Magnesium-aluminium alloys for electric vehicle battery housings
16 November 2023Electric vehicle (EV) design is regularly reduce weight for the sake of energy efficiency and driving range. Light metals and alloys are being studied by engineers as a result, with magnesium-aluminium examples showcasing promising features in terms of weight, strength and thermal management properties.
That said, magnesium-aluminium alloys showcase a susceptibility to corrosion in extreme environments. And in the case of EV battery housings, corrosion can become a major issue. Fortunately, advanced coating solutions can provide the necessary protections for magnesium-aluminium alloys to be successfully integrated into these housing components.
The design requirements of electric vehicle batteries
Thermal management
Lithium-ion batteries require thorough thermal management to maintain optimal operation over extended periods and maximise lifespan. They have an optimal operation temperature of 15 °C - 35 °C. Below this threshold, ionic conductivity is slowed and performance is reduced. Above this threshold, there is a reduction in lithium and active materials and energy capacity is lost, with an additional risk of thermal runaway and combustion at very high temperatures.
Weight optimisation
Driving range per charge has been a major barrier in widespread electrification, and EV design weight plays a significant role in maximising this energy efficiency. To achieve the same power output as fossil fuels, battery cells can be up to 100 times heavier in relation to energy capacity. Because of this, weight optimisation throughout the design of EVs has been a direct focus to maximise energy capacity and therefore driving range.
Corrosive protection
EV batteries face considerably corrosive environments over the course of their operation. In most EV designs, battery packs are a bed of cells that are positioned at the bottom of the vehicle design. Because of this, they face a number of corrosive elements such as salt, acidic rain and moisture penetration. Additionally, liquid cooling solutions for batteries can often exhibit a degree of leakage over their operation, which can lead to significant galvanic corrosion.
The benefits of using magnesium-aluminium alloys
Magnesium-aluminium alloys provide an innovative solution to the design requirements of EV battery housings.
Aluminium presents an impressive strength to weight ratio that has already seen widespread adoption in automotive, aerospace and other industries since the early 20th century. It also has excellent thermal conductivity (210 W/m-k) that enables thermal management properties via redirecting heat to dedicated cooling areas.
Magnesium is the lightest engineered metal on earth, with a density of 1.74 g/cm3 and a higher specific strength and stiffness than both steel and aluminium. It showcases flexibility and castability to provide a simple machining process, and also provides vibration dampening capabilities that can protect from additional factors such as wear.
The use of magnesium-aluminium based battery housings present weight savings of up to 40% when compared to aluminium designs. This is achieved without sacrificing component strength or thermal capabilities, aiding engineers in maximising energy efficiency without compromising on battery performance.
The remaining challenge of corrosion
The alloying of magnesium and aluminium brings benefits of strength, durability and weight optimisation. However, both metals exhibit a weakness in highly corrosive environments, which can lead to detrimental effects on battery housing components.
Magnesium is a highly reactive metal and is extremely susceptible to corrosion. Alloying with aluminium helps to negate this susceptibility as it has a naturally resistant oxide film, protecting it from most conditions. But when it comes to the constant and harsh corrosive conditions faced by EVs, magnesium-aluminium housings fail to provide sufficient corrosion resistance.
Moisture penetration, acidic rain and nanofluids in coolant solutions can all lead to the corrosion of magnesium-aluminium components by reacting with the outer oxide film. This is especially the case in acidic and alkaline conditions, as well as with high temperatures that often take place surrounding battery components.
Plasma Electrolytic Oxidation - a solution in corrosive conditions
Fortunately, advanced surface coating solutions can provide light metals such as aluminium and magnesium with enhanced corrosion resistance, along with many other improved surface properties. Plasma Electrolytic Oxidation (PEO) utilises an electrolyte bath process where high and controlled voltages produce an outer ceramic layer on a component’s substrate. This layer provides excellent resistances in relation to thermal, wear, corrosion and many other factors.
For magnesium-aluminium alloys being used as EV battery housings, PEO provides the protective characteristics to ensure prolonged component lifespan as well as the functionality of the batteries themselves. Moreover, PEO also enables the integration of lighter metals in areas where heavier metals would traditionally be used, helping to reduce the overall weight of designs.
Successfully integrate light metal alloys into your EV design with Keronite
Magnesium-aluminium alloys present promising features and benefits when used in battery housing components. Their lightweight yet strong characteristics makes it an attractive choice for designers, but the alloy’s susceptibility to corrosion can make it difficult to integrate.
Keronite’s PEO process provides light metals and alloys with a list of enhanced surface characteristics to prolong component life in the most extreme of environments. The electrolyte solution also provides bespoke capabilities via a customised mixture of regents; so no matter your design, we can help you achieve the surface properties you need.
To find out more about PEO, how it can optimise your designs and its ability to extend the lifespan of your components, contact a member of our team today.
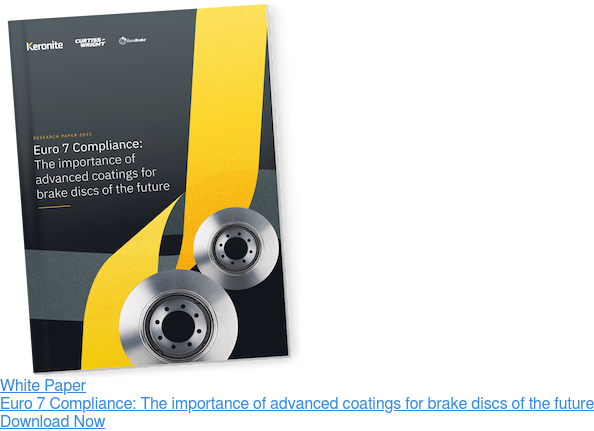
