What is the future of anodising?
3 October 2017For almost 100 years, anodising has been a go-to method for increasing the corrosion resistance of lightweight metals. Despite its familiarity to surface engineers, the downsides of the technique are making its future problematic: toxic emissions, potential weaknesses in the coating produced, and increased costs due to lower component lifespans – all things manufacturers want to avoid! In this article we'll take a closer look at anodising, its drawbacks, and see how new technologies like plasma elecrolytic oxidation are learning the lessons of the past, bringing the learnings of anodising into future coating developments.
What is anodising?
Anodising converts the surface of a metal into a corrosion-resistant, somewhat durable and often decorative oxide surface. For this to happen, the metal is placed in an electrically conducting liquid solution that contains oxygen. The most commonly used solutions are sulphuric acid and chromic acid. When an electric current is passed through the solution, a chemical reaction occurs at the surface of the substrate: oxygen in the solution reacts with the metal at the surface to form a layer of the metal’s oxide.
While the metal itself may be weak, prone to corrosion, and hard to coat, the metal’s oxide is fundamentally different. It is strong, corrosion-resistant, and often more porous than the metal itself, meaning it is much easier to apply coats of surface treatments. Because of this, anodising drastically expands the potential uses of metals like aluminium, magnesium, and titanium. Coated surface treatments provide extra lubricity, resistance, and aesthetic properties, while the increased strength and corrosion-resistance mean that the lightweight properties of the metal can be used in structural and design settings all over the world, in all sorts of sizes and climates.
Anodising today
Anodising is a prevalent surface coating methodology, made use of by all sorts of industries, including:
- Aerospace: Crucial joins and components are anodised to enable the use of lightweight alloys while withstanding intense wear at high altitudes.
- Smartphones and laptops: Apple pioneered the use of anodised aluminium with an aesthetically appealing finish to keep weight down and style up.
- Cooking utensils: Anodised saucepans, for instance, can make them non-stick, scratch-resistant, and capable of withstanding high temperatures and wear.
- Window frames: Anodised metal is often used by architects to ensure buildings are weatherproof and structurally sound.
This is just a small sample of the widespread use of aluminium: almost every industry with an interest in lightweighting and increased wear resistance has made use of anodised metal. There are clear benefits to anodising, but the rise of alternative innovative technologies have brought attention to some of the drawbacks of anodising:
What are the setbacks?
Despite its popularity, recent technical developments have shown three potential setbacks to anodising:
- Environmental: Although anodising is deemed environmentally safe, its use has become highly regulated: although anodised coatings are entirely non-toxic, waste products from the anodising process are extremely hazardous. Aluminium hydroxide and degraded sulphuric acid are both listed as hazardous materials, and sulphuric acid fumes can pose a danger to workers and the environment at large. If an anodising operation is large enough, safely processing the hazardous byproducts produced can become a major effort.
- Cost: The difficulty of replacing anodised coatings can mean that machine parts exposed to prolonged wear need to be entirely replaced once the anodised coating wears down. Anodising is typically used on components within a larger assembly. Like most coatings, anodising will wear down with use and when the anodising coating wears the larger assembly could fail. It may be possible to replace the coating, although often the component part is destroyed when the coating wears. It may require a new component plus coating, or in extreme cases, the failure may cause damage rendering the entire assembly unusable. Whilst the initial price of the coating may appear good value, the lifetime cost of the assembly should be considered taking into account replacements and retrofits.
- Wear resistance: Although anodising does greatly increase the wear resistance of metals, there is always room for improvements. In particular, the tendency for anodic oxide layers to form with cracks mean they tend to deal badly with extreme changes in temperature. Any technology that can offer longer lasting surfaces is welcome, as is any technology capable of guarding against the creep and cracking risks that can come with anodised metals.
In a world increasingly concerned with issues surrounding the environment, energy consumption, and costs, the future of anodising should be green, long lasting, and cost effective.
PEO makes it new
Plasma electrolytic oxidation (PEO) is an exciting extension of anodising. Although first used by the USSR to lightweight space rockets, Keronite have pioneered the possibility of using PEO in a wide range of performance-led applications and consumer markets (not just those with the budget of a national space program). Like anodising, PEO involves the formation of a strong, inert surface by passing an electric current through a metal placed in an electrolyte solution. There are some crucial differences:
- PEO uses much higher voltages than anodising, creating plasma discharges at the surface of the metal that lead to a ceramic surface coating.
- The resultant surface has a crystalline structure that can lead to 2-4x the strength of anodised surfaces.
- The microstructure of PEO coatings take an irregular form and so avoid being susceptible to cracking.
- No toxic waste products are produced as a result of PEO.
- A wide range of electrolytes can be used to change the material properties of the ceramic coating, including its porosity.
Every aspect of the PEO process can be controlled with a great degree of accuracy. Small changes can cause major aesthetic and material changes in the wear-resistant surface produced, and Keronite’s scientists continue to perform extensive tests in order to guarantee that their PEO surfaces are optimised for specific purposes.
As new, highly innovative surface coating technologies are appearing, the benefits of standard and hard anodising are becoming less impressive. For integral components, a higher performance coating may be required. Get in touch with the Keronite engineers today, to see if Keronite can deliver a custom PEO-induced ceramic coating that helps your components excel.
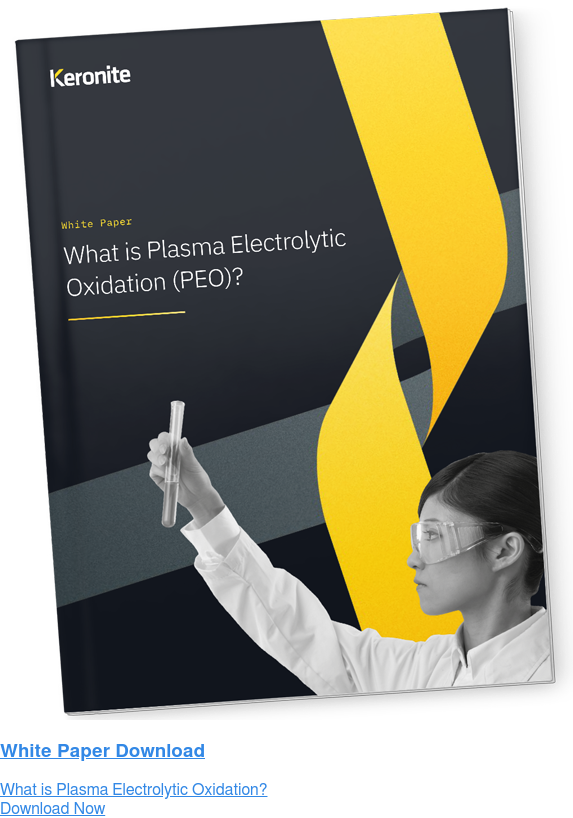
