Surface coatings for textile manufacturing equipment
13 September 2022Textile manufacturing puts a huge demand on components. Unprotected components can be damaged. Abrasive fibres, corrosive chemicals, extreme temperatures and high volume wear cause this damage. Surface coatings can protect components from these threats – but not all equally.
Without coatings, failure rates can skyrocket, as can maintenance costs. If manufacturers can find the right solution, they can benefit from greater uptime, lower operating costs and higher throughput. This increases profitability for textile producers.
Most volume produced textiles, such as wool and polyester, are precious commodities. As a result, manufacturers compete on price, especially in this era of ‘fast fashion’. This means eliminating production costs to improve margins and sweating expensive production assets. Minimising downtime resulting from unnecessary maintenance and machine failure is also a priority.
The life and performance of components can be extended. This is delivered by combining lightweight alloys with the right surface coatings. It provides the unique range of properties required. They include rigidity, thermal, hardness, chemical resistance and porosity.
Textile manufacturing is a complex and hostile environment for materials
Textile production converts fibres into yarns and weaves or knits yarns into fabrics. These are cut and made into end-products such as clothing and textile goods. Raw materials include natural fibres, such as cotton, wool and silk. Synthetic raw materials include polyester, polyamide and acrylic. Each has unique characteristics and final applications that drive diverse production processes. These raw materials and products can damage machinery. The fibres can be highly abrasive and rapidly wear machine parts.
Production machinery has become complex. Some applications, like embroidery, also require precision performance. Most textile manufacture is high volume, 24/7 process production. Machinery operating at high speeds generates high temperatures, through friction between the textile and machinery surfaces. Chemicals are used throughout, and many are corrosive, rapidly damaging unprotected equipment.
Why are light alloys used for textile manufacturing equipment?
Light alloys have properties that make them ideal for textile manufacturing machinery. The properties include low density, high ductility, a high strength to weight ratio, good thermal conductivity and generally low toxicity. The resulting component is lighter. Low toxicity means the textiles are not contaminated with harmful materials from the machinery.
The light alloy component requires less powerful motors and so less energy to do the same job as a steel component. These factors add up to production cost savings and improved margins. Alloys are more easily machined and cast than alternative component materials. This makes them cheaper to fabricate.
Yet, light alloys are typically vulnerable to chemical attack and wear through abrasion. This damage is exacerbated by the high temperature and volume operating environment. Damaged components fail. The result is downtime, lower productivity, higher maintenance costs and lower profitability.
Light alloys used in textile production machinery
Lightweight alloys used in process and manufacturing engineering typically include aluminium, magnesium, titanium and beryllium as the base. Each has the common core characteristics listed above but with extra unique features. For example, beryllium’s high Young’s modulus makes it suitable for structural applications. But its toxicity eliminates it from use in most process engineering applications, as it could cause contamination harmful to health.
Titanium has fatigue and corrosion resistance and a high strength-to-weight ratio. Normally, this would make it the ideal light alloy component. But, its high cost means it is mostly used in high value applications. This includes aerospace, oil and gas and chemical engineering, defence and medical devices.
Aluminium is low cost, plentiful, and has good electrical and thermal conductivity and ductility. It is easy to fabricate machine parts through casting, forming and machining. It is the most common lightweight alloy used in textile machinery components.
How to enhance light alloys for textile manufacturing
Engineers designing and fabricating textile production plants face a challenge. They must find lightweight materials that perform in difficult production conditions.
Using alternative materials such as steel alloys is one option. But steel alloys are heavier and difficult and expensive to work in comparison to more ductile light alloys.
Designers can instead specify coatings to protect the surfaces. Coatings make them resistant to abrasion and chemical attack. There are several coating technologies to choose:
- Hard anodising increases the thickness of the oxide layer on a lightweight alloy's surface. The thicker layer provides greater resistance to high temperatures, abrasion and corrosion. The process uses a refrigerated sulphuric acid bath with an electric current. The alloy forms the thick oxide layer.
- Plasma spray coatings: a powder coating is melted using an argon-nitrogen-hydrogen-helium flame. The melt is sprayed onto the alloy, bonding firmly to the substrate on cooling. The process is relatively low temperature, which can reduce/avoid damage to the alloy. But it is also more complex and expensive than most coating solutions.
