doing so?
Using aluminium as a sustainable solution: results vs challenges
Aluminium is one of the most widely recycled materials on the planet, with recycling rates exceeding 90% in most industrial markets. Recycling aluminium offers a 95% energy saving over casting new aluminium. It also reduces the use of oil – meaning the world could save more than 90 million barrels of oil per year in the United States alone.
In the process of designing a sustainable and recyclable car, aluminium is a prime candidate for structural applications as it is already used throughout automotive manufacturing. It has a low density whilst maintaining an impressive strength-to-weight ratio. Engine parts, bumpers and wheel rims are often made with aluminium alloys as they are significantly lighter than steel and strong enough to operate effectively. Better yet, aluminium based car frames are reported to have the potential to lower a vehicle’s life cycle global warming potential by 7.8 metric tons of CO2.
The challenges of designing an almost completely aluminium-based vehicle, however, derives from the lack of hardness it offers for specific components. Aluminium is vulnerable to friction-initiated wear due its comparative softness. It provides natural corrosion resistance, but for the harsh environments faced by vehicles, they require more comprehensive protection.
Vital car components such as axle carriers face extreme stresses on regular use, and are in direct contact with moisture, grime, and other elements. Not only would aluminium face extreme corrosion in this environment, but would be worn down quickly due to the regular abrasive wear. Because of this, specialised metal alloys are used instead, which often cannot be recycled as they release harmful toxins during the process.
Coated aluminium alloys - a sustainable solution?
Metal coatings present a solution to creating aluminium based vehicle designs. Methods such as anodising and spray coatings provide automotive designers with the necessary features of corrosion and abrasion resistance, allowing them to take full advantage of aluminium alloys for various components. However, some coating methods introduce toxic chemicals or materials that limit aluminium’s recyclability. For example, epoxy resin or plastic based coatings make aluminium difficult or impossible to recycle due to their permanent and irreversible cross-linked structures.
Plasma Electrolytic Oxidation (PEO) is an advanced surface coating technology for light metals that does not affect recyclability. PEO’s unique technology uses an electrolyte bath and plasma discharges to form a ceramic-like duplex coating for aluminium alloys. It involves no toxic chemicals, and the electrolyte solutions are typically benign, alloying for easy and clean disposal. As a result, big automakers can utilise PEO surface coating to successfully design aluminium based vehicles that function effectively whilst maintaining the recyclability of the metal.
Boosting life, reducing weight and improving recyclability with PEO
It is clear that the future of automotive manufacturing revolves around the repurposing of available resources to manage emissions and the finite materials that are available. In order to incorporate recyclable light metals like aluminium into your designs, Keronite’s industry leading PEO acts as a solution.
The unique PEO process involves three distinct stages that each enable engineers to tailor and adjust variables to meet the precise requirements of automotive components. It also creates a porous top layer to the metal’s substrate where sealers can be introduced to provide further customisation of surface properties. PEO provides light metals like aluminium with the necessary features to be used in harsh environments without impacting recyclability.
To learn more about the capabilities of our PEO coating method in the automotive industry, download our data sheet below or get in touch with a member from our science team. We’ll work directly with you to provide a bespoke solution to your sustainable design challenges.
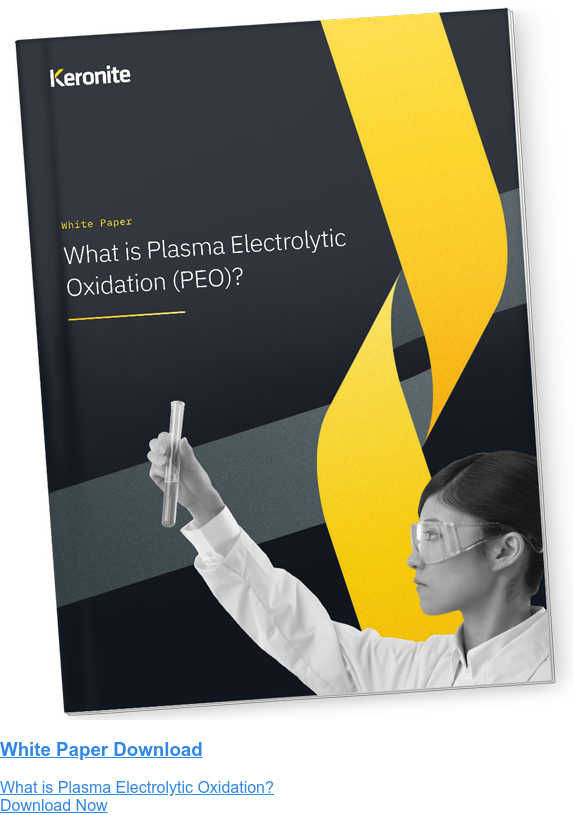
