Advanced plug and perf frac plug coatings could revolutionise the industry
27 September 2018Over the past ten to twenty years, the oil and gas industry has undergone something of a revolution. The industry has shifted its focus away from the “conventional” set of extraction techniques, which have served us well for centuries. Now that natural energy stores are depleting, more companies are looking towards innovative limited-entry techniques, allowing them to access hard-to-reach reserves.
‘Plug and perf’ is one of the most widely adopted unconventional techniques. It involves pumping a frac plug down to a predetermined depth, perforating a rock, before a ball follows in to seal and isolate the wellbore. Thanks to this highly methodical technique, the plug and perf technique creates results that can be replicated even in the most challenging of environments and well settings.
While the market has been quick to adopt these techniques, key industry figures are scratching their heads and wondering what’s next. Is it another technique? Or are there ways to make plug and perf excavations even more reliable, predictable, and rewarding? Naturally, these thoughts are instigating an industry-wide review of the materials employed within unconventional machinery.
Finding the perfect solution for plugs
To date, this method of fracking has relied on plugs that are made from a unique set of composite materials. Some have proven incredibly durable, but also eye-wateringly expensive, costing thousands of dollars per plug. The cost may be easier to swallow if it weren’t for the issues that are still prevalent in deeper extractions and other challenging wellbore conditions.
Composite plugs are non-dissolvable, which requires them to be milled out prior to production. This extra process increases the time it takes to complete an extraction, and can also prove costly, particularly in deeper wellbores. Equipment from the milling operation have been known to get stuck in wellbores, become damaged from milling debris, and require much more water to complete.
Switching from composite plugs to dissolvable solutions, such as magnesium, would allow these sorts of plugs to become completely dissolvable. They would not require milling-out, and would allow for quicker, easier and much more efficient excavations. However, these plugs require a careful mix of contrasting surface requirements – and that’s where advanced surface coating technologies such as plasma electrolytic oxidation (PEO) come in.
Plasma, plug, and perf.
- Firstly, the component is submerged in a bath of electrolyte, where the composition is tailored to provide unique surface characteristics for the application at hand.
- Then, plasma is introduced to modify the coating during the growth process, which fundamentally alters the microstructure of the resultant coating – without cracks and improving fatigue strength.
- Thirdly, elements from the electrolyte are incorporated into the coating, which gives a huge amount of control over the final coating characteristics. It’s the incorporation of these elements that can provide the unique set of coating characteristics necessary for advanced frac plug applications.
PEO coating properties could also offer a number of attractive possibilities, beyond toughness and wear resistance, that would be beneficial to fracking plug design, thanks to its the unique processing chemistry and Keronite’s trademark new product introduction process which ensures coatings are industrialised from the beginning.
The signs are more promising
Control
Control is the new order of the day in the unconventional oil and gas industry. The advanced simulation techniques that are allowing operators to plan extractions in fine details require dependable components that work to their exact specifications.
Few surface coating technologies enable this fine-level of control over coatings. On a dissolvable frac plug, the amount of time that this frac plug should last needs to be known and taken into account, otherwise, the whole excavation could be put at risk.
Every element of a coating produced through plasma electrolytic oxidation can be customised by carefully modifying the electrolyte chemistry and other processing parameters. This allows for micron-level precision for creating a dissolvable surface coating.
Debris
Limiting the amount of debris left behind by milled-out plugs is essential to the success of an operation. Chunks of composite metals left behind can cause damage to equipment, and add a degree of unpredictability to an intricately planned excavation. Dissolvable plugs coated using PEO can be finely controlled, with coating thicknesses determining the precise lengths of time required for materials to last.
Pressure and hardness
The limited entry fracking process produces significant pressure and at times can place up to 10,000+ psi levels on plugs, in part because of how they are placed and then compressed. PEO enables coatings of varying thicknesses, which would create a harder plug and reduce the chance of dents or buckling, all while ensuring materials are fully dissolvable.
Sliding wear
Efficacy, efficiency and cost are the three most important indicators of viability in unconventional oil & gas extraction. To ensure the process is quick and highly efficient, components need to perform under pressure at high speed––some techniques are designed so that production can begin after some 2-3 days after the ground has been broken.
Speed is of the essence. However, complex machinery running at continuously high speeds underground are prone to failure from a variety of known (and sometimes unexpected) challenges. Sliding wear is a prevalent issue in moving and continuously running machinery.
To achieve a surface which suitable protects components from the effects of sliding wear, methods to increase surface hardness and introduce compliance are important. Compliance reduces the risk of cracking, which leaves a substrate both exposed and weaker––leaving it vulnerable to corrosion and failure.
PEO provides this compliance through its irregular, non-columnar structure, which reduces the risk of cracking and keeps components protected when they most need protecting.
The future of fracking?
Keronite is pioneering plasma electrolytic oxidation, the world’s most advanced surface technology. If you are interested in how PEO could be used in your unconventional oil & gas projects, then get in touch with our materials scientists and find out how PEO could enhance the performance of light alloys in your components.
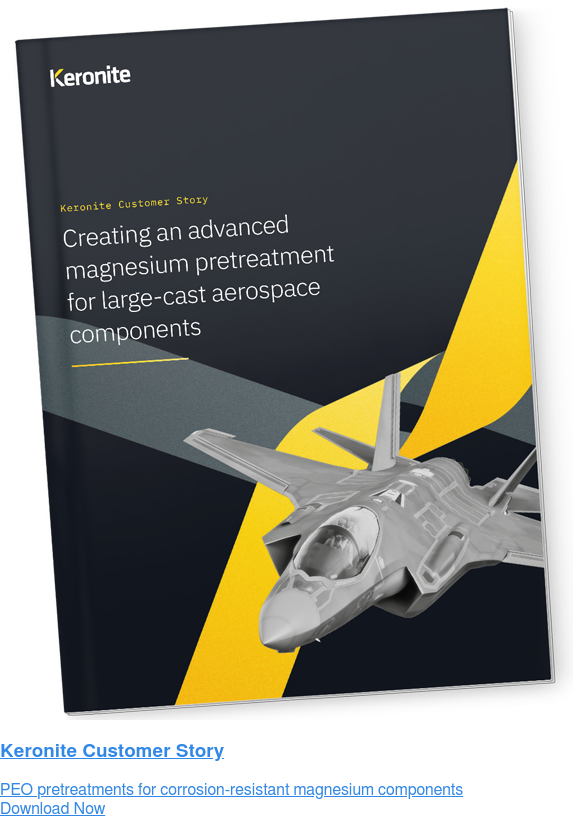