- Plasma electrolytic oxidation (PEO). It is also known as micro-arc oxidation (MAO) or spark discharge anodizing. This approach uses an electrolyte bath to create a coating. Plasma then changes the coating during deposition. The electrolyte bath elements form part of the coating. This means that the coating’s properties can be customised.
Why are more textile manufacturers turning to PEO?
PEO coatings offer a range of benefits. These enable textile manufacturing equipment to perform in the hostile production environment. The Composites and Coatings Group’s Gordon Laboratory at Cambridge University’s Department of Materials Science and Metallurgy has done research. It shows that PEO coatings on aluminium alloys can deliver:
- Hardness of 1400-1700 HV, ensuring components withstand highly abrasive fibres and yarns. The TWI (The Welding Institute) shows PEO is three times harder than hard anodising. A further benefit is that the surface is less likely to crack (see below and figure 1).
- Thermal resistance of up to 2000 degrees centigrade for short periods, like the thermal barrier properties of a ceramic. Cambridge researchers have shown that PEO is a more effective thermal barrier than hard anodising.
- Low friction coefficients of 0.5 when dry and 0.1 when lubricated, which reduces wear and operating temperature.
- Surface porosity allows impregnation. Lubricants are used for synthetic fibres during conversion into yarns. Porosity allows the lubricants to permeate the coating and enable new qualities.
- Controllable growth during deposition. Engineers can calibrate the change in dimensions of a component as the coating is applied. Precision components can remain within tolerances.
- Crack free edges reduce friction. They improve the wear tolerance at the corners of components. Figure 1 shows how hard anodising results in cracks. The cracks run through to the alloy substrate in hard anodised alloys. This reduces both corrosion resistance and mechanical strength.
PEO delivers all these benefits. It does this without using chrome, acids or other toxic chemicals. PEO also generates no hazardous waste.
Figure 1. Hard anodised coating (left) and Keronite PEO coating (right), on a corner of a component. Note the lack of through-cracks in the plasma electrolytic oxidation coating.
Learn more about plasma electrolytic oxidation
Keronite is the world leader in plasma electrolytic oxidation. Their technology creates coatings that protect light alloys in unique ways. With precise control, Keronite’s materials scientists create bespoke coatings, created to fit the needs of the application. PEO’s versatility therefore lends itself well to these challenging applications. If you are involved with a project that concerns improving the longevity of manufacturing components, get in touch with our technical team.
Or, download our white paper, What is Plasma Electrolytic Oxidation? for more detail.
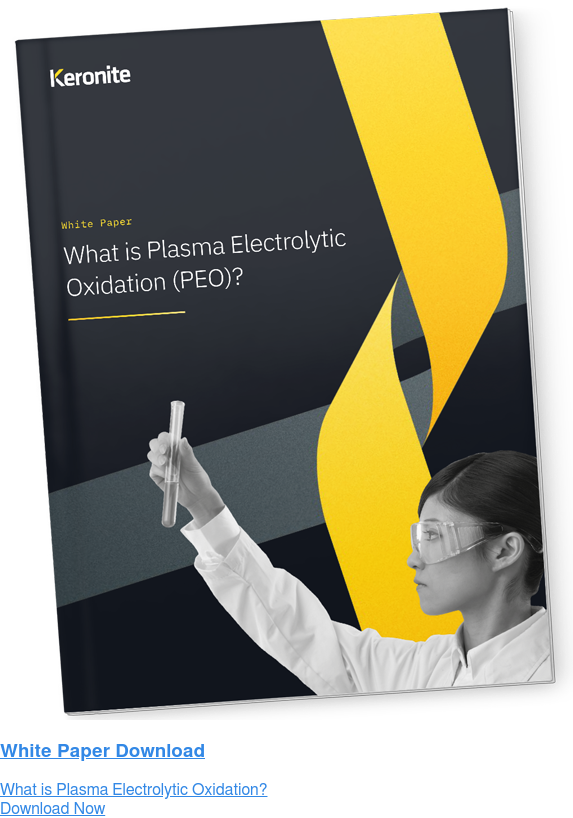
