The role of multi-functional surface coatings for oil & gas
15 November 2021The oil and gas industry is facing a series of new challenges, as are the materials used in the sector. As natural reserves become increasingly difficult to find and reach, new techniques, often referred to as unconventional, are much more complex and present tougher operating conditions for materials.
Equipment used in unconventional oil and gas are exposed to seawater, which accelerates the rate of corrosion and reduces component life. Extreme heats and, moreso, high pressures also chip away the useful life of materials. Whilst battling these harsh conditions, equipment needs to be reliable and perform predictably – especially in applications requiring controlled corrosion.
Unconventional techniques equate to new surface challenges facing the oil and gas industry
In unconventional oil and gas, subsea equipment (such as pipelines, well-heads and manifolds) may be submerged for weeks at a time. Whilst submerged, they are exposed to wildly fluctuating temperature conditions, from a low as -60°C to 200°C, as well as >103 MPa pressures (one thousand times higher than sea-level atmospheric pressure). Seawater also becomes a problem when exposed to dissolved hydrogen sulphide and carbon dioxide. Ionic salts also create more corrosive conditions in the seawater.
In addition to corrosion, wear and abrasion are also common challenges. Abrasion and wear can significantly affect the surfaces of pipelines, depending on flow rate and sediment content of the oil and gas fluids. Microbial activity within the pipelines can also increase corrosion rates.
Production and refinement facilities are subject to a different set of highly corrosive conditions. The combination of moisture, sea salt and water provide the perfect conditions for steel corrosion. Because production facilities are often static, metal surfaces are also subject to microbial corrosion and fouling.
Components are usually manufactured from stainless steel alloys, but light metal alloys based on aluminium or titanium are increasingly being used thanks to their high strength-to-weight ratios. Both aluminium and titanium are relatively easy to weld and shape, making them versatile options for complex components.
Protecting production assets to increasing operational life
Corrosion is the biggest threat to the safety and integrity of marine structures for the oil and gas industry. The industry is tightly regulated and equipment must undergo regular inspections to ensure that damage due to corrosion does not pose a risk.
Oil and gas production facilities are typically expected to have a lifespan of between 10 and 25 years, sometimes longer. A range of strategies are used to protect equipment that’s designed to operate in such extreme conditions. These can include powder coating, spray applied paints and even anodising. Due to the recent shifts in the industry, the performance of these coatings are under tight scrutiny.
Multi-functional duplex surface coating technologies
An innovative approach to protecting light alloy components from corrosion, abrasion, and wear is to use plasma electrolytic oxidation (PEO) surface coating technology. PEO coatings are suitable for light metal alloys such as aluminium, magnesium, and titanium. The metal substrate is immersed in an electrolyte bath and a voltage is passed through, creating a ceramic coating on the metal’s surface.
The composition of the electrolyte and the voltage sequence can be finely tuned to create a thin-film ceramic-oxide layer. This coating protects the metal substrate from corrosion and can increase the metal’s hardness and abrasion resistance. PEO coatings demonstrate excellent resistance to through cracking and can be applied to components with complex geometries. This can prevent galvanic corrosion at welds and bends.
The outer surface of a PEO coating is porous, so can create an ideal surface for the adhesion of subsequent coatings or sealers. Secondary coatings might be spray-applied to create a “duplex” coating system. Traditional coating chemistries can be used, such as epoxy coatings to enhance corrosion protection and chemical resistance.
Polyurethane (PU) additives also show excellent adhesion to the PEO layer and are used to improve corrosion resistance. PU coatings are often used as a topcoat as a variety of colours and aesthetic finishes can be formulated. Other specialist coatings for the oil and gas industry, such as intumescent coatings or thermally resistant coatings, can also be applied directly to the PEO layer.
Learn more about plasma electrolytic oxidation
For more information about the use of duplex coating systems to protect assets in the oil and gas industry, get in touch with our expert team of materials scientists. We create custom PEO coatings that are specific to your application and its challenges. Our coatings technicians can carry out bespoke development work and accelerated testing to ensure excellent performance when combined with a sealer that meets your requirements.
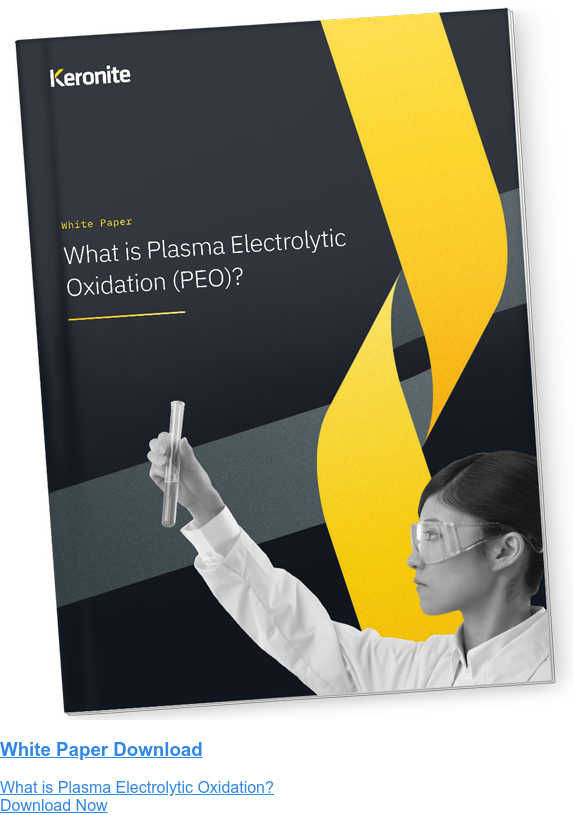
