Improving component life with PEO
13 July 2022Component lifespan has dictated the metals used in designs for decades. Industries such as automotive and aerospace rely on components that are robust and operate for thousands of hours without the need for repair or replacement. Light metals are notorious for being weak to environmental and industrial factors like corrosion, temperature and wear, resulting in a shorter lifespan when used in components; Even if metals like aluminium or magnesium can provide better fuel efficiency to designs, they simply cannot perform under the elements like heavier metals can.
Fortunately, the development of modern surface coating technologies has made the use of lighter metals in these applications a reality. Conventional methods such as hard anodising have helped introduce the application of light metals through the years, but Plasma Electrolytic Oxidation (PEO) is leading the charge in providing revolutionary design possibilities to designers. But why is PEO better at improving component life when compared to alternatives and how does it achieve this?
Traditional coatings and their features
Anodizing
Anodizing is a conventional method of metal surface coating that has been used for almost a century. It converts the surface of aluminium using an electrolyte bath and electric current into a resistant anodic layer. This protective coating provides significant temperature and corrosion resistance that can be hardened using higher temperatures.
Adversely, the coating growth mechanism of anodizing often causes through-thickness cracks or fissures in the protective layer of the coating, fatiguing the strength of components and negatively impacting component life.
Nitriding
Nitriding is a heat hardening treatment that involves diffusing nitrogen onto the surface of a metal to create a case-hardened outer layer. This outer layer provides effective wear resistance from corrosion and abrasion, helping to extend component life.
Nitriding can enhance metals like titanium, but can end up being problematic for other light metals that are more susceptible to heat. Nitriding typically uses temperatures above 540ºC and is unsuitable for most light alloys as it can cause thermal distortion, which can be problematic for precise designs.
Electroless Nickel
Electroless nickel is the process of depositing a nickel-alloy as a surface coating of a substrate using a chemical bath. It provides high hardness, natural lubricity and good wear/abrasion resistance, making it suitable for many sliding wear applications.
The main disadvantage of electroless nickel is that it can be difficult to apply, and if not applied correctly can cause significant corrosion damage. The application surface needs to be free of any surface contaminants to successfully plate the metal, and if not done correctly can result in rapid corrosion to the substrate through pores and breaches of the coating. This makes the process expensive and necessitates quality inspection for each part; a significant time expense.
Plasma Electrolytic Oxidation
Plasma Electrolytic Oxidation (PEO) is a surface coating technology that creates protective ceramic layers on the surface of light metals and alloys. The process involves submerging the metal in an electrolyte bath that creates plasma discharges on the substrate’s surface when a current is introduced. Specific reagents can also be introduced during the process to provide differing performance characteristics such as greater hardness, temperature protection or corrosion resistance.
PEO uniquely enhances the performance of light alloys by improving the lifespan across aluminium, titanium and magnesium based components. Its surface coating is two to four times the hardness of steel and anodising coatings, and also provides better coverage and uniformity around complex shapes than alternative technologies. This provides excellent wear and corrosion resistance whilst preventing the risk of cracks and fissures fatiguing the strength of the metal. PEO also enables experienced scientists to choose specific reagents to introduce in the coating, allowing them to maximise the lifespan of components specifically in the application at hand.
Extending component life with Keronite
Where harder metals were once a standard for high-stress environments, Plasma Electrolytic Oxidation is able to introduce the option of lighter metals into designs without jeopardising component lifespan. It is proven to offer more resistance and protection than alternative coating methods, and offers personalised resistance against application specific factors such as water corrosion or engine heat.
Keronite are the world leaders in PEO. Our PEO-dedicated materials scientists have helped prolong component life across a wide range of industries such as aerospace, automotive and defence. Our engineers work directly with designers to provide coating solutions that enable the use of aluminium, magnesium and titanium without compromising component life.
To find out more about the PEO process and its impact on the lifespan of components, read our full whitepaper below.
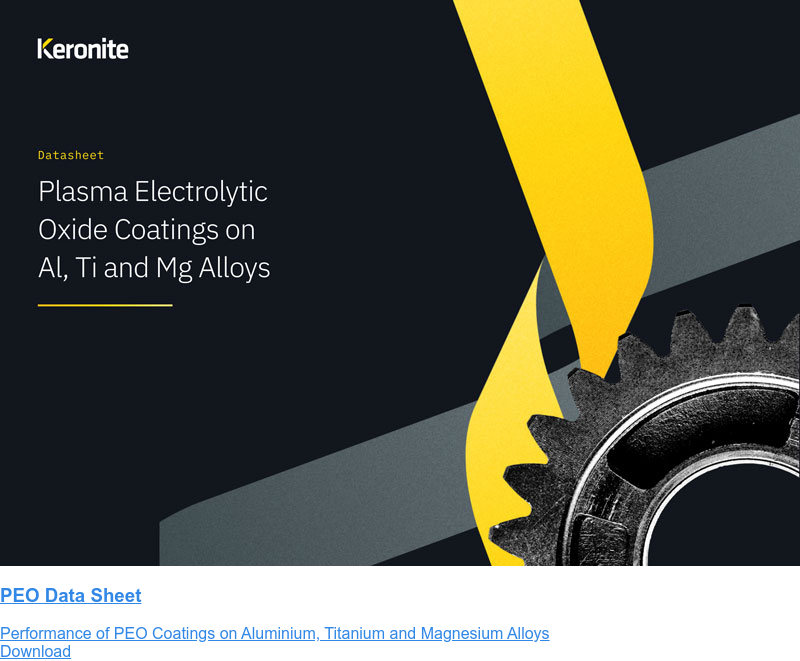
