Surface coatings for valve and alternative light metals
6 August 2021When it comes to selecting light alloys, most engineers do not venture far from Al, Mg and Ti alloys. However, this article explores the uses and benefits of some of those lesser used light alloys, such as Zirconium, Tantalum and Hafnium.
Developments in materials science and research into surface coatings have resulted in light alloys becoming some of the most used metals in tough operating environments. From the intense pressures of the oil and gas industry, to the lightweight but tough moving components of aircraft, light alloys are hugely prevalent. The medical and defence industries are not averse to the use of light alloys, either.
Most materials engineers and scientists turn to the light metals, aluminium, magnesium and titanium as the solution to their demanding engineering challenges. But there are other alternative light metals that have specific properties making them suitable for very specific high-performance applications. Some of these are lesser known, but deserve to be held in the same spotlight as their more widely known counterparts.
Valve metals include elements such as zirconium and tantalum and are known for their high resistance to corrosion, extreme temperatures, with dielectric and superconducting properties. Some valve metals do not absorb neutrons and are therefore widely used in the generation of zero-emission nuclear power.
In common with the better-known light metals, such as aluminium and magnesium, the properties of valve metals can be enhanced using surface coatings.
Introducing the valve metals
The term ‘valve metals’ refers to a collection of light transition metals from the periodic table’s group IV and V elements. These are typically zirconium (Zr), niobium (Nb), tantalum (Ta) and hafnium (Hf). Aluminium, magnesium and titanium are also classed as valve metals, but they are not the only ones deserving of this classification.
The origin of the name is disputed, but the consensus is that it stems from the metals’ electrical current conduction behaviour. Valve metals form a thin oxide layer that underpins the heat and corrosion resistant properties. That same oxide layer allows electrical current to flow one way and restricts the flow in the other direction, hence the term ‘valve’. This is called a rectifying effect.
Individual valve metals have other properties that include:
- Zirconium does not absorb neutrons
- Niobium improves strength in alloys, its oxide increases the refractive index in glass and has superconducting properties
- Tantalum creates no immune response in mammals, enabling its use in biomedicine
Each of these characteristics enables the valve metal to be used in a range of unique applications.
What are the benefits of alternative valve metals?
The core valve metals are widely used in many industry sectors. Most are used in a range of steel and light metal alloys to introduce additional strength and corrosion resistance, alongside other features. And the common heat and corrosion resistance properties mean the metals, their alloys and oxides are used in a range of laboratory and chemistry equipment.
Because it does not absorb neutrons and is heat and corrosion resistant, zirconium alloys are often found in nuclear power station pipework, fuel rod cladding and structural components. Its heat resistance properties mean it is found in space vehicles, jet engines and gas turbine parts. Zircons are also known as semi-precious stones that resemble diamonds – cubic zirconia is also much, much cheaper.
Niobium is also used in space and aerospace applications. In this form, it is found in structural materials for construction, offshore platforms and in oil and gas pipelines and manifolds. With its superconducting properties, niobium is widely used in electronics and the magnets used in medical imaging equipment such as NMR and MRI scanners, often in combination with zirconium.
Its oxide enables spectacle lenses to be thinner by increasing the refractive index of glass. Being physiologically inert and hypoallergenic, devices such as pacemakers and other medical impacts contain niobium alloys. Surface coatings can be used to create a porous top layer that aids with the speed and success of osseointegration.
The dielectric oxide layer that forms on its surface, and its ability to be thinly coated onto other components, enables tantalum to be a highly effective and small volume capacitor. In this form, it is used in mobile phones and other electronic devices. And it shares the same strengthening features as other valve metals, so it was often used in concorde aircraft nose cones, rocket nozzles and turbine blades. Tantalum is also found in surgical implants, as it is non-toxic and causes no immune response in mammals.
Surface engineering technologies for valve metals
Despite their generally impressive performance characteristics, valve metals do have some weaknesses. For example, zirconium alloys under high temperature conditions above 900 degrees centigrade will react with water to create hydrogen gas and degrade nuclear fuel rod cladding.
Niobium’s unique characteristics enable it to perform in so many highly demanding applications. However, when subjected to temperatures higher than 400 degrees centigrade, it oxidises and becomes brittle. Highly inert and therefore resistant to most acids and alkalis, tantalum can be corroded by heated alkalis, hot sulfuric acid and hydrofluoric acid.
In the same way that the more common light metals are enhanced, these chemical and mechanical flaws shown by valve metals can be easily addressed. Surface coatings can protect against specific corrosive substances, provide additional heat protection and can be seeded with additives which provide other performance improvements.
One approach is to apply an advanced surface coating technology, such as plasma electrolytic oxidation (PEO). It uses an electrolyte bath and plasma to form a ceramic-like coating on both the better-known light metals and valve metals. The PEO-derived coating has many beneficial properties that the original metal and metal alloy and their basic oxide coatings do not have. Researchers at Keronite have extensive experience when it comes to developing one-of-a-kind coatings that uniquely improve the performance of all valve metals.
To learn more about PEO, download our white paper ‘What is Plasma Electrolytic Oxidation?’ or get in touch with one of our materials scientists today.
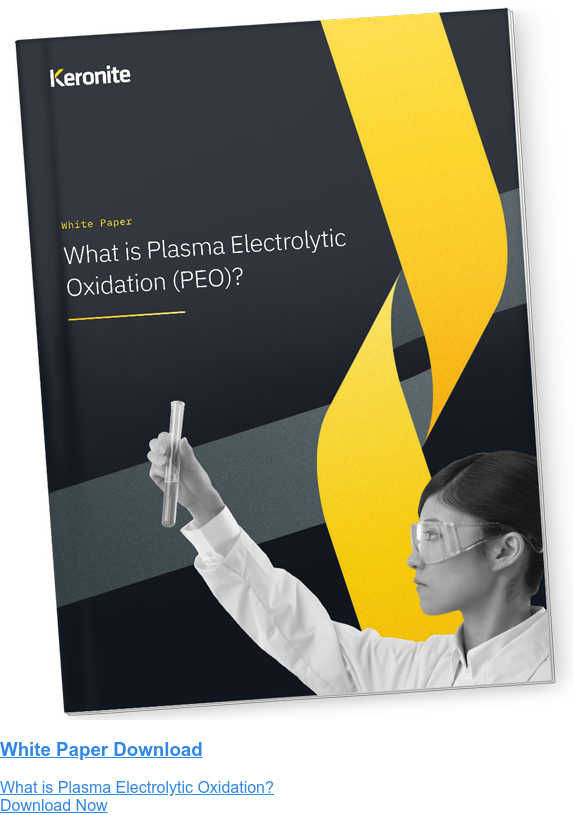
