The future of light alloys and composites in sports
13 May 2021At the top end of sport, every possible advantage that can help an athlete compete better, recover better and perform at a higher level will be taken into consideration. But, in many sports, the equipment can play a role in enabling an athlete to perform at their very best.
New innovations are customary across almost every sport, from the carbon-fibre plates that are breaking world records in running, to the lightweight aerodynamic components in F1 that yield fractions of a seconds off lap times. Every inch of performance that can be squeezed out of a piece of equipment, will offer a competitor a unique advantage.
This goes for golf clubs, tennis rackets, bicycle frames and even high-performance electric motors in professional racing, too. Each requires a unique combination of characteristics to comfort, performance and safety in mind. Material selection is an important factor in striking this balance. Metals, such as lightweight alloys and composites are widely used in the production of sports equipment, because they offer a high strength to weight ratio, resistance to impact and a stiffness that assists and enhances performance.
Carbon fibre and light alloys for sports equipment
Carbon fibre is one of the most renowned materials in sports. Its popularity surged in the automotive industry initially, offering a high strength with significant weight advantages over other conventional materials.
Although carbon fibre offers the performance characteristics required by the sports equipment market, repairing damage to carbon fibre equipment is not easy, potentially limiting the lifespan of kit which may have been expensive to purchase. Recycling this material is also more complex than alternative materials, an issue becoming increasingly prevalent in today’s ethically minded society. For this reason, carbon fibre bike frames are often preferred in controlled, road racing conditions, but for harsher, more unpredictable environments, aluminium is still favoured.
Magnesium and its alloys are also widely used for manufacturing sports equipment and offer easier repair and recycling processes compared to carbon fibre. Although magnesium offers equipment designers the performance and machining characteristics required for producing sporting equipment, it is highly reactive, making it susceptible to corrosion. Because magnesium alloys readily corrode, without treatment they are an unsuitable choice for outdoor applications, preventing the light metal from reaching its full potential in the sports equipment market.
Titanium is also favoured in some sports. Golf clubs, for example, are typically made from titanium alloys. Drivers typically have a ‘sweet spot’, which can be increased in surface area, allowing the club to be driven quicker to generate more speed and ‘drive’ the ball further down the fairway. Titanium also has good vibration characteristics, as well as being both stiffer and softer than steel.
However, innovate anti-corrosion surface coating technologies, such as Plasma Electrolytic Oxidation (PEO), can enable light metals such as magnesium and magnesium alloys to be used more broadly in sports, by improving the corrosion resistance and other performance characteristics of the metal.
New opportunities for sports equipment of all kinds
Carbon fibre and magnesium play an integral role in the creation of equipment and essential kit for a range of sports. They can both be formed into intricate shapes, making them ideal for many very niche manufacturing applications in this sector.
Tennis rackets and golf clubs, lacrosse sticks and even baseball bats all benefit from the strength, stiffness and light weight of these metals. Allowing athletes to enjoy a comfortable grip, a better swing and more control over their equipment on the playing field.
Cycling, snowboarding and skiing are other examples of where lightweight construction can really improve speed and performance, with carbon fibre and magnesium both featuring heavily in the production of bicycle frames, and carbon fibre boards for winter sports.
These metals not only provide superior performance for sporting equipment but are also advantageous in the production of sportswear and safety kit too. Magnesium in particular is specified for its ability to absorb shock and vibration, making it ideal for the design of helmets, and the wheel attachments of in-line skates.
The case for magnesium in sports performance
Magnesium is extremely light. It is 75% lighter than steel, 50% lighter than titanium and 33% lighter than aluminium. Although the stiffness-to-weight ratio for steel, aluminium and magnesium are the same, this does not scale linearly with thickness.
There are a number of equipment applications within the sports sector that benefit from magnesium’s unique characteristics. For example, vaulting poles are commonly manufactured using magnesium due to its high torsional strain resistance which minimises twisting.
Compared to carbon fibre, magnesium is simple to machine, can be injection moulded and is entirely biocompatible, posing no toxicity hazards. It has the highest known damping capacity of any structural metal, capable of withstanding 10x more than aluminium, titanium and steel.
Magnesium is also easier to repair and recycle, offers excellent noise, vibration and harshness (NVH) properties and better energy absorption.
Using anti-corrosion coatings to broaden the use of magnesium in sports equipment
Despite its many favourable strength and performance characteristics, and the easier repair and recycling processes associated with magnesium when compared to carbon fibre, its chemical reactivity and speed of corrosion is a challenge that must be overcome so that the sports equipment industry can use this metal to its full potential.
Surface coatings, such as Plasma electrolytic oxidation (PEO), offer multiple solutions for materials scientists and engineers designing and specifying sports equipment. PEO’s unique technology uses an electrolyte bath and plasma over three distinct stages to form a ceramic-like duplex coating on magnesium alloys.
Each stage enables engineers to adjust the process to create tailored coatings for the precise needs of the sport. The multi-layered coating’s top layer is also highly porous, which can incorporate the contents of the electrolytic bath in the surface coating to include additional properties.
PEO’s fine microstructure and surface texture create an ideal physical ‘key’ for top coats – resulting in much stronger adhesion of the top coat than other surface coating technologies, such as hard anodising. This duplex system combines the improved corrosion protection of both elements synergistically to provide unparalleled corrosion protection. This enables sports equipment designers to use magnesium alloys in applications that were previously not an option.
To learn how surface coatings such as PEO enable sports equipment designers to exploit the full range of magnesium’s properties in many more sports by preventing corrosion, click below to download the whitepaper.
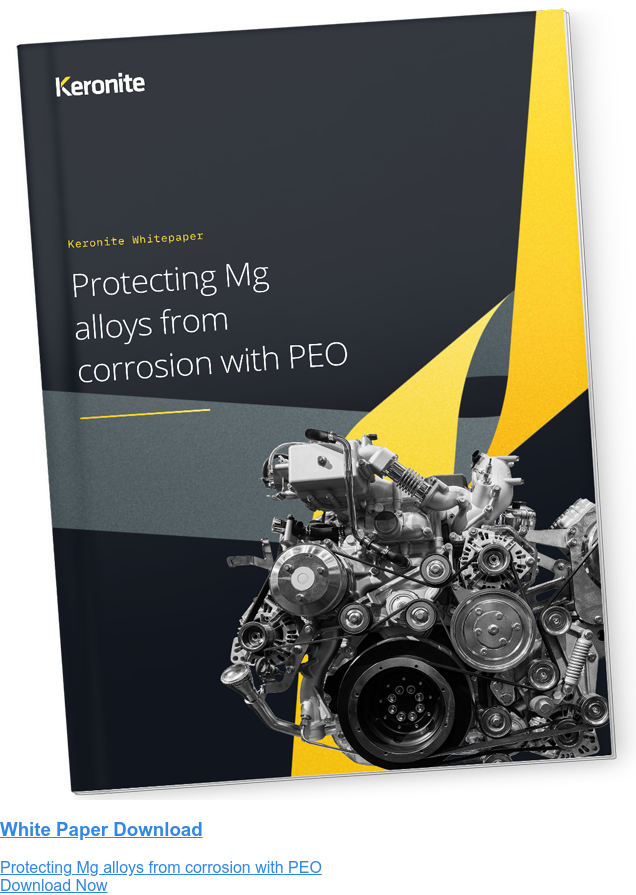
