Controllable surfaces: PEO for unconventional oil and gas
3 March 2021Unconventional oil and gas extraction accounts for a growing share of global hydrocarbon production. During 2019, 7.7 million barrels of oil a day were produced in the US, with an estimated 174 billion barrels of oil and 7299 trillion cubic feet of shale gas reserves still available in the US alone. Whilst production fell during the 2020 pandemic, unconventional hydrocarbon extraction techniques remain an important asset while the world looks towards clean, low-carbon energy sources.
Due to their favourable strength to weight ratios, low density and other key properties, aluminium and magnesium alloys are widely used in multiple applications in the oil and gas industry. However, the real value of light metal alloys has been turning one of the less positive performance characteristics, rapid corrosion under certain conditions, into an advantage.
Materials scientists at Keronite have created a highly-controllable advanced surface coating that uses new techniques to control the corrosion and dissolution rates of components in ‘unconventional’ oil and gas systems.
Why light metals corrode rapidly in high temperature conditions
Adopting unconventional techniques puts components and machinery in a variety of testing conditions, even within the same geographic location. These can combine to create a hostile environment for aluminium and magnesium alloys. These conditions include a combination of:
- Temperatures of up to 260 degrees centigrade, although most onshore wells operate at temperatures in the range of 80-160 degrees centigrade
- Pressures of up to 240MPa
- Naturally corrosive fluids circulating in porous and permeable reservoir formations. Fluids include brine (concentrated sodium chloride and potassium chloride in water) and in acid gas / sour gas reservoirs high levels of methane, carbon dioxide and hydrogen sulphide
- Corrosive chemicals used in the unconventional oil and gas extraction process. Depending on the extraction phase and proprietary technology used, these can include acids such as HCl, polymers, salts, gelling agents and antifreeze. Many of these substances can aggressively attack, corrode and eventually dissolve uncoated aluminium and magnesium alloys.
Aluminium and magnesium alloys benefit from a ceramic like surface coating formed naturally when exposed to the oxygen in air. The corrosive fluids will rapidly break down this layer. For example, the naturally occurring chloride ions in brine and sour / acid gas reservoirs will break down the oxide film, a process which is accelerated in high temperatures.
Using surface coatings to control dissolving rates
Dissolving components are a critical part of many unconventional oil and gas systems, and, for their natural susceptibility to corrosion, light alloys provide numerous advantages over glass fibre and epoxy or phenolic resin composites, ceramic and steel equivalents. Rather than being milled out, requiring an additional downhole operation and increasing risk of ball stumps blocking tubing, the magnesium and aluminium alloy components completely dissolve.
However, one of the unique requirements of dissolvable components is that they need to dissolve predictably. Ideally, an engineer would understand and be able to accurately predict how long a dissolvable component will survive in variable temperature conditions. While uncoated light alloys will begin to dissolve immediately (and reduce to nothing in just a few hours), surface coatings such as PEO can delay this dissolution by hours or even days.
How plasma electrolytic oxidation (PEO) finely controls corrosion
Both the protection and the precision control can be achieved using the unique surface coating technology plasma electrolytic oxidation (PEO). PEO’s unique technology uses an electrolyte bath and plasma over three distinct stages to form a ceramic-like duplex coating on magnesium and aluminium alloys. By adjusting variables, such as the timing, contents of the bath and voltage, the coating thickness can be finely controlled.
The outer layer is porous, which enables additional performance enhancing substances to be added by using the electrolyte bath. Its porosity and resulting roughness means it is an ideal substrate for additional layers, such as polymer sealants, to further control the properties.
This means that the life of components in unconventional oil and gas settings can be minutely controlled like never before. Plasma electrolytic oxidation coatings with a duplex coating solution can extend the life of these components by several weeks, if required. And, when it is time to dissolve the components, mechanical means can be used to breach the protective surface coating. Rapid disintegration can then ensure.
To learn how surface coatings such as PEO enable engineers and materials scientists to control magnesium and aluminium’s performance, and use these alloys in wider applications by preventing corrosion, click below to download the whitepaper.
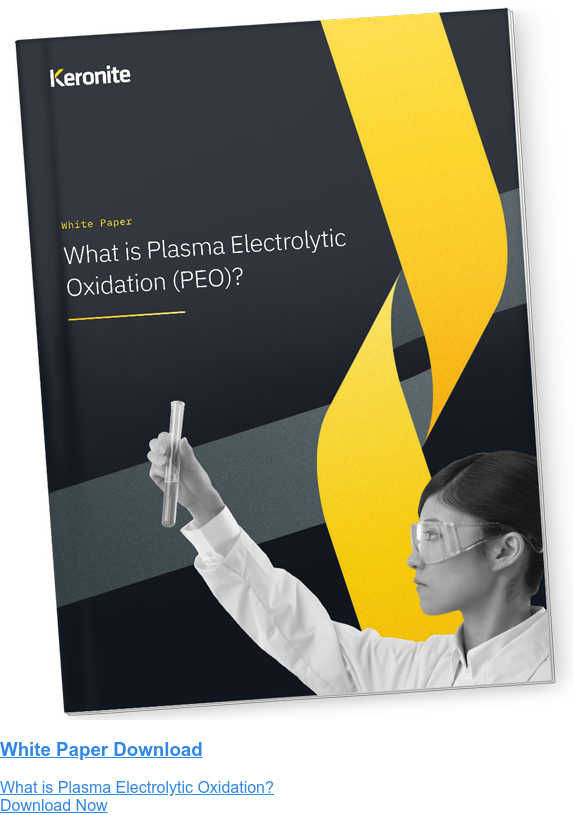
