Advanced surface coatings for next-gen textile manufacturing equipment
29 November 2019Since the industrial revolution, machines have played a vital role in textile manufacturing. Now, all the processes involved in turning fibres into fabric are automated. The techniques have not changed radically, but the equipment that performs this task has.
But that has not devoid the industry of innovation. In the 20th century, man-made fibres, like nylon and polyester, have risen in prominence. These fibres introduced new qualities, so can be used in a greater variety of use cases. We’re also demanding textiles in far greater quantities than ever before. This is putting new pressures on the machines that produce them.
Man-made fibres introduce new manufacturing concerns, also. Nylon fibres are much more abrasive than plant and animal fibres. Abrasive fibres wear down equipment more quickly. In response, the industry now lubricates yarn. These lubricants can cause corrosion if equipment isn’t sufficiently protected.
Advanced surface coatings are essential for protecting textile manufacturing equipment. As the industry looks to improve productivity, doing so while reducing downtime and expense is critical.
Improving component service life
Components in manufacturing environments regularly fail. In the textile industry, it’s the components that are in constant contact with yarn and fibre that are most prone to failure. Spin rotors, rollers and yarn guides are particularly problematic components. These components are in constant contact with abrasive materials, which are often lubricated with oil-based substances.
As manufacturers have sought to shorten lead times and boost profitability, the throughput of textile manufacturing machinery has increased. Fibres, yarns and resultant fabrics are moving quicker and quicker. While this is boosting productivity, it is also detrimentally impacting the service life of vital equipment.
Protecting fast-moving parts in applications where they are subject to abrasion, wear, corrosive liquids and elevated temperatures is key to increasing uptime, improving productivity and reducing costs associated with textile manufacturing.
Why light alloys?
Light alloys have become a favoured material in the textile manufacturing industry. Aluminium alloys, which are used widely in manufacturing equipment, offer a high strength-to-weight ratio. Importantly though, they are far less costly to machine than alternatives like steel.
With all of this promise, some manufacturers have faced difficulty in leveraging light alloys within their applications. Light alloys cannot provide the complete and comprehensive protective qualities required in intensive manufacturing applications. In particular, light alloys are not naturally very corrosion resistant, and with many components subject to wear and corrosion, the service life of light alloys can be radically shorter than heavier metals. But that is where advanced surface coatings come in.
There are options aplenty when it comes to protecting the surfaces of light alloys. However, there is one notable candidate that provides the optimal combination of surface characteristics for textile manufacturers. Plasma electrolytic oxidation (PEO) provides light alloys with greater tribological performance and greater levels of corrosion resistance.
Enhancing light alloys
To protect light alloys from both wear and corrosion, there needs to be strong adhesion between surface coatings. In a duplex coating stackup, plasma electrolytic oxidation (PEO) is capable of offering both qualities.
PEO is a type of advanced electrochemical conversion coating. The process involves modifying the anodic film through arc discharges. These charges occur above the breakdown voltage of the oxide film, which creates a uniquely-formed non-columnar microstructure – which gives PEO its high hardness and compliance, offering exceptional wear performance.
PEO in numbers
- Exceeded 2000 hours in salt spray testing (ASTM B117).
- 2000HV, resulting in ultra-high hardness
- Young’s Modulus values of around 30 Gpa, producing strain tolerant layers
Aside from the environmental benefits, PEO offers superior performance to anodising and other comparable techniques. Ultimately, the technique produces ultra-hard ceramic layers that are harder than steel. The formation of the ceramic layer enables corrosion resistance; acting as a ‘key’ for subsequent topcoats. Additionally, the non-columnar microstructure of PEO layers means that substrates are protected from corrosion, even where there is surface wear. There are environmental benefits over comparable treatments, too. PEO uses no organic compounds, VoCs, strong acids or heavy metals.
Greater productivity, less downtime, more profit
The intricate components involved in converting fibre to fabric are capable of performing for longer, and more quickly, with light alloys and advanced surface coatings. Components in rollers and rotors are likely to benefit greatly by improving their performance with a thick PEO coating (100–150 μm). This is enabling machines to operate for longer, at greater speed, with reduced downtime and, ultimately, reduced machine maintenance and operation bills.
Keronite are the world leaders in plasma electrolytic oxidation technology, a surface coating that uniquely improves light alloys in some of the world’s most challenging engineering applications. Keronite’s materials scientists specialise in developing bespoke-to-application surface solutions that outperform rival coatings. If you are involved with a project that concerns improving the longevity of manufacturing components, get in touch with our technical team.
Alternatively, download our white paper, ‘What is Plasma Electrolytic Oxidation?’ for more detail about our unique coating technology.
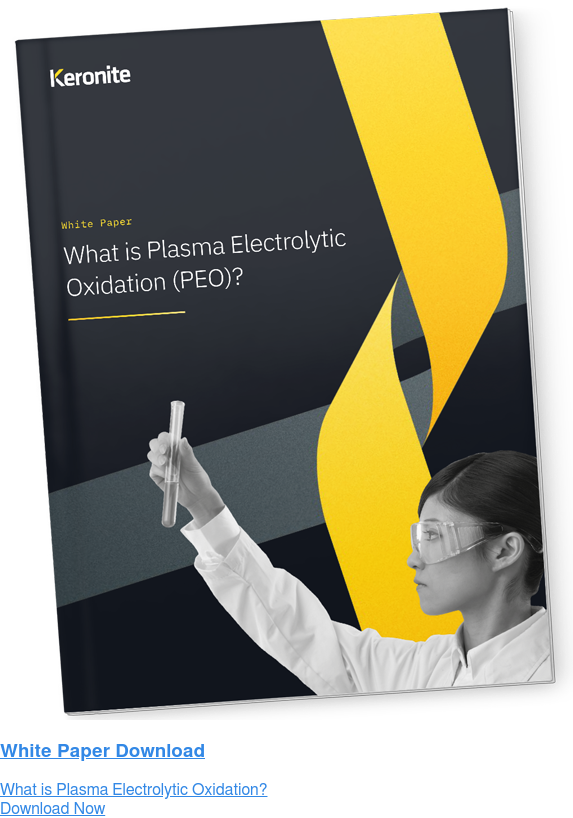
